Company Size
1,000+
Region
- America
- Europe
Country
- United Kingdom
- United States
Product
- JDA® Build to Order
Tech Stack
- Automated decision-support tool
Implementation Scale
- Enterprise-wide Deployment
Impact Metrics
- Cost Savings
- Customer Satisfaction
- Productivity Improvements
Technology Category
- Functional Applications - Manufacturing Execution Systems (MES)
Applicable Industries
- Automotive
Applicable Functions
- Discrete Manufacturing
- Logistics & Transportation
Use Cases
- Manufacturing System Automation
- Supply Chain Visibility
About The Customer
Headquartered in Gillingham, England, Delphi Automotive PLC is a leading supplier of technologies for the worldwide automotive and commercial vehicle markets. The company’s Electrical/Electronic Architecture business unit provides complete design of vehicles’ electrical architecture, including connectors, wiring assemblies and harnesses, electrical centers, and hybrid high voltage and safety distribution systems. Delphi has manufacturing plants worldwide, as well as a network of third-party manufacturing partners.
The Challenge
Delphi Automotive PLC, a key supplier to the world’s leading automakers, faced the challenge of incorporating increased delivery speed and product customization into its operations. The company assembles and delivers critical components to automotive OEM assembly lines, in a predefined sequence at short notice. This is particularly challenging due to the complexity of Delphi’s products. For instance, a single electrical harness may be composed of hundreds of miles of wire, connecting to thousands of points within the vehicle. Delphi recognized the need for an automated decision-support tool to help it support these increasingly complex build-to-order requirements.
The Solution
Delphi chose to implement JDA Build to Order from JDA Software’s Manufacturing Planning suite of solutions to address this challenge. The solution considers every possible way of fulfilling a given customer order by exploring a variety of production plans and manufacturing sites, enabling Delphi to determine the fastest, most cost-efficient way to meet each customer’s needs. JDA Build to Order receives each customer order electronically, then maps the most efficient, low-cost pathway across Delphi’s many production steps. These steps typically include cutting wire (KAN BAN), assembling harness “kits,” performing final assembly according to each customer’s unique Vehicle Order Number, conducting a couple of testing steps including electrical testing, and finally packaging products based on exacting customer specifications.
Operational Impact
Quantitative Benefit
Case Study missing?
Start adding your own!
Register with your work email and create a new case study profile for your business.
Related Case Studies.
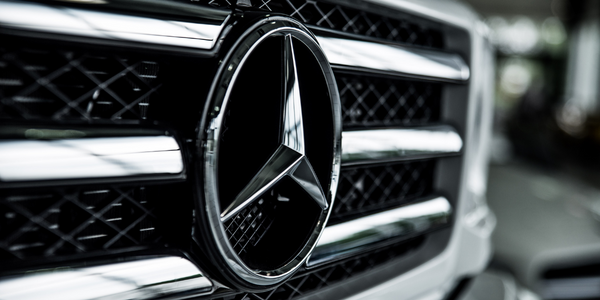
Case Study
Integral Plant Maintenance
Mercedes-Benz and his partner GAZ chose Siemens to be its maintenance partner at a new engine plant in Yaroslavl, Russia. The new plant offers a capacity to manufacture diesel engines for the Russian market, for locally produced Sprinter Classic. In addition to engines for the local market, the Yaroslavl plant will also produce spare parts. Mercedes-Benz Russia and his partner needed a service partner in order to ensure the operation of these lines in a maintenance partnership arrangement. The challenges included coordinating the entire maintenance management operation, in particular inspections, corrective and predictive maintenance activities, and the optimizing spare parts management. Siemens developed a customized maintenance solution that includes all electronic and mechanical maintenance activities (Integral Plant Maintenance).
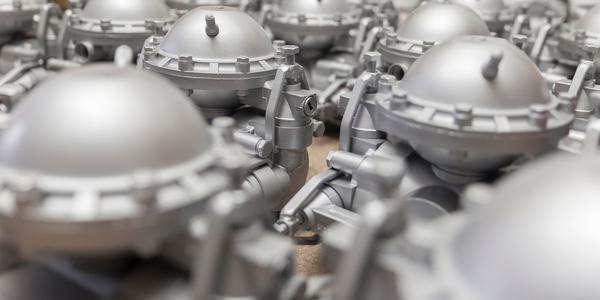
Case Study
Monitoring of Pressure Pumps in Automotive Industry
A large German/American producer of auto parts uses high-pressure pumps to deburr machined parts as a part of its production and quality check process. They decided to monitor these pumps to make sure they work properly and that they can see any indications leading to a potential failure before it affects their process.