Customer Company Size
Large Corporate
Region
- America
Country
- Mexico
Product
- COMSOL Multiphysics®
- Intel® Xeon® X5670 CPU
- MATLAB®
Tech Stack
- Electromagnetic Simulation
- Space Mapping Algorithms
- Multiphysics Simulation
Implementation Scale
- Enterprise-wide Deployment
Impact Metrics
- Productivity Improvements
- Innovation Output
- Digital Expertise
Technology Category
- Analytics & Modeling - Predictive Analytics
- Application Infrastructure & Middleware - Data Exchange & Integration
- Application Infrastructure & Middleware - Data Visualization
Applicable Industries
- Electronics
- Semiconductors
Applicable Functions
- Product Research & Development
- Quality Assurance
Use Cases
- Predictive Quality Analytics
- Manufacturing Process Simulation
- Digital Twin
Services
- Software Design & Engineering Services
- System Integration
About The Customer
Intel, a leader in the electronics and computer hardware industry, is renowned for its powerful computing clusters and servers used to efficiently simulate and optimize designs. The Intel Guadalajara Design Center, in particular, has developed innovative optimization methods combining space mapping algorithms and electromagnetic simulation to improve signal speed and integrity in package interconnects. This approach is crucial for the development of high-speed interconnects in printed circuit boards (PCBs), which are integral to almost every electronic device, from handheld computers and cellphones to state-of-the-art satellite communication systems. The center's researchers and engineers leverage multiphysics simulation software and unconventional design optimization techniques to address the challenges of making electronic devices smaller and more efficient. Their work ensures that the latest high-speed interconnect technology is available in less time, maintaining Intel's position at the forefront of technological innovation.
The Challenge
In the electronics and computer hardware industry, optimizing the design of high-speed interconnects in printed circuit boards (PCBs) is a significant challenge. As electronic devices become smaller, the size and spacing of package interconnects must be scaled down, making computational design optimization more time-consuming. Higher frequency interconnects consume more power, and the geometry and materials of these interconnects need to be redesigned to minimize power consumption and prevent signal loss. This is particularly crucial for PCBs, which are used in a wide range of electronic devices. Full-wave electromagnetic simulation is necessary to model signal propagation in these interconnects, but solving the complete set of Maxwell’s equations without simplifying assumptions is computationally intensive. This complexity is compounded by the need to account for non-negligible electromagnetic couplings and impedance mismatch in complex 3D structures, which can cause crosstalk and reflection, compromising signal integrity.
The Solution
To address the challenges of optimizing high-speed package interconnects, Intel engineers at the Guadalajara Design Center utilized COMSOL Multiphysics® software to develop a model of a single-ended interconnect line embedded in a PCB structure. This model allowed them to perform full-wave electromagnetic simulations, which are essential for accurately modeling signal propagation in interconnects operating at higher frequencies. The simulations accounted for non-negligible electromagnetic couplings and impedance mismatch in complex 3D structures, which are critical factors in maintaining signal integrity. To further enhance the optimization process, the engineers implemented a Broyden-based input space mapping optimization algorithm. This approach involved solving two separate interconnect models in COMSOL: a coarse 2D model and a fine 3D model. The coarse model provided a fast result by neglecting electromagnetic losses and using a very coarse mesh, while the fine model offered greater accuracy with a much finer mesh. The space mapping algorithm, implemented in MATLAB® software, aimed to find the 3D model design parameters that closely matched the optimal 2D model response. This method significantly reduced the overall computation time, allowing the interconnect design parameters to be optimized within just four iterations. The results showed a substantial reduction in reflected signal for the optimized design compared to the original fabricated interconnect prototype.
Operational Impact
Quantitative Benefit
Case Study missing?
Start adding your own!
Register with your work email and create a new case study profile for your business.
Related Case Studies.

Case Study
Remote Temperature Monitoring of Perishable Goods Saves Money
RMONI was facing temperature monitoring challenges in a cold chain business. A cold chain must be established and maintained to ensure goods have been properly refrigerated during every step of the process, making temperature monitoring a critical business function. Manual registration practice can be very costly, labor intensive and prone to mistakes.
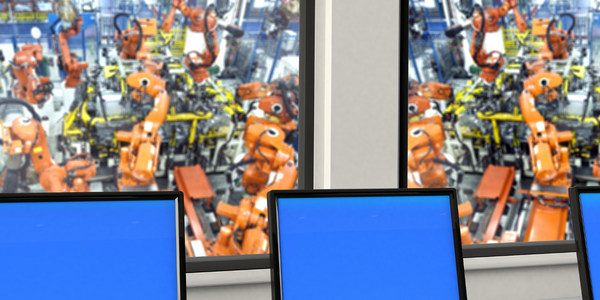
Case Study
KINESYS Semiconductor Factory Automation Software
KINESYS Software provides both Integrated Device Manufacturer (IDM) and Original Equipment Manufacturer (OEM) customers world-class software products and solutions for advanced wafer and device traceability and process management. KINESYS offers state of the art database technology with a core focus on SEMI standards. KINESYS’ challenge was to make back-end processing failure-free and easy to use for clients while supporting licensing models more adaptable to changing industry needs.
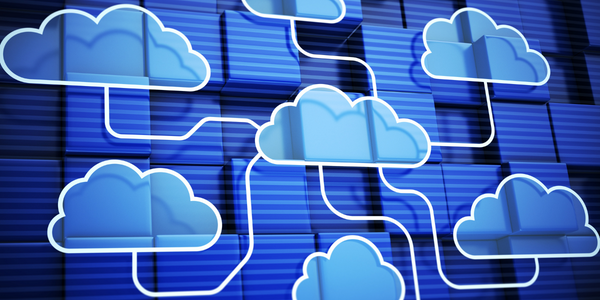
Case Study
Cloud Solution for Energy Management Platform-Schneider Electric
Schneider Electric required a cloud solution for its energy management platform to manage high computational operations, which were essential for catering to client requirements. As the business involves storage and analysis of huge amounts of data, the company also needed a convenient and scalable storage solution to facilitate operations efficiently.
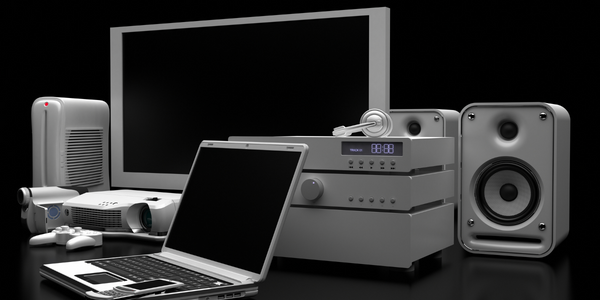
Case Study
Leveraging the IoT to Gain a Competitive Edge in International Competition
Many large manufacturers in and outside Japan are competing for larger market share in the same space, expecting a growing demand for projectors in the areas of entertainment, which requires glamor and strong visual performance as well as digital signage that can attract people’s attention. “It is becoming more and more difficult to differentiate ourselves with stand-alone hardware products,” says Kazuyuki Kitagawa, Director of Service & Support at Panasonic AVC Networks. “In order for Panasonic to grow market share and overall business, it is essential for us to develop solutions that deliver significant added value.” Panasonic believes projection failure and quality deterioration should never happen. This is what and has driven them to make their projectors IoT-enabled. More specifically, Panasonic has developed a system that collects data from projectors, visualizes detailed operational statuses, and predicts issues and address them before failure occurs. Their projectors are embedded with a variety of sensors that measure power supply, voltage, video input/ output signals, intake/exhaust air temperatures, cooling fan operations, and light bulb operating time. These sensors have been used to make the projector more intelligent, automatically suspending operation when the temperature rises excessively, and automatically switching light bulbs. Although this was a great first step, Panasonic projectors were still not equipped with any capability to send the data over a network.