CinePostproduction: Speeding delivery of digital cinema packages for theatre release using hybrid cloud model
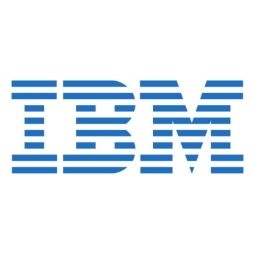
Customer Company Size
Mid-size Company
Region
- Europe
Country
- Germany
- Austria
- Switzerland
Product
- IBM Aspera On Demand
- SHARC system
Tech Stack
- Cloud Computing
- Data Transfer Protocol
Implementation Scale
- Enterprise-wide Deployment
Impact Metrics
- Productivity Improvements
- Cost Savings
Technology Category
- Infrastructure as a Service (IaaS) - Cloud Computing
- Infrastructure as a Service (IaaS) - Hybrid Cloud
Applicable Functions
- Logistics & Transportation
Use Cases
- Track & Trace of Assets
Services
- Cloud Planning, Design & Implementation Services
About The Customer
CinePostproduction is one of Germany’s leading post-production facilities and has been operating in the digital cinema market for several years. The company offers a range of services including post-production of feature films and TV-productions, duplication of DCP copies, DCP-versioning and -mastering, localization of trailers and KDM-services. CinePostproduction has been developing software solutions for over four years, including the DCP portal SHARC. This solution is used by a majority of cinemas in the D-A-CH region to download DCP cinema trailers and also offers distributors a comfortable and flexible way for DCP key-creation and -management. The company was founded in 1911 and has been a pioneer in the transition from 35-millimeter film to digital cinema.
The Challenge
CinePostproduction, a leading postproduction facility in Germany, was faced with the challenge of speeding up the ingest of media files and the delivery of large Digital Cinema Packages (DCPs) to cinemas throughout the DACH region. The transition from 35-millimeter film to digital cinema posed a significant challenge for the company. Despite the shift to digital, the most common method for distributing DCPs remained the physical shipment of specialized hard disks via courier or satellite delivery. This method was not only slow and unreliable, but also costly. The challenge was further complicated by the large volume and size of the media files: DCPs typically range from 100GB to as large as 400GB. For its TV and cinema postproduction business area, CinePostproduction needed to send data sets between 150GB to 1.5TB per feature film, which occasionally needed to be transferred globally.
The Solution
CinePostproduction integrated IBM® Aspera® on Demand into their new SHARC system to speed the ingest of DCPs from studios and the delivery of DCPs directly to cinemas. The SHARC system, which fully integrates Aspera on Demand running in the cloud, allows CinePostproduction to transfer encrypted, high-resolution Digital Cinema Packages (DCP) with up to 2K or 4K resolutions between the CinePostproduction Content Delivery Network servers in their data center and the participating cinemas in the DACH region. The distribution platform is extremely cost effective because theaters can utilize their existing infrastructure to achieve maximum speed delivery. They simply install the CinePostproduction download client software, which contains an embedded Aspera client, and receive DCPs directly from SHARC to the theater over their existing broadband connection. Running Aspera On Demand in the cloud allows CinePostproduction to scale up transfer capacity as needed to help meet the variable demand and provide on-time delivery to the cinemas.
Operational Impact
Quantitative Benefit
Case Study missing?
Start adding your own!
Register with your work email and create a new case study profile for your business.
Related Case Studies.
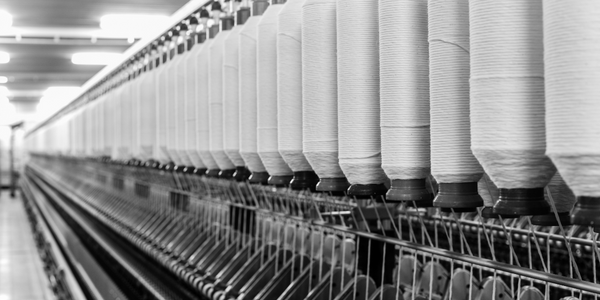
Case Study
IoT Applications and Upgrades in Textile Plant
At any given time, the textile company’s manufacturing facility has up to 2,000 textile carts in use. These carts are pushed from room to room, carrying materials or semi-finished products. Previously, a paper with a hand-written description was attached to each cart. This traditional method of processing made product tracking extremely difficult. Additionally, making sure that every cart of materials or semi-finished products went to its correct processing work station was also a problem. Therefore, the company desired an intelligent solution for tracking assets at their factories. They also wanted a solution that would help them collect process data so they could improve their manufacturing efficiency.
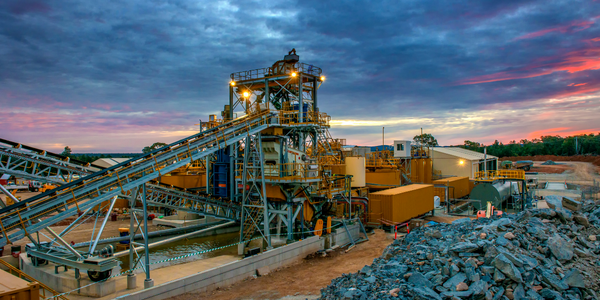
Case Study
Goldcorp: Internet of Things Enables the Mine of the Future
Goldcorp is committed to responsible mining practices and maintaining maximum safety for its workers. At the same time, the firm is constantly exploring ways to improve the efficiency of its operations, extend the life of its assets, and control costs. Goldcorp needed technology that can maximize production efficiency by tracking all mining operations, keep employees safe with remote operations and monitoring of hazardous work areas and control production costs through better asset and site management.
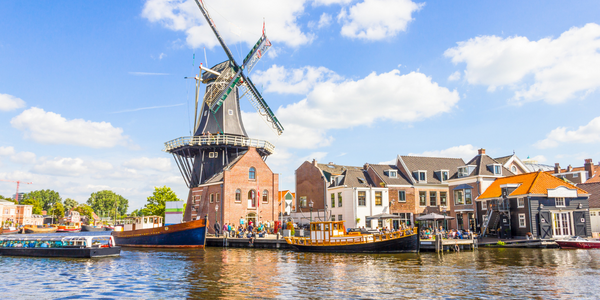
Case Study
Buoy Status Monitoring with LoRa
The Netherlands are well-known for their inland waterways, canals, sluices and of course port activities. The Dutch Ministry of Infrastructure indicates that there are thousands of buoys and fixed items in and near water environments that would profit from IoT monitoring. One of the problems with buoys for example, is that they get hit by ships and the anchor cable breaks. Without connectivity, it takes quite some time to find out that something has happened with that buoy. Not to mention the costs of renting a boat to go to the buoy to fix it. Another important issue, is that there is no real-time monitoring of the buoys at this moment. Only by physically visiting the object on the water, one gains insight in its status.

Case Study
IoT Based Asset Tracking System
The existing system used by the customer could only track a few thousand assets and was able to generate only a few standard set of reports. As the number of assets tracked grew exponentially, the system started to break at the seams. The Tracking devices were from different manufacturers following different protocols. There was no proper integration among the devices to send instant alerts. There are thousands of tracking devices spread across multiple geographies, that are moving. The configuration and troubleshooting of these devices incurred heavy costs, which was a logistics challenge. The existing system did not provide sophisticated Analytics, Business Intelligence and Insights from the data
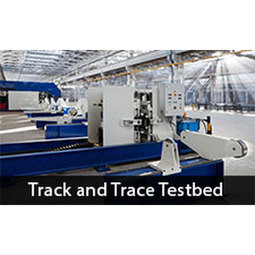
Case Study
IIC - Track and Trace Testbed
Factory systems can detect - within a meter - the location of a tool; Misuse of tools can result in serious accident or injury; The production of many industrial and consumer goods requires exacting work - down to the precise force used to tighten a screw. GOAL Manage smart, hand-held tools in manufacturing, maintenance, and industrial environments