Cabot Streamlines and Standardizes Scheduling, Greatly Improving Visibility
Company Size
1,000+
Region
- America
- Asia
- Europe
Country
- United States
- Worldwide
Product
- Aspen Plant Scheduler
- Aspen Supply Chain Connect
- AspenTech engineering
- AspenTech advanced process control
- AspenTech information management solutions
Tech Stack
- Microsoft Excel
- Microsoft Access
- ERP system
Implementation Scale
- Enterprise-wide Deployment
Impact Metrics
- Cost Savings
- Productivity Improvements
Technology Category
- Functional Applications - Enterprise Resource Planning Systems (ERP)
- Functional Applications - Inventory Management Systems
Applicable Industries
- Chemicals
Applicable Functions
- Discrete Manufacturing
- Procurement
Use Cases
- Inventory Management
- Predictive Maintenance
Services
- Cloud Planning, Design & Implementation Services
- System Integration
About The Customer
Cabot is a specialty chemicals manufacturer with 42 manufacturing facilities in 18 countries that revenues $2.5 billion. The company has expertise in making and handling fine particles, modifying the surfaces of very fine particles, and designing particle-media composites for specific properties. Cabot has been an AspenTech customer for 10 years, using AspenTech engineering, advanced process control, and information management solutions across all global sites. Cabot made the decision to expand their AspenTech relationship into the supply chain space with Aspen Plant Scheduler.
The Challenge
Cabot’s Carbon Black business was using their own Microsoft® Excel and Access-based tools for scheduling, which did not provide the visibility required to make timely business decisions. Planning was performed regionally, scheduling was performed offline through customized tools at each plant, and executing events was done manually in the ERP system. As a result, schedulers were forced to spend the majority of their time gathering the data needed to make decisions. Cabot sought to improve the information available to the schedulers and enrich communication along the supply chain.
The Solution
Cabot decided to standardize on Aspen Plant Scheduler at all global Carbon Black sites, which now provides visibility into their supply chain to bridge execution gaps, thereby improving schedule use and response time, and reducing working capital. The professional services team at AspenTech worked with Cabot to develop the standard scheduling model, as well as its implementation and deployment at the initial European plants. Cabot’s four-stage implementation methodology and “cookie cutter” approach to basic scheduling enabled a faster and smoother rollout for subsequent plants, using mostly internal resources.
Operational Impact
Quantitative Benefit
Case Study missing?
Start adding your own!
Register with your work email and create a new case study profile for your business.
Related Case Studies.
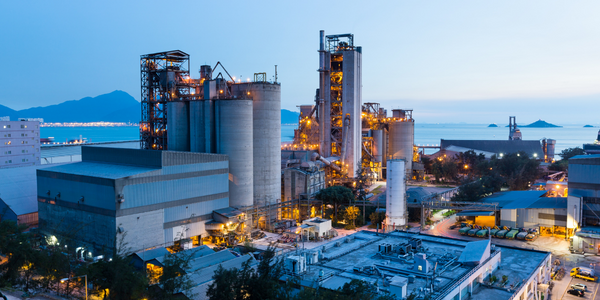
Case Study
Honeywell - Tata Chemicals Improves Data Accessibility with OneWireless
Tata was facing data accessibility challenges in the cement plant control room tapping signals from remote process control areas and other distant locations, including the gas scrubber. Tata needed a wireless solution to extend its control network securely to remote locations that would also provide seamless communication with existing control applications.

Case Study
Advanced Elastomer Systems Upgrades Production
In order to maintain its share of the international market for thermoplastic elastomers AES recently expanded its Florida plant by adding a new production line. While the existing lines were operating satisfactorily using a PROVOX distributed control system with traditional analog I/O, AES wanted advanced technology on the new line for greater economy, efficiency, and reliability. AES officials were anxious to get this line into production to meet incoming orders, but two hurricanes slowed construction.
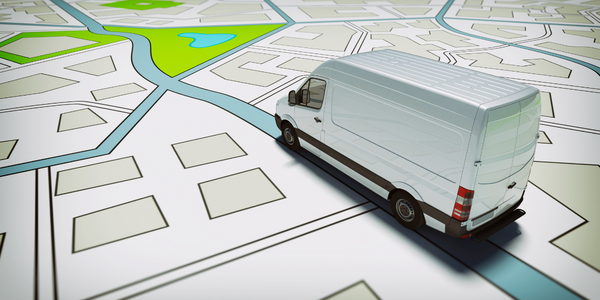
Case Study
Wireless GPS Tracking & Security Monitoring
Enhancing the security of hazardous freight and ensuring compliance with Homeland Security’s Transportation Security Administration mandate that all trains carrying chemicals capable of creating a toxic inhalation condition are equipped with on-board safety monitoring systems.
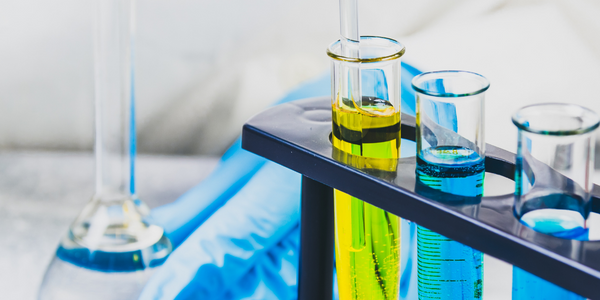
Case Study
Field Device Asset Management For Chemical Company in China
Chinese chemical subsidiary of multinational corporation serves customers throughout the world. Sales offices and research and technology centers are strategically located to provide rapid response to customer requests. Just two workers were assigned to maintain thousands of intelligent instruments in three production units, so they could do little more than react to device issues as they appeared. This costly maintenance method inevitably led to unexpected downtime when a critical instrument failed. Plant management recognized the need to change from reactive to predictive maintenance for all assets, including instruments and control valves, but help was needed in implementing such a technology-based initiative.
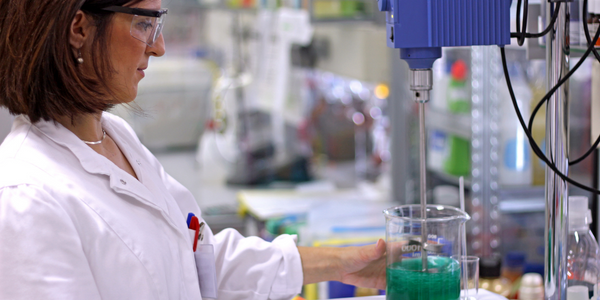
Case Study
Industrial Workforce Mobility for Improved Safety & Operations
Huntsman Corporation, a global manufacturer and marketer of differentiated chemicals, undertook an aggressive program to eliminate injuries, product defects, and environmental releases at their Port Neches facility. Termed “Project Zero”, this program required a completely mobile solution to empower operations and maintenance personnel to capture defects, track work progress and make process and safety related decisions in real-time.