Building a Foundation on Automation
Customer Company Size
SME
Region
- America
Country
- United States
Product
- Savanna.NET®
- Automated Storage and Retrieval Systems (AS/RS)
- Storage/Retrieval Machine (S/RM)
Tech Stack
- Warehouse Management System (WMS)
- Warehouse Control System (WCS)
- Biometric Human Machine Interface
Implementation Scale
- Enterprise-wide Deployment
Impact Metrics
- Cost Savings
- Customer Satisfaction
- Productivity Improvements
Technology Category
- Automation & Control - Automation & Process Control Systems
- Functional Applications - Warehouse Control Systems (WCS)
- Functional Applications - Warehouse Management Systems (WMS)
Applicable Functions
- Warehouse & Inventory Management
Use Cases
- Inventory Management
- Warehouse Automation
Services
- Software Design & Engineering Services
- System Integration
About The Customer
RoboVault is a premier ultra-secure, high-tech, automated private storage facility located in Fort Lauderdale, Florida. The facility caters to hundreds of clients, storing high-value luxury items such as exotic cars, fine jewelry, high-value works of art, and vintage wine. RoboVault represents the future of the self-storage industry, offering unparalleled levels of security, privacy, and service. The facility is designed to withstand extreme weather conditions, including category 5 hurricanes, and is equipped with state-of-the-art technology to ensure the safety and security of stored items.
The Challenge
When RoboVault was founded in 2008, the Fort Lauderdale area’s escalating land prices, hurricane-prone location, strict zoning requirements, and short supply of urban land presented limited building options. RoboVault saw that an automated, multi-story facility would be both cost-effective and help the newly formed company achieve the highest level of security. From the start, RoboVault sought a partner that would be an expert in warehouse automation that could not only help design and build the facility but also implement and support the right blend of technology to provide maximum security for high-value objects.
The Solution
RoboVault commissioned Westfalia Technologies, Inc., to develop a state-of-the-art automated storage facility. Westfalia, a leading provider of logistics solutions for plants, warehouses, and distribution centers, worked with RoboVault to design and build a 90,000 sq. foot facility that securely stores more than 450 containers in a museum-quality, climate-controlled, ultra-secure environment. The facility is constructed of solid concrete with reinforced steel, a solid concrete roof, and double-pane impact-resistant glass to withstand the 200 mph winds of a category 5 hurricane. At the heart of RoboVault is Westfalia’s Automated Storage and Retrieval Systems (AS/RS) technology, which features a robotic crane that safely and conveniently retrieves clients’ items. Clients drive up to the facility into a private entry cabin, access their individual module using a unique Personal Identification Number (PIN) on a keypad, and the Storage/Retrieval Machine (S/RM) retrieves the appropriate container/pallet. The final piece to RoboVault’s facility is Westfalia’s modular Savanna.NET® software, which controls, manages, and tracks all container movements and facility operations. The software interfaces with RoboVault’s security system and front-office operations, including customer information, credit card approval, keypads/biometric human machine interface screens, video monitoring, motion sensing, and heat detection to authenticate each client and ensure the security of their belongings.
Operational Impact
Quantitative Benefit
Case Study missing?
Start adding your own!
Register with your work email and create a new case study profile for your business.
Related Case Studies.
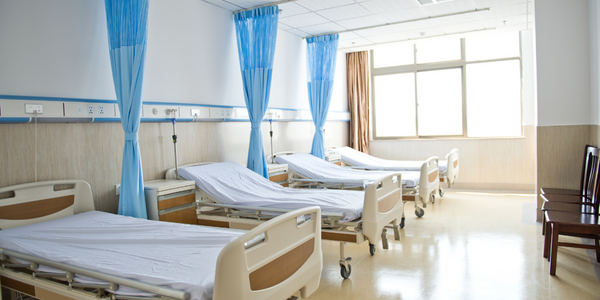
Case Study
Hospital Inventory Management
The hospital supply chain team is responsible for ensuring that the right medical supplies are readily available to clinicians when and where needed, and to do so in the most efficient manner possible. However, many of the systems and processes in use at the cancer center for supply chain management were not best suited to support these goals. Barcoding technology, a commonly used method for inventory management of medical supplies, is labor intensive, time consuming, does not provide real-time visibility into inventory levels and can be prone to error. Consequently, the lack of accurate and real-time visibility into inventory levels across multiple supply rooms in multiple hospital facilities creates additional inefficiency in the system causing over-ordering, hoarding, and wasted supplies. Other sources of waste and cost were also identified as candidates for improvement. Existing systems and processes did not provide adequate security for high-cost inventory within the hospital, which was another driver of cost. A lack of visibility into expiration dates for supplies resulted in supplies being wasted due to past expiry dates. Storage of supplies was also a key consideration given the location of the cancer center’s facilities in a dense urban setting, where space is always at a premium. In order to address the challenges outlined above, the hospital sought a solution that would provide real-time inventory information with high levels of accuracy, reduce the level of manual effort required and enable data driven decision making to ensure that the right supplies were readily available to clinicians in the right location at the right time.
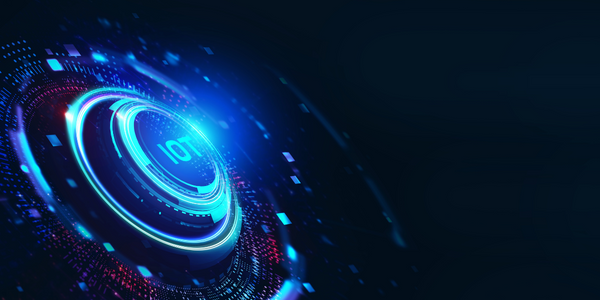
Case Study
IoT Solution for Cold Chain
Most of the customer's warehouses run on utility and generator power. Since these warehouses are in remote locations, power outages are a very common scenario. Diesel fuel, thereby, becomes a significant cost for these warehouses. Energy consumption was also very high due to the lack of a consistent temperature throughout the facility. This lack of a consistent temperature in all areas and no way to control it, resulted in the customer losing a significant amount of their temperature sensitive goods due to spoilage.
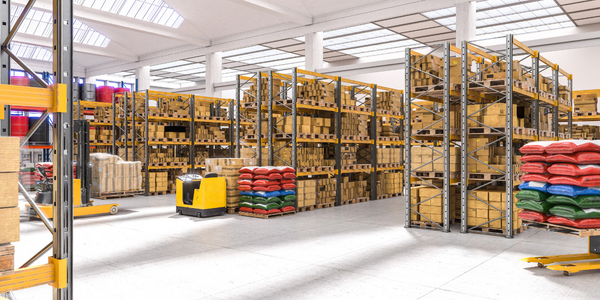
Case Study
Hardware Retailer Uses Data Warehouse to Track Inventory
Ace tracked which products retailers ordered, when they were ordered and shipped. However, the company could not track or forecast actual sales. Data used for reporting was up to a one-week old, owing to performance and data cleansing issues. Requirement to integrate wholesale and inventory data with POS data to help drive key business decisions, improve category management, lower inventory costs and optimize pricing. Reliance on custom coding to integrate POS data was excessively resource intensive and led to major performance constraints.
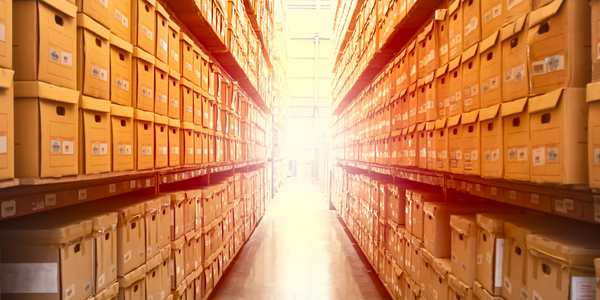
Case Study
DSV Road levels their workflow and decreases stress thanks to 4 BT Autopilots
During peaks in the workflow employeescan experience stress which makes them prone to causing damage. Avoiding these peaks also eliminates the need to hire temporary workers that require extra time and costs for education.