Dennen Steel Finds the Solution for its Unique Business Processes
Customer Company Size
Large Corporate
Region
- America
Country
- United States
Product
- Microsoft Dynamics AX 2009
- RF-SMART
Tech Stack
- ERP
- Automated Data Collection (ADC)
- Handheld Devices
Implementation Scale
- Enterprise-wide Deployment
Impact Metrics
- Productivity Improvements
- Customer Satisfaction
Technology Category
- Functional Applications - Enterprise Resource Planning Systems (ERP)
- Functional Applications - Remote Monitoring & Control Systems
Applicable Functions
- Warehouse & Inventory Management
- Quality Assurance
Use Cases
- Inventory Management
- Process Control & Optimization
Services
- System Integration
- Training
About The Customer
Dennen Steel Corp. is a steel assembly, welding, and stamping manufacturer based in the United States. Founded in 1947 by two brothers from Grand Rapids, Michigan, the company initially focused on buying and selling scrap steel from World War II. Over the years, Dennen Steel has significantly expanded its operations, adding various manufacturing processes such as stamping, welding, and assembly. The company has also grown its geographic presence by opening manufacturing centers across the country, including locations in Burns Harbor, Indiana, and Iuka, Mississippi. With a focus on integrating its operations into a seamless supply chain, Dennen Steel aims to enhance visibility and data collection to support its business growth.
The Challenge
As Dennen Steel expanded its operations and added new manufacturing processes, the company faced significant challenges in integrating its operations into a seamless supply chain. The lack of visibility and limited data collection capabilities were major issues that needed to be addressed. The company recognized the need for an ERP and Automated Data Collection (ADC) solution to support its evolving business needs. The existing manual processes for inventory management and production tracking were inefficient and prone to errors, leading to inaccuracies and delays in operations.
The Solution
To address its challenges, Dennen Steel implemented Microsoft Dynamics AX 2009 as its ERP system and selected RF-SMART for Automated Data Collection (ADC). The decision was based on RF-SMART's certification with Dynamics AX and its proven integration capabilities. The implementation began in February 2011, and RF-SMART was able to meet the business needs of the manufacturing company from the start. One of the first areas to benefit from the implementation was the receiving department. With RF-SMART's ADC workflows, receiving personnel could enter inventory data using handheld devices, providing immediate updates and improving visibility. The solution also enhanced the company's ability to track production operations and finished goods in real-time, eliminating the need for manual tag writing and reducing errors. Additionally, RF-SMART's workflows were customized to handle specific processes like slitting, allowing for individual identification of co-products. The implementation led to significant productivity improvements and streamlined inventory management processes.
Operational Impact
Quantitative Benefit
Case Study missing?
Start adding your own!
Register with your work email and create a new case study profile for your business.
Related Case Studies.

Case Study
System 800xA at Indian Cement Plants
Chettinad Cement recognized that further efficiencies could be achieved in its cement manufacturing process. It looked to investing in comprehensive operational and control technologies to manage and derive productivity and energy efficiency gains from the assets on Line 2, their second plant in India.
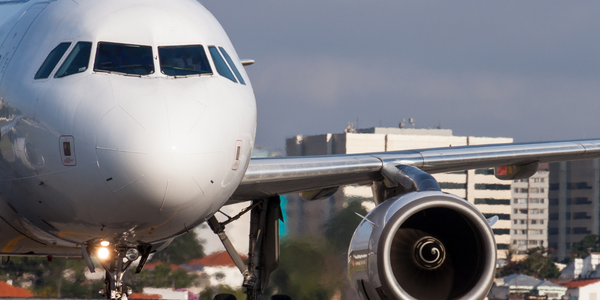
Case Study
Airbus Soars with Wearable Technology
Building an Airbus aircraft involves complex manufacturing processes consisting of thousands of moving parts. Speed and accuracy are critical to business and competitive advantage. Improvements in both would have high impact on Airbus’ bottom line. Airbus wanted to help operators reduce the complexity of assembling cabin seats and decrease the time required to complete this task.
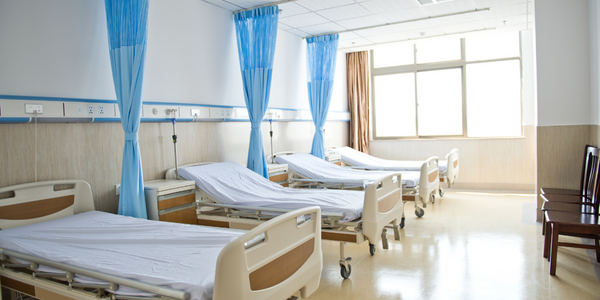
Case Study
Hospital Inventory Management
The hospital supply chain team is responsible for ensuring that the right medical supplies are readily available to clinicians when and where needed, and to do so in the most efficient manner possible. However, many of the systems and processes in use at the cancer center for supply chain management were not best suited to support these goals. Barcoding technology, a commonly used method for inventory management of medical supplies, is labor intensive, time consuming, does not provide real-time visibility into inventory levels and can be prone to error. Consequently, the lack of accurate and real-time visibility into inventory levels across multiple supply rooms in multiple hospital facilities creates additional inefficiency in the system causing over-ordering, hoarding, and wasted supplies. Other sources of waste and cost were also identified as candidates for improvement. Existing systems and processes did not provide adequate security for high-cost inventory within the hospital, which was another driver of cost. A lack of visibility into expiration dates for supplies resulted in supplies being wasted due to past expiry dates. Storage of supplies was also a key consideration given the location of the cancer center’s facilities in a dense urban setting, where space is always at a premium. In order to address the challenges outlined above, the hospital sought a solution that would provide real-time inventory information with high levels of accuracy, reduce the level of manual effort required and enable data driven decision making to ensure that the right supplies were readily available to clinicians in the right location at the right time.
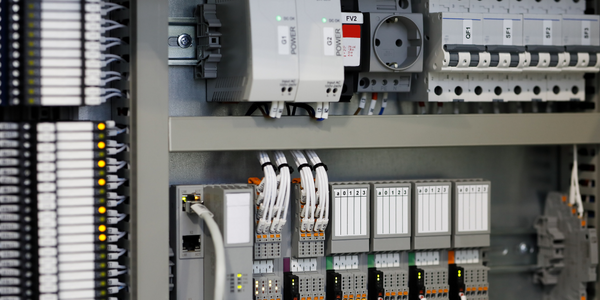
Case Study
Improving Production Line Efficiency with Ethernet Micro RTU Controller
Moxa was asked to provide a connectivity solution for one of the world's leading cosmetics companies. This multinational corporation, with retail presence in 130 countries, 23 global braches, and over 66,000 employees, sought to improve the efficiency of their production process by migrating from manual monitoring to an automatic productivity monitoring system. The production line was being monitored by ABB Real-TPI, a factory information system that offers data collection and analysis to improve plant efficiency. Due to software limitations, the customer needed an OPC server and a corresponding I/O solution to collect data from additional sensor devices for the Real-TPI system. The goal is to enable the factory information system to more thoroughly collect data from every corner of the production line. This will improve its ability to measure Overall Equipment Effectiveness (OEE) and translate into increased production efficiencies. System Requirements • Instant status updates while still consuming minimal bandwidth to relieve strain on limited factory networks • Interoperable with ABB Real-TPI • Small form factor appropriate for deployment where space is scarce • Remote software management and configuration to simplify operations