Brite-O-Matic leverages WinMan’s enterprise resource planning software to optimize its operations.
Company Size
11-200
Region
- America
Country
- United States
Product
- WinMan ERP
- Custom Mobile Applications by WinMan
Tech Stack
- Enterprise Resource Planning (ERP)
- Customer Relationship Management (CRM)
- Warehouse Management System (WMS)
- Manufacturing Resource Planning (MRP)
Implementation Scale
- Enterprise-wide Deployment
Impact Metrics
- Cost Savings
- Customer Satisfaction
- Productivity Improvements
Technology Category
- Functional Applications - Enterprise Resource Planning Systems (ERP)
- Functional Applications - Warehouse Management Systems (WMS)
Applicable Industries
- Automotive
- Professional Service
Applicable Functions
- Business Operation
- Warehouse & Inventory Management
Use Cases
- Inventory Management
- Remote Asset Management
Services
- Software Design & Engineering Services
- System Integration
About The Customer
Brite-O-Matic is a market-leading car wash consultancy that specializes in manufacturing, installing, and servicing car wash systems for new car dealerships. The company operates in ten states throughout the Midwest, providing high-quality machines designed to meet high demand. Brite-O-Matic's operations are extensive, involving multiple facets such as accounting, parts management, reporting, and customer relationship management (CRM). The company previously relied on four separate software systems to manage these functions, which were not integrated, leading to inefficiencies and a heavy reliance on manually produced Excel spreadsheets. Brite-O-Matic sought a more streamlined and integrated solution to better coordinate its operations and improve overall efficiency.
The Challenge
Brite-O-Matic is a market-leading car wash consultancy that manufactures, installs, and services car wash systems designed for use in new car dealerships. Operating in ten states throughout the Midwest, the company provides high-quality machines built to meet high demand. To run its operations, Brite-O-Matic previously relied on four software systems to handle its accounting, parts management, reporting, and customer relationship management (CRM). None of these systems integrated with the others, which caused employees to rely heavily on manually produced Excel spreadsheets. Brite-O-Matic needed a platform that could easily coordinate its entire operation, specifically “a single software solution that could help us keep track of our inventory,” said Steve. “It should let us order parts, tell us when to order parts, and inform us when to build a system within a designated time frame.” Steve interviewed four software providers that all said they could provide a solution, but “their prices were outrageous,” said Steve. His search continued, and then he found WinMan.
The Solution
WinMan is a powerful, all-in-one enterprise resource planning (ERP) system aimed at the manufacturing and distribution sectors. Designed to support optimal business processes, the system’s uniqueness is its flexibility and range of functionality within one system to help improve efficiency and productivity. It has a rich set of features, including production management, CRM, warehouse management, manufacturing resource planning, and supply chain management. Thanks to WinMan, Brite-O-Matic now has an integrated solution in which sales, purchasing, accounting, and service are all in the same system. Additionally, WinMan developed two custom mobile applications for Brite-O-Matic. These applications allow the off-site service techs to both view and enter required information while visiting customers throughout the day. One application helps the techs quickly fill their vans with the necessary repair or maintenance supplies required for their upcoming jobs. The other application allows each service tech to record time, material, and various readings gathered while servicing the car wash systems. When it comes to customer service, Steve said that WinMan did a top-notch job. “Whenever a change in the system needed to be made, WinMan took care of it right away. If it took some time to handle, WinMan gave us a target date and met it.”
Operational Impact
Case Study missing?
Start adding your own!
Register with your work email and create a new case study profile for your business.
Related Case Studies.
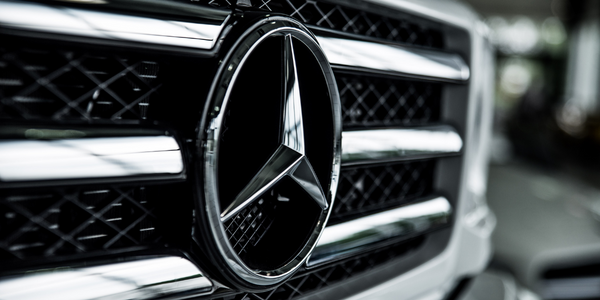
Case Study
Integral Plant Maintenance
Mercedes-Benz and his partner GAZ chose Siemens to be its maintenance partner at a new engine plant in Yaroslavl, Russia. The new plant offers a capacity to manufacture diesel engines for the Russian market, for locally produced Sprinter Classic. In addition to engines for the local market, the Yaroslavl plant will also produce spare parts. Mercedes-Benz Russia and his partner needed a service partner in order to ensure the operation of these lines in a maintenance partnership arrangement. The challenges included coordinating the entire maintenance management operation, in particular inspections, corrective and predictive maintenance activities, and the optimizing spare parts management. Siemens developed a customized maintenance solution that includes all electronic and mechanical maintenance activities (Integral Plant Maintenance).
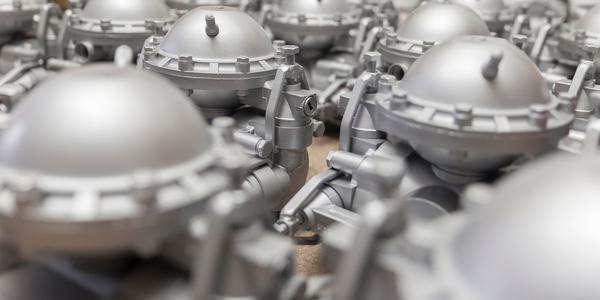
Case Study
Monitoring of Pressure Pumps in Automotive Industry
A large German/American producer of auto parts uses high-pressure pumps to deburr machined parts as a part of its production and quality check process. They decided to monitor these pumps to make sure they work properly and that they can see any indications leading to a potential failure before it affects their process.