Company Size
1,000+
Region
- America
Country
- United States
Product
- Blue Yonder’s transportation modeling
Tech Stack
- Transportation modeling
Implementation Scale
- Enterprise-wide Deployment
Impact Metrics
- Cost Savings
Technology Category
- Analytics & Modeling - Predictive Analytics
Applicable Industries
- Retail
Applicable Functions
- Logistics & Transportation
Use Cases
- Fleet Management
- Supply Chain Visibility
Services
- Data Science Services
- System Integration
About The Customer
Wegmans is a family-owned supermarket chain headquartered in Rochester, NY. With over 100 stores across the northeast and midAtlantic states and almost $10 billion in revenue, Wegmans is both one of the largest private companies in the U.S. and a customer favorite for its European-like open-air market displays and broad selection of organics, vegan offerings and restaurant-quality prepared foods. They pride themselves on a “near telepathic” level of customer service. To get all of those fresh, frozen and dry foods and ingredients to their network of stores, Wegmans employs a private fleet.
The Challenge
Wegmans, a family-owned supermarket chain with over 100 stores across the northeast and midAtlantic states, operates a private fleet to transport fresh, frozen, and dry foods and ingredients to their network of stores. However, with a network of this size and complexity, Wegmans wondered if they were getting the most utility possible from their fleet investments. The challenges they faced included tight store delivery windows, which limited opportunities for order consolidation or routing options, routing restrictions by type of commodity being shipped, and virtually no visibility to cost savings available from the use of backhauls.
The Solution
Wegmans turned to logistics consulting firm, enVista, and Blue Yonder’s transportation modeling capabilities to help them model potential transportation strategies. Blue Yonder’s modeling was utilized to model the complexities of Wegman’s transportation network. Its extensive functionality enabled enVista to accurately capture multiple constraints and parameters in Wegman’s network and allowed efficient and accurate future state analyses. enVista used Blue Yonder’s transportation modeling capabilities to measure the impact of adjusting the delivery windows by three hours to enable order consolidation and routing opportunities to be evaluated. They also used the Blue Yonder modeling capabilities to analyze different combinations of commodity groups during routing while still abiding by restrictions such as maintaining product temperature and humidity limitations that required certain types of vehicles. Finally, Blue Yonder’s modeling capabilities enabled enVista to analyze Wegmans’ current and potential backhaul vendors to see where additional opportunities for cost savings might exist.
Operational Impact
Quantitative Benefit
Case Study missing?
Start adding your own!
Register with your work email and create a new case study profile for your business.
Related Case Studies.
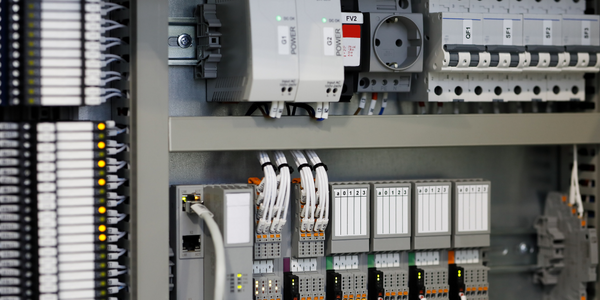
Case Study
Improving Production Line Efficiency with Ethernet Micro RTU Controller
Moxa was asked to provide a connectivity solution for one of the world's leading cosmetics companies. This multinational corporation, with retail presence in 130 countries, 23 global braches, and over 66,000 employees, sought to improve the efficiency of their production process by migrating from manual monitoring to an automatic productivity monitoring system. The production line was being monitored by ABB Real-TPI, a factory information system that offers data collection and analysis to improve plant efficiency. Due to software limitations, the customer needed an OPC server and a corresponding I/O solution to collect data from additional sensor devices for the Real-TPI system. The goal is to enable the factory information system to more thoroughly collect data from every corner of the production line. This will improve its ability to measure Overall Equipment Effectiveness (OEE) and translate into increased production efficiencies. System Requirements • Instant status updates while still consuming minimal bandwidth to relieve strain on limited factory networks • Interoperable with ABB Real-TPI • Small form factor appropriate for deployment where space is scarce • Remote software management and configuration to simplify operations
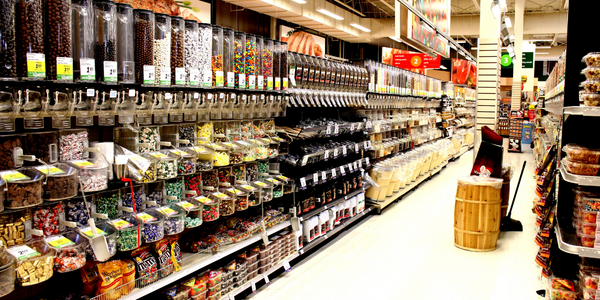
Case Study
How Sirqul’s IoT Platform is Crafting Carrefour’s New In-Store Experiences
Carrefour Taiwan’s goal is to be completely digital by end of 2018. Out-dated manual methods for analysis and assumptions limited Carrefour’s ability to change the customer experience and were void of real-time decision-making capabilities. Rather than relying solely on sales data, assumptions, and disparate systems, Carrefour Taiwan’s CEO led an initiative to find a connected IoT solution that could give the team the ability to make real-time changes and more informed decisions. Prior to implementing, Carrefour struggled to address their conversion rates and did not have the proper insights into the customer decision-making process nor how to make an immediate impact without losing customer confidence.
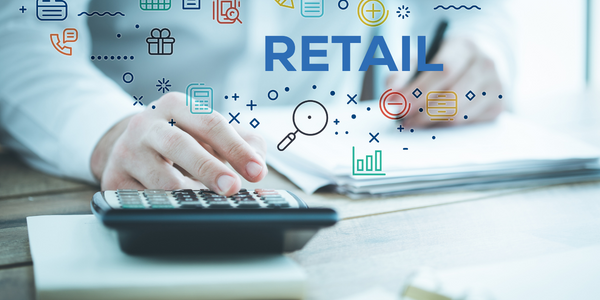
Case Study
Digital Retail Security Solutions
Sennco wanted to help its retail customers increase sales and profits by developing an innovative alarm system as opposed to conventional connected alarms that are permanently tethered to display products. These traditional security systems were cumbersome and intrusive to the customer shopping experience. Additionally, they provided no useful data or analytics.
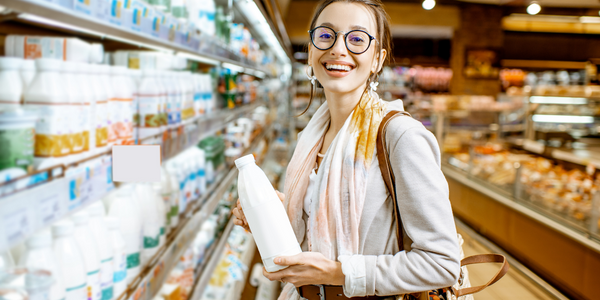
Case Study
Ensures Cold Milk in Your Supermarket
As of 2014, AK-Centralen has over 1,500 Danish supermarkets equipped, and utilizes 16 operators, and is open 24 hours a day, 365 days a year. AK-Centralen needed the ability to monitor the cooling alarms from around the country, 24 hours a day, 365 days a year. Each and every time the door to a milk cooler or a freezer does not close properly, an alarm goes off on a computer screen in a control building in southwestern Odense. This type of alarm will go off approximately 140,000 times per year, equating to roughly 400 alarms in a 24-hour period. Should an alarm go off, then there is only a limited amount of time to act before dairy products or frozen pizza must be disposed of, and this type of waste can quickly start to cost a supermarket a great deal of money.
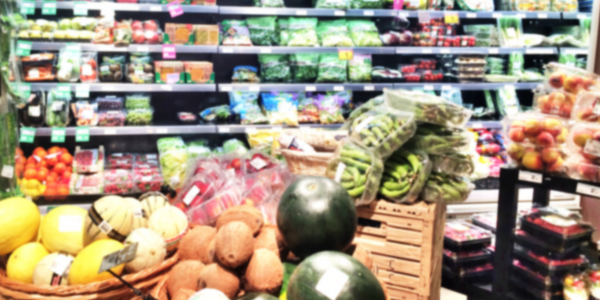
Case Study
Supermarket Energy Savings
The client had previously deployed a one-meter-per-store monitoring program. Given the manner in which energy consumption changes with external temperature, hour of the day, day of week and month of year, a single meter solution lacked the ability to detect the difference between a true problem and a changing store environment. Most importantly, a single meter solution could never identify root cause of energy consumption changes. This approach never reduced the number of truck-rolls or man-hours required to find and resolve issues.