Case Study – Lawler Foods Ltd.
Customer Company Size
Mid-size Company
Region
- America
Country
- United States
Product
- ProcessPro’s ERP solution
- Warehouse Management Solution (WMS)
- Dock Scheduling
- Research and Development (R&D)
Tech Stack
- ERP software
Implementation Scale
- Enterprise-wide Deployment
Impact Metrics
- Productivity Improvements
- Cost Savings
Technology Category
- Functional Applications - Enterprise Resource Planning Systems (ERP)
- Functional Applications - Warehouse Management Systems (WMS)
Applicable Industries
- Food & Beverage
Applicable Functions
- Discrete Manufacturing
- Warehouse & Inventory Management
Use Cases
- Inventory Management
- Warehouse Automation
Services
- System Integration
About The Customer
Lawler Foods Ltd. is a family-owned and operated manufacturer of gourmet cheesecakes, cakes, and pies that are served in restaurants, hotels, and other fine foodservice establishments around the world. The company was previously utilizing an ERP software system they struggled with for almost a decade. The system was not a proper fit for their business operations, leading to manual scheduling for three plants, which cost them nearly two days worth of labor. The scanning aspect of their previous software was a third party add-on that they didn’t receive any support when issues arose. Accounting was also operated via a third party add-on and didn’t function as “true” accounting software, therefore decreasing productivity with the accounting staff and leaving them again stranded without product support to navigate any issues.
The Challenge
Lawler Foods Ltd., a family-owned and operated manufacturer of gourmet cheesecakes, cakes, and pies, was previously utilizing an ERP software system they struggled with for almost a decade. The first of three main issues was the inability to use the Material Requirements Planning (MRP) functionality within the system; an improper fit left their business with individually scheduling for three plants manually which cost them nearly two days worth of labor. Secondly, the scanning aspect of their previous software was a third party add-on that they didn’t receive any support when issues arose. Finally, accounting was also operated via a third party add-on and didn’t function as “true” accounting software, therefore decreasing productivity with the accounting staff and leaving them again stranded without product support to navigate any issues.
The Solution
While evaluating their previous ERP system, Lawler decided to implement ProcessPro’s ERP solution, a fully integrated and industry-specific ERP software that strongly matched their company’s business operations and objectives. The software add-on applications included Warehouse Management Solution (WMS), Dock Scheduling, and Research and Development (R&D). Lawler implemented ProcessPro in October 2011. Their previous experience implementing other ERP systems were difficult; they had numerous contacts for each component of the software which often halted progress and was an ongoing frustration. Implementing with ProcessPro went really smooth and had the flexibility to go at the pace that was most comfortable for them.
Operational Impact
Quantitative Benefit
Case Study missing?
Start adding your own!
Register with your work email and create a new case study profile for your business.
Related Case Studies.

Case Study
The Kellogg Company
Kellogg keeps a close eye on its trade spend, analyzing large volumes of data and running complex simulations to predict which promotional activities will be the most effective. Kellogg needed to decrease the trade spend but its traditional relational database on premises could not keep up with the pace of demand.

Case Study
HEINEKEN Uses the Cloud to Reach 10.5 Million Consumers
For 2012 campaign, the Bond promotion, it planned to launch the campaign at the same time everywhere on the planet. That created unprecedented challenges for HEINEKEN—nowhere more so than in its technology operation. The primary digital content for the campaign was a 100-megabyte movie that had to play flawlessly for millions of viewers worldwide. After all, Bond never fails. No one was going to tolerate a technology failure that might bruise his brand.Previously, HEINEKEN had supported digital media at its outsourced datacenter. But that datacenter lacked the computing resources HEINEKEN needed, and building them—especially to support peak traffic that would total millions of simultaneous hits—would have been both time-consuming and expensive. Nor would it have provided the geographic reach that HEINEKEN needed to minimize latency worldwide.

Case Study
Energy Management System at Sugar Industry
The company wanted to use the information from the system to claim under the renewable energy certificate scheme. The benefit to the company under the renewable energy certificates is Rs 75 million a year. To enable the above, an end-to-end solution for load monitoring, consumption monitoring, online data monitoring, automatic meter data acquisition which can be exported to SAP and other applications is required.

Case Study
Coca Cola Swaziland Conco Case Study
Coco Cola Swaziland, South Africa would like to find a solution that would enable the following results: - Reduce energy consumption by 20% in one year. - Formulate a series of strategic initiatives that would enlist the commitment of corporate management and create employee awareness while helping meet departmental targets and investing in tools that assist with energy management. - Formulate a series of tactical initiatives that would optimize energy usage on the shop floor. These would include charging forklifts and running cold rooms only during off-peak periods, running the dust extractors only during working hours and basing lights and air-conditioning on someone’s presence. - Increase visibility into the factory and other processes. - Enable limited, non-intrusive control functions for certain processes.

Case Study
Temperature Monitoring for Restaurant Food Storage
When it came to implementing a solution, Mr. Nesbitt had an idea of what functionality that he wanted. Although not mandated by Health Canada, Mr. Nesbitt wanted to ensure quality control issues met the highest possible standards as part of his commitment to top-of-class food services. This wish list included an easy-to use temperature-monitoring system that could provide a visible display of the temperatures of all of his refrigerators and freezers, including historical information so that he could review the performance of his equipment. It also had to provide alert notification (but email alerts and SMS text message alerts) to alert key staff in the event that a cooling system was exceeding pre-set warning limits.
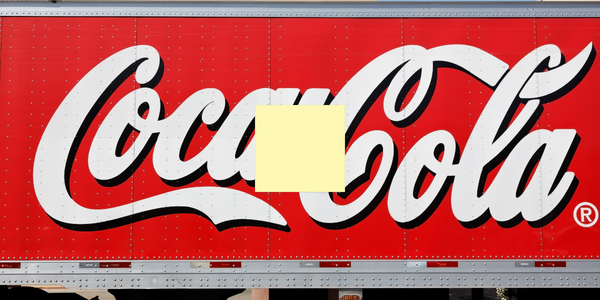
Case Study
Coca-Cola Refreshments, U.S.
Coca-Cola Refreshments owns and manages Coca-Cola branded refrigerators in retail establishments. Legacy systems were used to locate equipment information by logging onto multiple servers which took up to 8 hours to update information on 30-40 units. The company had no overall visibility into equipment status or maintenance history.