Company Size
11-200
Region
- America
Country
- United States
Product
- DTR
Tech Stack
- ERP
Implementation Scale
- Enterprise-wide Deployment
Impact Metrics
- Cost Savings
- Customer Satisfaction
- Productivity Improvements
Technology Category
- Functional Applications - Enterprise Resource Planning Systems (ERP)
Applicable Industries
- Plastics
Applicable Functions
- Discrete Manufacturing
- Sales & Marketing
Use Cases
- Inventory Management
- Manufacturing System Automation
Services
- System Integration
About The Customer
Dreco Incorporated is a family-owned company that manufactures injection molded plastic parts primarily for the vacuum cleaner industry. The company, which is currently run by the third generation, offers a large product line with more than 800 hose end types and a full line of vacuum attachments. Dreco serves the needs of several industries, including lawn and garden, health care, industrial cleaning, consumer products, and automotive. The company is based in Cleveland, Ohio.
The Challenge
Dreco Incorporated, a manufacturer of injection molded plastic parts, was struggling with an outdated ERP system that was not designed to account for sales orders in real time or effectively manage data on prospective sales. The system required constant updates and was not user-friendly. Dreco needed a software solution that could handle the unique requirements of a plastics processor, including accounting for parts weighing as little as a few grams. The company also wanted a system that could seamlessly integrate all its business operations.
The Solution
After conducting thorough research on a variety of competitive industry products, Dreco selected DTR, a product of more than 20 years of plastics-focused software development. DTR was designed to provide industry-specific manufacturing, distribution, and financial management solutions that address the unique system requirements of plastics processors. Once installed, DTR enabled Dreco’s management to predict required materials and subcomponents based on scheduled production, sales orders, and backorders. DTR also generates forward finite, queued, and just-in-time scheduling for all workstations and/or secondary operations. Users have the option of basing schedules on sales orders, forecasts, release orders, electronic data interchange (EDI), manual assignments, consolidations, and/or reorder points.
Operational Impact
Quantitative Benefit
Case Study missing?
Start adding your own!
Register with your work email and create a new case study profile for your business.
Related Case Studies.

Case Study
Plastic Spoons Case study: Injection Moulding
In order to meet customer expectations by supplying a wide variety of packaging units, from 36 to 1000 spoons per package, a new production and packaging line needed to be built. DeSter wanted to achieve higher production capacity, lower cycle time and a high degree of operator friendliness with this new production line.
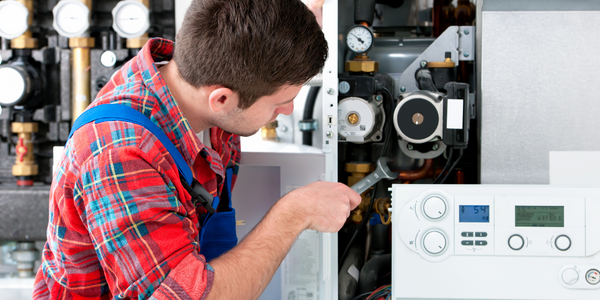
Case Study
Boiler Control System for Plastic Manufacturing Applications
Factory automation applications must be equipped to handle and monitor the myriads of information from attached devices. For plastic manufacturing applications, the boiler control system plays a critical role by gathering and regulating information to ensure production is accurate and smooth. In this particular case, the customer combines eight subsystems that include power meters, water meters, alarm output, displays, and I/O status to be controlled by several intelligent controllers with Modbus RTU interface. The Modbus TCP protocol is used for this application due to the distance. System Requirements: • Modbus serial to Modbus TCP translation • Multiple slaves/masters support • Automatic Modbus TCP response time detection
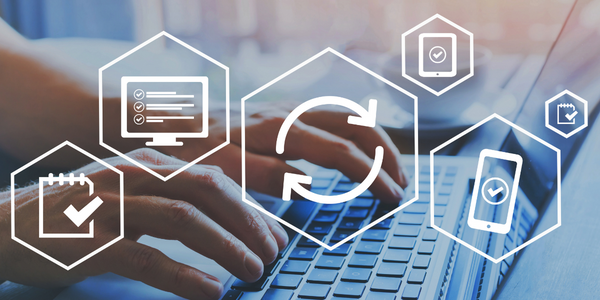
Case Study
Ascend Performance Materials Case Study
Ascend operations must access multiple software systems to manage day-to-day operations in an effective and secure manner. These systems generate large sets of data which contain critical information pertaining to management systems, planning and cost information in business systems and energy consumption. As a result, Ascend management was challenged with creating relevant reports reflecting performance measures in overall context of their operational process. The company’s previous process entailed collecting and analyzing data manually which was not effective, since the information collected was generated after the fact, and was too complex for collaborative use across the organization.
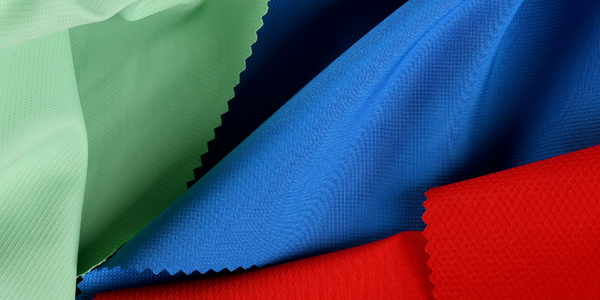
Case Study
Remake Enterprise-to-production System
The client was running a legacy material flow tracking system and wanted to replace the system with a more effective one as the system was increasingly expensive to maintain and support and also was not extendable. The client's IT landscape was filled with modern applications and it was difficult to interface the material flow tracking system with modern applications.