Developing Innovative Design Concepts Faster with SOLIDWORKS Visualize
Customer Company Size
SME
Region
- Europe
Country
- France
Product
- SOLIDWORKS Visualize
- Keyshot
- Maxwell
- Octane
- Flamingo
Tech Stack
- 3D Rendering Software
- Photorealistic Rendering
- CAD Integration
Implementation Scale
- Enterprise-wide Deployment
Impact Metrics
- Cost Savings
- Productivity Improvements
- Customer Satisfaction
Technology Category
- Analytics & Modeling - Predictive Analytics
- Application Infrastructure & Middleware - Data Visualization
- Functional Applications - Product Lifecycle Management Systems (PLM)
Applicable Industries
- Consumer Goods
- Automotive
Applicable Functions
- Product Research & Development
- Quality Assurance
- Sales & Marketing
Use Cases
- Visual Quality Detection
- Digital Twin
- Virtual Prototyping & Product Testing
Services
- Software Design & Engineering Services
- System Integration
- Training
About The Customer
ZAMAK design is a leading French industrial design studio driven by the creativity of four experienced designers: Nicolas Michel-Imbert, Florian Foizon, Damien Esclasse, and Arnaud Perez. The team is formally trained in industrial design and brings diverse expertise and multidisciplinary skills to creating innovative solutions for their clients' product development challenges. They work with an established network of partners specializing in engineering, set design, CAD, web development, and consulting to ensure successful project completion.
The Challenge
ZAMAK design needed to create realistic 3D renderings of innovative industrial design concepts quickly and easily for presentation to clients, promotion of new concepts, and marketing of products. The firm previously used the Keyshot rendering package but found it inefficient and lacking in quality. They required a solution that was fast, easy to use, and capable of producing high-quality, photorealistic renderings for a variety of projects.
The Solution
ZAMAK design implemented SOLIDWORKS Visualize 3D photorealistic rendering software after evaluating several alternatives, including Maxwell, Octane, Flamingo, and Lumion. They chose SOLIDWORKS Visualize for its balance of quality, speed, and ease of use. The software allows them to quickly change colors, materials, and lighting without losing render quality, significantly shortening design cycles. The easy-to-use interface and linked capabilities make it an invaluable tool for their design process, enabling them to produce high-quality renderings efficiently.
Operational Impact
Quantitative Benefit
Case Study missing?
Start adding your own!
Register with your work email and create a new case study profile for your business.
Related Case Studies.
.png)
Case Study
Improving Vending Machine Profitability with the Internet of Things (IoT)
The vending industry is undergoing a sea change, taking advantage of new technologies to go beyond just delivering snacks to creating a new retail location. Intelligent vending machines can be found in many public locations as well as company facilities, selling different types of goods and services, including even computer accessories, gold bars, tickets, and office supplies. With increasing sophistication, they may also provide time- and location-based data pertaining to sales, inventory, and customer preferences. But at the end of the day, vending machine operators know greater profitability is driven by higher sales and lower operating costs.
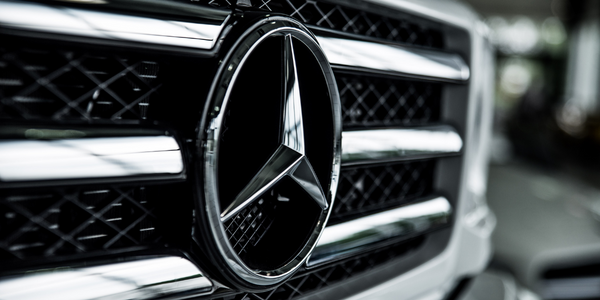
Case Study
Integral Plant Maintenance
Mercedes-Benz and his partner GAZ chose Siemens to be its maintenance partner at a new engine plant in Yaroslavl, Russia. The new plant offers a capacity to manufacture diesel engines for the Russian market, for locally produced Sprinter Classic. In addition to engines for the local market, the Yaroslavl plant will also produce spare parts. Mercedes-Benz Russia and his partner needed a service partner in order to ensure the operation of these lines in a maintenance partnership arrangement. The challenges included coordinating the entire maintenance management operation, in particular inspections, corrective and predictive maintenance activities, and the optimizing spare parts management. Siemens developed a customized maintenance solution that includes all electronic and mechanical maintenance activities (Integral Plant Maintenance).