Big Data-Powered Tuning for Fast and Secure Processes
Customer Company Size
Large Corporate
Region
- Europe
- America
- Asia
Country
- Germany
- Mexico
- United States
- China
Product
- Celonis Process Mining
- SAP
Tech Stack
- Process Mining
- SQL Database
- ERP System
Implementation Scale
- Enterprise-wide Deployment
Impact Metrics
- Productivity Improvements
- Cost Savings
- Customer Satisfaction
- Digital Expertise
Technology Category
- Analytics & Modeling - Big Data Analytics
- Application Infrastructure & Middleware - Data Exchange & Integration
- Functional Applications - Manufacturing Execution Systems (MES)
Applicable Industries
- Automotive
Applicable Functions
- Procurement
- Quality Assurance
Use Cases
- Predictive Maintenance
- Process Control & Optimization
- Supply Chain Visibility
- Inventory Management
Services
- System Integration
- Data Science Services
- Software Design & Engineering Services
About The Customer
Eissmann Automotive is a globally active family business founded in 1964, headquartered in Bad Urach, Germany. The company is the world’s leading manufacturer of high-quality shifter modules, trim components, and complete car interiors. With more than 5,000 employees across 13 production sites in Hungary, the Czech Republic, Slovakia, the US, Mexico, and China, Eissmann Automotive collaborates with nearly all renowned manufacturers in the automotive industry. The company combines traditional craftsmanship with state-of-the-art production processes to deliver high-quality products. Eissmann Automotive has digitized its entire process chain to ensure effective and profitable production, particularly for safety-related products such as driver airbags.
The Challenge
Eissmann Automotive faced the challenge of maintaining high-quality production standards while ensuring complete traceability and efficiency in their complex production processes. The company needed to digitize its entire process chain to monitor every production step, especially for safety-related products like driver airbags. Manual data evaluation methods were prone to errors, and there was a lack of transparency and traceability in the purchasing process. Additionally, the company needed to optimize its master data management to support various business processes effectively.
The Solution
Eissmann Automotive implemented Celonis Process Mining technology to monitor and optimize various business processes, including Purchase-to-Pay (P2P), Master Data Management (MDM), production, manufacturing management, and purchasing. The technology enabled the company to track and visualize the production cycle in real-time, identify bottlenecks, and uncover optimization potential. By connecting the Manufacturing Execution System (MES) to an AS-400 or SQL database, data from production processes were transmitted to the Celonis software for real-time tracking and analysis. This allowed Eissmann Automotive to achieve complete traceability, unify data evaluation, and make informed decisions to improve production efficiency. Additionally, Celonis Process Mining was used in master data management to ensure accurate and timely data availability, leading to significant process improvements and reduced throughput times. In purchasing, the technology provided transparency and traceability, enabling better supplier management and strategic purchasing decisions.
Operational Impact
Quantitative Benefit
Case Study missing?
Start adding your own!
Register with your work email and create a new case study profile for your business.
Related Case Studies.
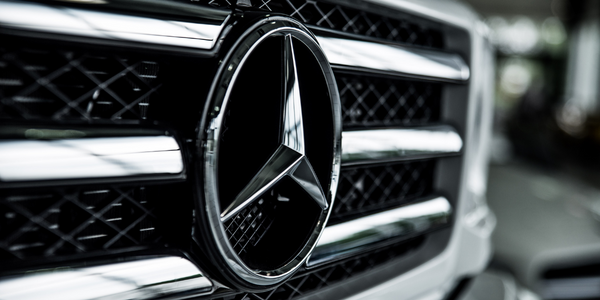
Case Study
Integral Plant Maintenance
Mercedes-Benz and his partner GAZ chose Siemens to be its maintenance partner at a new engine plant in Yaroslavl, Russia. The new plant offers a capacity to manufacture diesel engines for the Russian market, for locally produced Sprinter Classic. In addition to engines for the local market, the Yaroslavl plant will also produce spare parts. Mercedes-Benz Russia and his partner needed a service partner in order to ensure the operation of these lines in a maintenance partnership arrangement. The challenges included coordinating the entire maintenance management operation, in particular inspections, corrective and predictive maintenance activities, and the optimizing spare parts management. Siemens developed a customized maintenance solution that includes all electronic and mechanical maintenance activities (Integral Plant Maintenance).
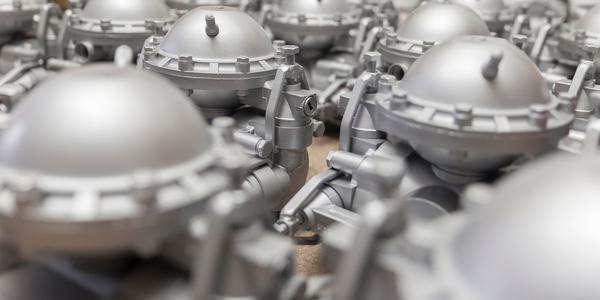
Case Study
Monitoring of Pressure Pumps in Automotive Industry
A large German/American producer of auto parts uses high-pressure pumps to deburr machined parts as a part of its production and quality check process. They decided to monitor these pumps to make sure they work properly and that they can see any indications leading to a potential failure before it affects their process.