Customer Company Size
Large Corporate
Region
- Asia
Country
- China
Product
- Aegis Manufacturing Execution System (MES) software
Tech Stack
- Computer Aided Design (CAD)
- Bill of Materials (BOM) data
Implementation Scale
- Enterprise-wide Deployment
Impact Metrics
- Productivity Improvements
- Cost Savings
- Customer Satisfaction
Technology Category
- Functional Applications - Manufacturing Execution Systems (MES)
Applicable Industries
- Automotive
Applicable Functions
- Discrete Manufacturing
- Quality Assurance
Use Cases
- Manufacturing System Automation
- Predictive Maintenance
Services
- System Integration
- Software Design & Engineering Services
About The Customer
Lear Automotive Electronics and Electrical Products in Shanghai, China, is a subsidiary of the global Lear Corporation. Established in 2008, the company is one of the world’s leading suppliers of automotive seating and electrical distribution systems. Their main products include central control boxes, tire pressure monitoring systems, remote keyless entry units, and door sensor systems. The company's customers span some of the top automotive manufacturers in the world, including BMW, General Motors, Volkswagen, Geely, and Ford. As a new facility in 2008, it was crucial for Lear Shanghai to quickly establish a fully functioning operation that could meet their customers’ expectations for product quality, on-time delivery, and traceability.
The Challenge
Lear Shanghai, a subsidiary of the global Lear Corporation, was looking to eliminate rework and shorten new product introduction (NPI) time to improve their overall manufacturing process. As a supplier of automotive electrical distribution systems, their customers’ expectations for product quality and traceability were a key priority. The manufacturing process is quite complex, and the company’s main products include central control boxes, tire pressure monitoring systems, remote keyless entry units, and door sensor systems. Decision makers at the management level must balance their customers’ needs for product quality, on-time delivery, and traceability while minimizing their own production costs and increasing throughput. In 2008, as a new facility, it was crucial that decision makers choose an MES software that could be quickly and easily deployed throughout the facility to minimize the time it took to run as a fully functioning operation.
The Solution
Lear Shanghai deployed Aegis Manufacturing Execution System (MES) software to improve their manufacturing process. The software's 95% out-of-the-box configurability required only a small amount of integration to achieve its full potential in operations at Lear. This simplified deployment compared to the other options considered, and it allowed for Lear to achieve a fully functional Shanghai operation in just one month. The software's unique ability to import, clean, and merge BOM data with the product CAD design data enabled engineers to compare product versions instantly. They could detect errors and changes that would require hours to do manually. This data was then used to rapidly create machine programs, build visual work instructions for operators automatically, and visually design an entire process flow/routing for production. The visuals designed by engineering were then digitally presented paperlessly in production at the right time, right place, and fully automatically.
Operational Impact
Quantitative Benefit
Case Study missing?
Start adding your own!
Register with your work email and create a new case study profile for your business.
Related Case Studies.
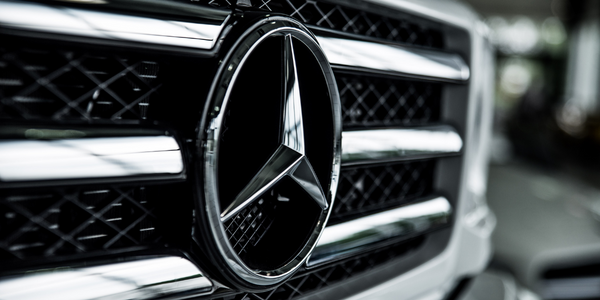
Case Study
Integral Plant Maintenance
Mercedes-Benz and his partner GAZ chose Siemens to be its maintenance partner at a new engine plant in Yaroslavl, Russia. The new plant offers a capacity to manufacture diesel engines for the Russian market, for locally produced Sprinter Classic. In addition to engines for the local market, the Yaroslavl plant will also produce spare parts. Mercedes-Benz Russia and his partner needed a service partner in order to ensure the operation of these lines in a maintenance partnership arrangement. The challenges included coordinating the entire maintenance management operation, in particular inspections, corrective and predictive maintenance activities, and the optimizing spare parts management. Siemens developed a customized maintenance solution that includes all electronic and mechanical maintenance activities (Integral Plant Maintenance).
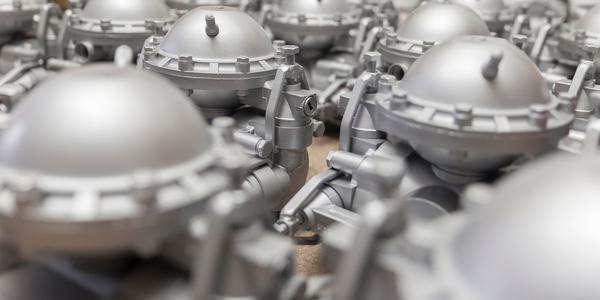
Case Study
Monitoring of Pressure Pumps in Automotive Industry
A large German/American producer of auto parts uses high-pressure pumps to deburr machined parts as a part of its production and quality check process. They decided to monitor these pumps to make sure they work properly and that they can see any indications leading to a potential failure before it affects their process.