Customer Company Size
Large Corporate
Region
- America
Country
- United States
Product
- IBM® Aspera® Connect Server
- IBM® Aspera® Desktop Client
- IBM® Aspera® Sync
- IBM® Aspera® Point-to-Point Client
- IBM® Aspera® Connect Browser Plug-in
Tech Stack
- FASP® technology
Implementation Scale
- Enterprise-wide Deployment
Impact Metrics
- Productivity Improvements
- Cost Savings
Technology Category
- Application Infrastructure & Middleware - Data Exchange & Integration
Applicable Functions
- Discrete Manufacturing
Use Cases
- Digital Thread
- Supply Chain Visibility
Services
- System Integration
- Software Design & Engineering Services
About The Customer
Cinedigm is a full service digital entertainment distribution company and the largest worldwide aggregator of independent digital content. Cinedigm delivers award-winning content for a variety of distribution platforms, including digital, cable video on-demand, Blu-ray, DVD, and theatrical release, and reaches a global audience through its partnerships with Netflix, iTunes, Hulu, Amazon, and many others. Cinedigm relies on Aspera’s patented FASP® technology for digital content deliveries to all of its partner distribution platforms, as well as to pull in content from independent film producers and studios.
The Challenge
As Cinedigm’s business continues to grow, the company is faced with the dilemma of how to retrieve more content from production companies and disseminate more content, and faster, to their distribution partners located across the country and even internationally. Presented with full-length HD films, often uncompressed or in ProRes or other high-res versions, Cinedigm needed a transfer solution that could accommodate very large file sizes while maintaining speed, efficiency and security. Along with receiving content from producers and delivering to distribution partners, Cinedigm also needed a faster transfer mechanism for their internal business needs. Files needed to be quickly delivered to storage facilities located in Dallas and Chicago as well as content sent from New York to their sister office in Los Angeles for sharing and collaboration. Shipping media content on hard drives back and forth across the country and internationally was too costly and time-consuming, while FTP presented challenges with speed, bandwidth consumption and reliability. Cinedigm sought a faster, more dependable solution to shorten the end-to-end delivery workflow.
The Solution
After evaluating their options, Cinedigm selected a software suite from Aspera to fulfill their transfer requirements, citing Aspera’s prevalence within the media and entertainment industry as well as the technology’s ability to scale alongside the growth of the business as key influencers in their decision. Because Aspera is used or affiliated with the back-end delivery system of nearly every company that Cinedigm works with, adopting Aspera opened the door to an existing ecosystem of Aspera-based workflows, making transfers between partners and clients easier than ever. Cinedigm adopted the Aspera Connect Server to enable content partners to deliver files directly to Cinedigm. Once content is received, it goes through a series of steps including processing, transcoding and ingest, and subsequently Cinedigm uploads the files to “workflow watch folders” where the Aspera Connect Server picks them up for high-speed delivery to distribution channels. Partner distributors such as Netflix and Hulu can use their own Aspera clients or the auto-installed IBM® Aspera® Connect Browser Plug-in available at no charge to download content. Internally, Cinedigm selected Aspera Point-to-Point to transfer feature-length films directly to their Tier 3 mirror SAN storage facilities and to their sister office, enabling collaboration between cross-country team members.
Operational Impact
Quantitative Benefit
Case Study missing?
Start adding your own!
Register with your work email and create a new case study profile for your business.
Related Case Studies.

Case Study
Remote Temperature Monitoring of Perishable Goods Saves Money
RMONI was facing temperature monitoring challenges in a cold chain business. A cold chain must be established and maintained to ensure goods have been properly refrigerated during every step of the process, making temperature monitoring a critical business function. Manual registration practice can be very costly, labor intensive and prone to mistakes.
-Testbed.png)
Case Study
IIC Industrial Digital Thread (IDT) Testbed
Field engineers and service teams often lack data and digital insights needed to assess, troubleshoot, and determine work scope for the large industrial assets in performing corrective and preventative maintenance activities. QA engineers many times need to understand why a particular problem in the part is happening recurrently or why parts from suppliers don’t stack up well in the assemblies due to mismatch. The root cause is usually hidden in design, manufacturing processes, supply chain logistics or production planning. But without the right data and digital insights, it's hard to pinpoint. GOAL To collect information in the design, manufacturing, service, supply-chain setup and provide access to and intelligent analytics for industrial manufacturing and performance data, to identify the root cause easier. Such insights can improve not only service and owner/operator productivity, but also provide critical feedback to the design engineering and manufacturing operations teams for continuous improvement.
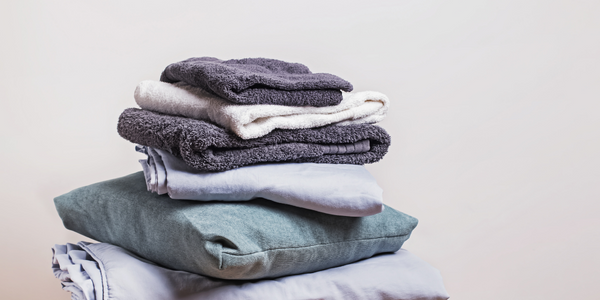
Case Study
Retail Uses RFID to Enable Cold Chain Monitoring
Like most grocery retailers, Hy-Vee is faced with the challenge of providing the highest quality products to its shoppers. Shoppers want the longest possible shelf life from perishable products and expect a consistent product experience each time they shop. Controlling the quality of products sold leads to shopper loyalty, which is of paramount importance to the success of Hy-Vee. Before products arrive in stores, Hy-Vee's distribution centers (DCs) handle items including dairy products, fresh meats, seafood, deli items, produce and frozen goods, all of which have different temperature needs and sensitivities. During transit from suppliers to DCs, Hy-Vee has limited visibility and temperature management abilities due to large amount of supplier managed transportation. For instance, during a week-long transit, a supplier's carrier equipment may malfunction, causing an item to thaw and then refreeze once repairs are made. Hy-Vee sought help from TempTRIP, an RFID solution provider that focuses on shipping, storage, receiving, and temperature control. TempTRIP's EPC RFID tags use Impinj chips to monitor and report temperature readings throughout the shipping and receiving process. The tags can also be re-configured and re-used, a unique feature within the current market of temperature monitoring devices.
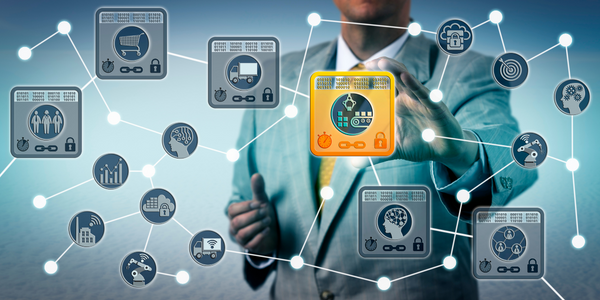
Case Study
Covisint Improves Mitsubishi's Collaboration With Its Supply Chain
Mitsubishi sought to improve supplier relationships on a global basis and to offer an easy-to-use solution to interact with them. In August 2004, Mitsubishi selected Covisint’s platform to help improve sharing of information and collaborative business processes with its global suppliers. Covisint enabled Mitsubishi to provide its suppliers with immediate access to information and applications to obtain more collaborative working relationships