Technology Category
- Functional Applications - Manufacturing Execution Systems (MES)
Applicable Industries
- Equipment & Machinery
Applicable Functions
- Logistics & Transportation
- Product Research & Development
Use Cases
- Additive Manufacturing
- Manufacturing Process Simulation
Services
- System Integration
About The Customer
Carrier is a leading manufacturer of products across three primary market segments: HVAC (both residential and commercial), refrigeration, and fire/security. The company generates nearly $20 billion in sales and employs 50,000 people. Carrier's products require different manufacturing processes including casting, sheet metal bending, wire harnesses, PCB assembly, and additive manufacturing. The company's cost engineering group works directly with design engineers and supply chain representatives throughout the organization to identify cost drivers and the potential for value-driven improvements.
The Challenge
Carrier, a manufacturer of products across HVAC, refrigeration, and fire/security segments, faced a significant challenge in modeling manufacturing costs for complex parts requiring multiple manufacturing processes. The company's cost engineering group was tasked with optimizing product cost and value through improved supplier negotiation and cost-effective design. However, traditional tools like Excel spreadsheets or traditional cost estimation software were not well-suited to generating accurate manufacturing cost models for this high-tolerance, multi-faceted production process. Precisely modeling manufacturing costs for this assembly without the capability to analyze an actual 3D model was simply not possible. Additionally, Carrier was also aiming to meet their emissions reduction goals, which required a detailed understanding of the carbon emissions associated with their manufacturing processes.
The Solution
Carrier implemented aPriori, a technology that allowed them to automate the process of generating 'should cost' models for their diverse range of products. The company's cross-functional should cost team used aPriori to tackle a wide range of manufacturing cost modeling projects. They utilized over 80 digital factories in their aPriori implementation, generating should cost models across the full range of manufacturing processes required by their products. In addition to utilizing customizable digital factories, they developed several in-house manufacturing cost models to reflect some of Carrier’s unique designs and production requirements. aPriori’s configurable digital factory approach allowed Carrier’s should cost professionals to build detailed, highly accurate models of suppliers’ costs for rotor manufacturing. These manufacturing cost models were based on the precise tolerances required by Carrier for every aspect of the design. Furthermore, Carrier used aPriori as a critical tool in its mission to achieve a gigaton in carbon emissions reduction by 2030.
Operational Impact
Quantitative Benefit
Case Study missing?
Start adding your own!
Register with your work email and create a new case study profile for your business.
Related Case Studies.

Case Study
Smart Water Filtration Systems
Before working with Ayla Networks, Ozner was already using cloud connectivity to identify and solve water-filtration system malfunctions as well as to monitor filter cartridges for replacements.But, in June 2015, Ozner executives talked with Ayla about how the company might further improve its water systems with IoT technology. They liked what they heard from Ayla, but the executives needed to be sure that Ayla’s Agile IoT Platform provided the security and reliability Ozner required.

Case Study
IoT enabled Fleet Management with MindSphere
In view of growing competition, Gämmerler had a strong need to remain competitive via process optimization, reliability and gentle handling of printed products, even at highest press speeds. In addition, a digitalization initiative also included developing a key differentiation via data-driven services offers.
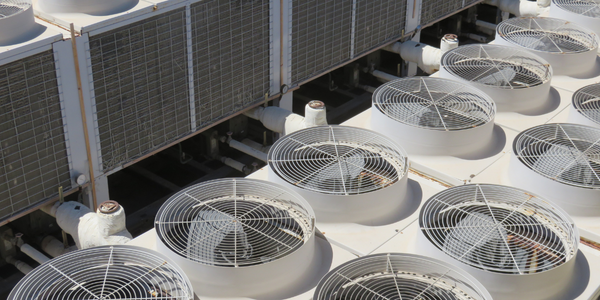
Case Study
Predictive Maintenance for Industrial Chillers
For global leaders in the industrial chiller manufacturing, reliability of the entire production process is of the utmost importance. Chillers are refrigeration systems that produce ice water to provide cooling for a process or industrial application. One of those leaders sought a way to respond to asset performance issues, even before they occur. The intelligence to guarantee maximum reliability of cooling devices is embedded (pre-alarming). A pre-alarming phase means that the cooling device still works, but symptoms may appear, telling manufacturers that a failure is likely to occur in the near future. Chillers who are not internet connected at that moment, provide little insight in this pre-alarming phase.

Case Study
Premium Appliance Producer Innovates with Internet of Everything
Sub-Zero faced the largest product launch in the company’s history:It wanted to launch 60 new products as scheduled while simultaneously opening a new “greenfield” production facility, yet still adhering to stringent quality requirements and manage issues from new supply-chain partners. A the same time, it wanted to increase staff productivity time and collaboration while reducing travel and costs.

Case Study
Integration of PLC with IoT for Bosch Rexroth
The application arises from the need to monitor and anticipate the problems of one or more machines managed by a PLC. These problems, often resulting from the accumulation over time of small discrepancies, require, when they occur, ex post technical operations maintenance.
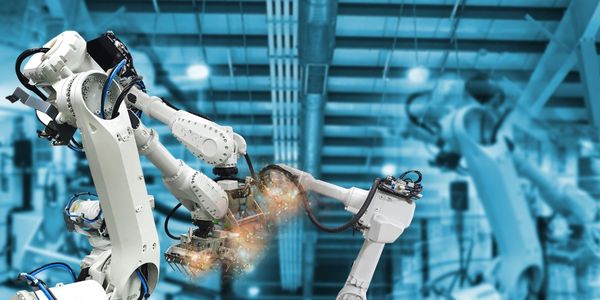
Case Study
Robot Saves Money and Time for US Custom Molding Company
Injection Technology (Itech) is a custom molder for a variety of clients that require precision plastic parts for such products as electric meter covers, dental appliance cases and spools. With 95 employees operating 23 molding machines in a 30,000 square foot plant, Itech wanted to reduce man hours and increase efficiency.