Applicable Industries
- Automotive
- Equipment & Machinery
About The Customer
BOS Automotive is a leading supplier of interior components for the automotive industry. The company has a wide product range and a thriving armrest business. To meet the changing requirements of its expanded product range and to keep up with the increasing demands of its business, the company needed a solution that could enhance its production process. The company was looking for a solution that could not only increase the output but also improve the quality of the cut, thereby fulfilling the customer requirements.
The Challenge
BOS Automotive, a supplier of interior components, was facing a challenge in keeping up with the changing requirements of an expanded product range and a thriving armrest business. The company's existing fabric-cutting equipment was not able to meet the increasing demands and the need for precision in the production process. The challenge was to find a solution that could not only increase the output but also improve the quality of the cut, thereby fulfilling the customer requirements.
The Solution
BOS Automotive decided to replace its existing fabric-cutting equipment with a Lectra VectorAuto iX6. This high-capacity fabric-cutting solution offered a cutting speed that was 30% faster than the previous machine. This increase in speed resulted in a greater output, enabling the plant to eliminate a cutting line work shift. Additionally, the solution’s 2x7mm blade, which can cut up to 6cm of material, significantly reduced downtime. The high precision of the blade ensured the quality of the cut, thereby meeting the customer requirements.
Operational Impact
Quantitative Benefit
Case Study missing?
Start adding your own!
Register with your work email and create a new case study profile for your business.
Related Case Studies.

Case Study
Smart Water Filtration Systems
Before working with Ayla Networks, Ozner was already using cloud connectivity to identify and solve water-filtration system malfunctions as well as to monitor filter cartridges for replacements.But, in June 2015, Ozner executives talked with Ayla about how the company might further improve its water systems with IoT technology. They liked what they heard from Ayla, but the executives needed to be sure that Ayla’s Agile IoT Platform provided the security and reliability Ozner required.

Case Study
IoT enabled Fleet Management with MindSphere
In view of growing competition, Gämmerler had a strong need to remain competitive via process optimization, reliability and gentle handling of printed products, even at highest press speeds. In addition, a digitalization initiative also included developing a key differentiation via data-driven services offers.
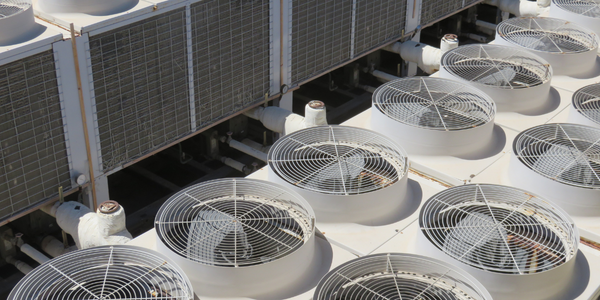
Case Study
Predictive Maintenance for Industrial Chillers
For global leaders in the industrial chiller manufacturing, reliability of the entire production process is of the utmost importance. Chillers are refrigeration systems that produce ice water to provide cooling for a process or industrial application. One of those leaders sought a way to respond to asset performance issues, even before they occur. The intelligence to guarantee maximum reliability of cooling devices is embedded (pre-alarming). A pre-alarming phase means that the cooling device still works, but symptoms may appear, telling manufacturers that a failure is likely to occur in the near future. Chillers who are not internet connected at that moment, provide little insight in this pre-alarming phase.

Case Study
Premium Appliance Producer Innovates with Internet of Everything
Sub-Zero faced the largest product launch in the company’s history:It wanted to launch 60 new products as scheduled while simultaneously opening a new “greenfield” production facility, yet still adhering to stringent quality requirements and manage issues from new supply-chain partners. A the same time, it wanted to increase staff productivity time and collaboration while reducing travel and costs.

Case Study
Integration of PLC with IoT for Bosch Rexroth
The application arises from the need to monitor and anticipate the problems of one or more machines managed by a PLC. These problems, often resulting from the accumulation over time of small discrepancies, require, when they occur, ex post technical operations maintenance.
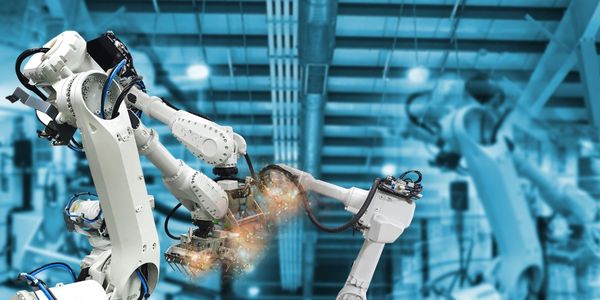
Case Study
Robot Saves Money and Time for US Custom Molding Company
Injection Technology (Itech) is a custom molder for a variety of clients that require precision plastic parts for such products as electric meter covers, dental appliance cases and spools. With 95 employees operating 23 molding machines in a 30,000 square foot plant, Itech wanted to reduce man hours and increase efficiency.