Company Size
1,000+
Region
- America
Country
- United States
Product
- Factory MES
Tech Stack
- Manufacturing operations management system
Implementation Scale
- Enterprise-wide Deployment
Impact Metrics
- Cost Savings
- Productivity Improvements
- Revenue Growth
Technology Category
- Functional Applications - Manufacturing Execution Systems (MES)
Applicable Industries
- Food & Beverage
Applicable Functions
- Discrete Manufacturing
- Quality Assurance
Use Cases
- Manufacturing System Automation
- Predictive Maintenance
Services
- System Integration
About The Customer
Berner Foods is a market-leading supplier of quality food products, including natural cheese, specialty performance cheese, processed cheese and soy beverages. The company offers leading-edge products to the supermarket, drug, mass merchandiser, club, dollar store, specialty food distributor, foodservice and contract manufacturing channels. Its facilities are USDA- and AIB-approved and ISO 9001 certified and meet the demanding standards of virtually every major retailer in North America.
The Challenge
Berner Foods, a leading supplier of quality food products, was facing several challenges. The company lacked complete information from the shop floor, which prevented them from identifying and addressing root causes of inefficiencies. They were also struggling with capacity constraints, as they were unable to determine the root causes of production inefficiency and capacity constraints. This lack of visibility was restricting their capacity and business growth. Additionally, production personnel were spending hundreds of man-hours every week filling out dozens of forms. Supervisors alone were spending between two and four hours every day on paperwork.
The Solution
Berner Foods implemented Factory MES, a manufacturing operations management (MES) system from Aptean. This system offered a short implementation time and a much shorter learning curve and faster time to value than competing options. Factory MES enabled Berner to employ Lean and Six Sigma principles to reduce waste and unlock capacity. The system provided real-time data, enabling the company to make better and more timely decisions. Factory MES also reduced factory floor paperwork by 40 percent, leading to an immediate $30,000 annual labor savings. The system has become a strategic management tool for Berner, providing better access to data for finance, marketing and sales departments.
Operational Impact
Quantitative Benefit
Case Study missing?
Start adding your own!
Register with your work email and create a new case study profile for your business.
Related Case Studies.

Case Study
The Kellogg Company
Kellogg keeps a close eye on its trade spend, analyzing large volumes of data and running complex simulations to predict which promotional activities will be the most effective. Kellogg needed to decrease the trade spend but its traditional relational database on premises could not keep up with the pace of demand.

Case Study
HEINEKEN Uses the Cloud to Reach 10.5 Million Consumers
For 2012 campaign, the Bond promotion, it planned to launch the campaign at the same time everywhere on the planet. That created unprecedented challenges for HEINEKEN—nowhere more so than in its technology operation. The primary digital content for the campaign was a 100-megabyte movie that had to play flawlessly for millions of viewers worldwide. After all, Bond never fails. No one was going to tolerate a technology failure that might bruise his brand.Previously, HEINEKEN had supported digital media at its outsourced datacenter. But that datacenter lacked the computing resources HEINEKEN needed, and building them—especially to support peak traffic that would total millions of simultaneous hits—would have been both time-consuming and expensive. Nor would it have provided the geographic reach that HEINEKEN needed to minimize latency worldwide.

Case Study
Energy Management System at Sugar Industry
The company wanted to use the information from the system to claim under the renewable energy certificate scheme. The benefit to the company under the renewable energy certificates is Rs 75 million a year. To enable the above, an end-to-end solution for load monitoring, consumption monitoring, online data monitoring, automatic meter data acquisition which can be exported to SAP and other applications is required.

Case Study
Coca Cola Swaziland Conco Case Study
Coco Cola Swaziland, South Africa would like to find a solution that would enable the following results: - Reduce energy consumption by 20% in one year. - Formulate a series of strategic initiatives that would enlist the commitment of corporate management and create employee awareness while helping meet departmental targets and investing in tools that assist with energy management. - Formulate a series of tactical initiatives that would optimize energy usage on the shop floor. These would include charging forklifts and running cold rooms only during off-peak periods, running the dust extractors only during working hours and basing lights and air-conditioning on someone’s presence. - Increase visibility into the factory and other processes. - Enable limited, non-intrusive control functions for certain processes.

Case Study
Temperature Monitoring for Restaurant Food Storage
When it came to implementing a solution, Mr. Nesbitt had an idea of what functionality that he wanted. Although not mandated by Health Canada, Mr. Nesbitt wanted to ensure quality control issues met the highest possible standards as part of his commitment to top-of-class food services. This wish list included an easy-to use temperature-monitoring system that could provide a visible display of the temperatures of all of his refrigerators and freezers, including historical information so that he could review the performance of his equipment. It also had to provide alert notification (but email alerts and SMS text message alerts) to alert key staff in the event that a cooling system was exceeding pre-set warning limits.
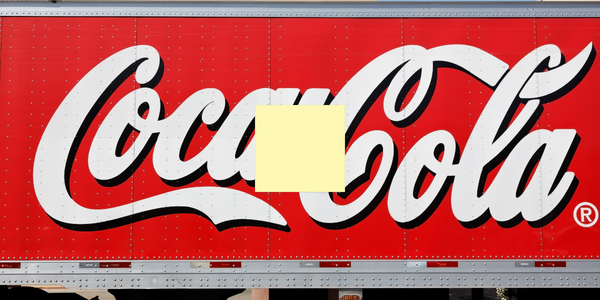
Case Study
Coca-Cola Refreshments, U.S.
Coca-Cola Refreshments owns and manages Coca-Cola branded refrigerators in retail establishments. Legacy systems were used to locate equipment information by logging onto multiple servers which took up to 8 hours to update information on 30-40 units. The company had no overall visibility into equipment status or maintenance history.