Domino’s Pizza uses Opti-Time to organize the routes for supplying its local branches.
Company Size
1,000+
Country
- France
- United States
Product
- Opti-Time
Tech Stack
- Route Optimization Software
- Traffic Software
Implementation Scale
- Enterprise-wide Deployment
Impact Metrics
- Cost Savings
- Customer Satisfaction
- Productivity Improvements
Technology Category
- Functional Applications - Fleet Management Systems (FMS)
- Functional Applications - Remote Monitoring & Control Systems
Applicable Industries
- Food & Beverage
- Retail
Applicable Functions
- Logistics & Transportation
- Warehouse & Inventory Management
Use Cases
- Fleet Management
- Supply Chain Visibility
Services
- Software Design & Engineering Services
- System Integration
About The Customer
Domino’s Pizza is a global leader in pizza delivery and takeaway services, founded in 1960. The company operates more than 17,000 stores in over 90 countries, selling an average of 3 million pizzas a day. Domino’s is known for using fresh dough that has never been frozen, and it offers pizzas made to order. The company has a strong presence worldwide, with more than half of its sales coming from outside the United States. Domino’s operates a network of franchised pizza delivery and takeaway sales outlets, supported by numerous production and logistics centers. These centers produce fresh pizza dough and other food products, which are then transported to the sales outlets multiple times a week. The company is committed to maintaining the cold chain during delivery to ensure product quality.
The Challenge
The challenge for Domino's Pizza: Optimizing the management of the supply route itineraries of its countless sales outlets. Domino’s Pizza operates a network of franchised pizza delivery and takeaway sales outlets. The brand is one of the only ones to use fresh dough for its pizzas that is guaranteed never to have been frozen and offers pizzas made to order, currently positioning itself as the leader in the delivered and takeaway pizza market. Domino’s Pizza has many productions and logistics centers where it produces the fresh pizza dough and provides other food products (salads and desserts) and merchandising (caps, t-shirts). These products are ordered by the network’s various sales outlets via a buying hub and are then transported to the outlets two or three times a week. Each vehicle is responsible for one supply route. On average, it carries 3 to 4 loads of fresh and dry ingredients and between 6 and 8 stacks of pizza dough platters, which requires controlled temperature delivery in order to maintain the cold chain throughout the route. To sustain its strong growth worldwide, Domino’s Pizza wanted to optimize its supply route organization so as to be able to respond efficiently to the challenges associated with the increased order volume. The brand was looking to be able to incorporate into its information system a solution that allows the definition of logical route itineraries and reduces the travel time of each transport movement to all its outlets in all strategic territories in which the company’s activities are experiencing rapid growth. All the deliveries, necessary parameters such as for these the characteristics of the ordered products, the volume they occupy, and the location of the sales outlets to be supplied also had to be included in the tool.
The Solution
Opti-Time tailored response. After studying feedback from other users, Domino’s Pizza decides to turn to Opti-Time and quickly opted to implement the route optimization solution. This tool enables the daily management of the supply route itineraries of its outlets to be automated and optimized. Opti-Time with the traffic software most provides Domino’s Pizza profitable and logical organization and routes in real-time, taking account of constraints and each sales outlet’s timetabling requirements (day or night-time delivery, opening hours, accessibility). The delivery staff responsible for the supply routes can thus reduce the time spent on the road, have better control over the regularity of delivery hours and increase the number of deliveries completed per day. Optimal reliability of route organization for higher productivity and lower transport costs. By installing the Opti-Time software suite, the drivers responsible for the supply routes now have 100% reliable and logical routes with no excess mileage added, optimal vehicle loading rate based on the orders and better overall visibility. Domino’s reward: travel time productivity gains of 25%. In addition to improving delivery staff efficiency, The routing software enables a fully capable configuration of operational costs. Domino’s Pizza has indeed reduced 15% of its transport costs compared with the previous financial year. Encouraged by this success, Domino’s Pizza is planning to extend the use of the routing & scheduling solution by applying it to the supply routes for outlets located in lower priority markets such developing economies.
Operational Impact
Quantitative Benefit
Case Study missing?
Start adding your own!
Register with your work email and create a new case study profile for your business.
Related Case Studies.

Case Study
The Kellogg Company
Kellogg keeps a close eye on its trade spend, analyzing large volumes of data and running complex simulations to predict which promotional activities will be the most effective. Kellogg needed to decrease the trade spend but its traditional relational database on premises could not keep up with the pace of demand.

Case Study
HEINEKEN Uses the Cloud to Reach 10.5 Million Consumers
For 2012 campaign, the Bond promotion, it planned to launch the campaign at the same time everywhere on the planet. That created unprecedented challenges for HEINEKEN—nowhere more so than in its technology operation. The primary digital content for the campaign was a 100-megabyte movie that had to play flawlessly for millions of viewers worldwide. After all, Bond never fails. No one was going to tolerate a technology failure that might bruise his brand.Previously, HEINEKEN had supported digital media at its outsourced datacenter. But that datacenter lacked the computing resources HEINEKEN needed, and building them—especially to support peak traffic that would total millions of simultaneous hits—would have been both time-consuming and expensive. Nor would it have provided the geographic reach that HEINEKEN needed to minimize latency worldwide.
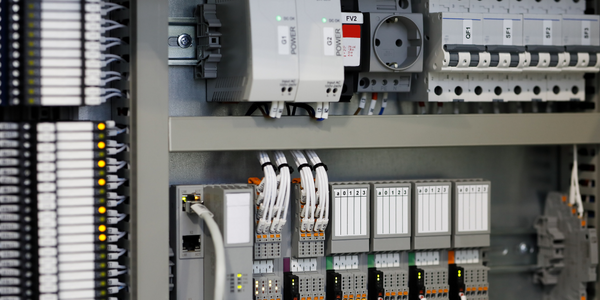
Case Study
Improving Production Line Efficiency with Ethernet Micro RTU Controller
Moxa was asked to provide a connectivity solution for one of the world's leading cosmetics companies. This multinational corporation, with retail presence in 130 countries, 23 global braches, and over 66,000 employees, sought to improve the efficiency of their production process by migrating from manual monitoring to an automatic productivity monitoring system. The production line was being monitored by ABB Real-TPI, a factory information system that offers data collection and analysis to improve plant efficiency. Due to software limitations, the customer needed an OPC server and a corresponding I/O solution to collect data from additional sensor devices for the Real-TPI system. The goal is to enable the factory information system to more thoroughly collect data from every corner of the production line. This will improve its ability to measure Overall Equipment Effectiveness (OEE) and translate into increased production efficiencies. System Requirements • Instant status updates while still consuming minimal bandwidth to relieve strain on limited factory networks • Interoperable with ABB Real-TPI • Small form factor appropriate for deployment where space is scarce • Remote software management and configuration to simplify operations

Case Study
Energy Management System at Sugar Industry
The company wanted to use the information from the system to claim under the renewable energy certificate scheme. The benefit to the company under the renewable energy certificates is Rs 75 million a year. To enable the above, an end-to-end solution for load monitoring, consumption monitoring, online data monitoring, automatic meter data acquisition which can be exported to SAP and other applications is required.
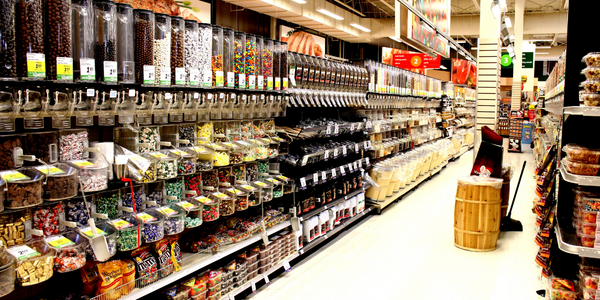
Case Study
How Sirqul’s IoT Platform is Crafting Carrefour’s New In-Store Experiences
Carrefour Taiwan’s goal is to be completely digital by end of 2018. Out-dated manual methods for analysis and assumptions limited Carrefour’s ability to change the customer experience and were void of real-time decision-making capabilities. Rather than relying solely on sales data, assumptions, and disparate systems, Carrefour Taiwan’s CEO led an initiative to find a connected IoT solution that could give the team the ability to make real-time changes and more informed decisions. Prior to implementing, Carrefour struggled to address their conversion rates and did not have the proper insights into the customer decision-making process nor how to make an immediate impact without losing customer confidence.