Customer Company Size
Large Corporate
Region
- Europe
Country
- Germany
Product
- FORCAM’s Advanced Shop Floor Management Technology
Tech Stack
- Real-time Machine Data Collection
- SAP ERP
Implementation Scale
- Enterprise-wide Deployment
Impact Metrics
- Productivity Improvements
- Waste Reduction
Technology Category
- Platform as a Service (PaaS) - Data Management Platforms
Applicable Industries
- Automotive
Applicable Functions
- Discrete Manufacturing
Use Cases
- Manufacturing System Automation
- Predictive Maintenance
Services
- System Integration
- Cloud Planning, Design & Implementation Services
About The Customer
Audi AG is a well-known car manufacturer in the automotive industry. The company is based in Ingolstadt, Germany and reported a revenue of 53.8 billion dollars in 2014. Audi's press plants in Ingolstadt and Neckarsulm are equipped with the Advanced Shop Floor Management Technology by FORCAM, which helped increase productivity by 20% during the first year of deployment. The company is known for its pioneering role in the industry and its distinctive design in aluminium and steel. Audi's press plants are one of the most efficient in the company, with more than 1,500 employees working with state-of-the-art press machinery. The company has seen a significant increase in the range of models available, which has implications for the manufacturing of car body panels.
The Challenge
Audi, a pioneering car manufacturer, operates press plants in Ingolstadt and Neckarsulm, Germany. The automotive industry has seen significant changes over the years, with niche products becoming increasingly important. To remain competitive, Audi needed to respond instantly to specific customer requests. The range of models available from Audi has increased, which has implications for the manufacturing of car body panels. It requires the production of more sophisticated pressed parts, involving the use of a wide range of tooling. This necessitates creating capacities and improving the efficiency and performance of the press plants. More than 1,500 employees work with state-of-the-art press machinery at Audi's plants. The independent subdivision is responsible for the distinctive Audi design in aluminium and steel, making it one of the most efficient plants in the whole company.
The Solution
FORCAM implemented its Advanced Shop Floor Management Technology in select press lines at the Ingolstadt and Neckarsulm press plant during the pilot phase in 2005. The modular composition of the solution simplified the gradual implementation of individual modules and allowed for smooth - continuous production. During the same year, FORCAM further rolled out deployment in a total of 33 press lines at Ingolstadt and an additional 15 at Neckarsulm. These press lines are now automatically monitored. Machine signals are captured, data collected and converted into meaningful metrics on any web-based device – not just from the shop floor. Shop floor workers can access these visualizations, analyze them and eliminate any deviation from the target. Access to data and information can be customized to each role, which allows for precise address to problems during production in real time. In addition, the solution offers through its standardized data model for comparisons and benchmarking of any plant in any location.
Operational Impact
Quantitative Benefit
Case Study missing?
Start adding your own!
Register with your work email and create a new case study profile for your business.
Related Case Studies.
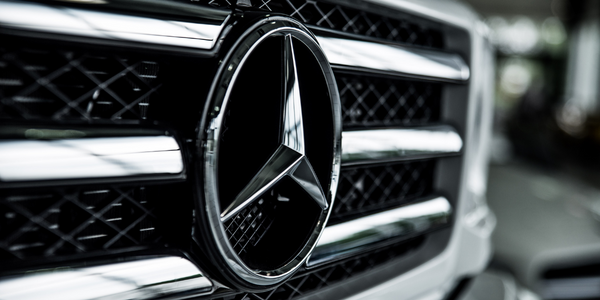
Case Study
Integral Plant Maintenance
Mercedes-Benz and his partner GAZ chose Siemens to be its maintenance partner at a new engine plant in Yaroslavl, Russia. The new plant offers a capacity to manufacture diesel engines for the Russian market, for locally produced Sprinter Classic. In addition to engines for the local market, the Yaroslavl plant will also produce spare parts. Mercedes-Benz Russia and his partner needed a service partner in order to ensure the operation of these lines in a maintenance partnership arrangement. The challenges included coordinating the entire maintenance management operation, in particular inspections, corrective and predictive maintenance activities, and the optimizing spare parts management. Siemens developed a customized maintenance solution that includes all electronic and mechanical maintenance activities (Integral Plant Maintenance).
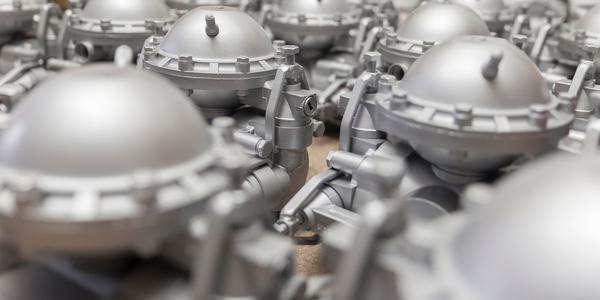
Case Study
Monitoring of Pressure Pumps in Automotive Industry
A large German/American producer of auto parts uses high-pressure pumps to deburr machined parts as a part of its production and quality check process. They decided to monitor these pumps to make sure they work properly and that they can see any indications leading to a potential failure before it affects their process.