Company Size
1,000+
Region
- America
Country
- United States
Product
- Fulcrum’s inspection app builder
- Fulcrum’s platform
Tech Stack
- Digital inspection apps
- QR code technology
Implementation Scale
- Enterprise-wide Deployment
Impact Metrics
- Customer Satisfaction
- Employee Satisfaction
- Productivity Improvements
Technology Category
- Application Infrastructure & Middleware - Data Exchange & Integration
Applicable Industries
- Equipment & Machinery
Applicable Functions
- Quality Assurance
Use Cases
- Process Control & Optimization
- Root Cause Analysis & Diagnosis
Services
- Software Design & Engineering Services
- System Integration
About The Customer
Halton Company is part of a family-owned, global technology organization that delivers complex indoor air solutions. The company's corporate vision and strategy focus on a premium customer experience, innovative digital capabilities, and high employee commitment. Delivering a quality product is at the heart of its business. In 2019, the company was tasked with digitizing its quality checklist process on the floor. At that point, they were using paper quality control forms that were filled out as products traveled through the manufacturing process. These were then manually scanned and filed away into a directory on a server. The data was not in an easily usable format so was not really supporting any other quality initiatives.
The Challenge
Halton Company, a global technology organization delivering complex indoor air solutions, was facing several challenges with its quality control inspections. The company was using paper-based quality control forms that were filled out as products traveled through the manufacturing process. These forms were then manually scanned and filed away into a directory on a server. The data was not in an easily usable format and was not supporting any other quality initiatives. The paper checklists promoted cursory examinations, often resulting in incomplete quality control audit documentation. The company was unable to share quality control inspection data to promote constant improvement and had ineffective and delayed identification of quality issues.
The Solution
In 2021, Halton Company completed its evaluation and chose Fulcrum to digitize its quality control checklist process. Fulcrum’s inspection app builder allowed Halton Company to collapse its paper forms for a three-phase quality control inspection process into a single all-encompassing digital checklist app for each product. Fulcrum’s platform filtering logic guides inspectors through the quality control procedure based on their inputs at each inspection point. The company also utilized Fulcrum's QR code access reporting, which allowed employees and other stakeholders to report quality issues even if they do not have a Fulcrum user license. By scanning a QR code, an online form can be accessed and completed right on their mobile device, including adding pictures. Upon submission, the reported issue is visible and actionable right on the Fulcrum platform.
Operational Impact
Quantitative Benefit
Case Study missing?
Start adding your own!
Register with your work email and create a new case study profile for your business.
Related Case Studies.

Case Study
Smart Water Filtration Systems
Before working with Ayla Networks, Ozner was already using cloud connectivity to identify and solve water-filtration system malfunctions as well as to monitor filter cartridges for replacements.But, in June 2015, Ozner executives talked with Ayla about how the company might further improve its water systems with IoT technology. They liked what they heard from Ayla, but the executives needed to be sure that Ayla’s Agile IoT Platform provided the security and reliability Ozner required.

Case Study
IoT enabled Fleet Management with MindSphere
In view of growing competition, Gämmerler had a strong need to remain competitive via process optimization, reliability and gentle handling of printed products, even at highest press speeds. In addition, a digitalization initiative also included developing a key differentiation via data-driven services offers.
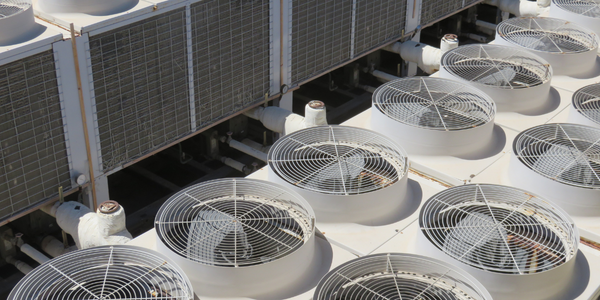
Case Study
Predictive Maintenance for Industrial Chillers
For global leaders in the industrial chiller manufacturing, reliability of the entire production process is of the utmost importance. Chillers are refrigeration systems that produce ice water to provide cooling for a process or industrial application. One of those leaders sought a way to respond to asset performance issues, even before they occur. The intelligence to guarantee maximum reliability of cooling devices is embedded (pre-alarming). A pre-alarming phase means that the cooling device still works, but symptoms may appear, telling manufacturers that a failure is likely to occur in the near future. Chillers who are not internet connected at that moment, provide little insight in this pre-alarming phase.

Case Study
Premium Appliance Producer Innovates with Internet of Everything
Sub-Zero faced the largest product launch in the company’s history:It wanted to launch 60 new products as scheduled while simultaneously opening a new “greenfield” production facility, yet still adhering to stringent quality requirements and manage issues from new supply-chain partners. A the same time, it wanted to increase staff productivity time and collaboration while reducing travel and costs.

Case Study
Integration of PLC with IoT for Bosch Rexroth
The application arises from the need to monitor and anticipate the problems of one or more machines managed by a PLC. These problems, often resulting from the accumulation over time of small discrepancies, require, when they occur, ex post technical operations maintenance.
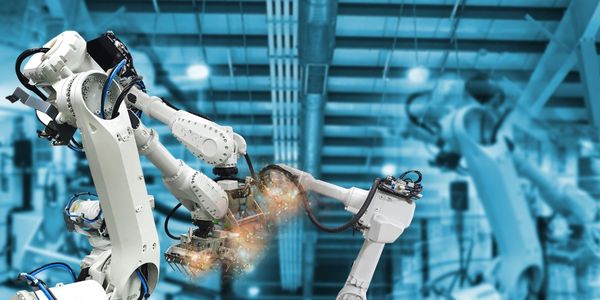
Case Study
Robot Saves Money and Time for US Custom Molding Company
Injection Technology (Itech) is a custom molder for a variety of clients that require precision plastic parts for such products as electric meter covers, dental appliance cases and spools. With 95 employees operating 23 molding machines in a 30,000 square foot plant, Itech wanted to reduce man hours and increase efficiency.