Customer Company Size
Large Corporate
Region
- Pacific
Country
- Australia
Product
- Cumulocity IoT
Tech Stack
- IoT
- Real-time data analytics
- Machine Learning
Implementation Scale
- Enterprise-wide Deployment
Impact Metrics
- Cost Savings
- Productivity Improvements
- Customer Satisfaction
Technology Category
- Platform as a Service (PaaS) - Connectivity Platforms
- Analytics & Modeling - Real Time Analytics
Applicable Industries
- Food & Beverage
Applicable Functions
- Logistics & Transportation
- Quality Assurance
Use Cases
- Supply Chain Visibility
- Predictive Quality Analytics
- Real-Time Location System (RTLS)
Services
- System Integration
- Software Design & Engineering Services
About The Customer
Bega Cheese is an Australian diversified food company and one of the largest dairy producers in the country. It was originally founded as a dairy cooperative in 1899 with a number of its shares still held by Bega's farmer-suppliers. Headquartered in Bega, and with manufacturing sites in New South Wales, Queensland and Victoria, over half of Bega Cheese's revenue (as of 2019) comes from its spreads, dairy consumer packaged goods and other grocery products. Bega Cheese is a master at making cheese; its flagship Bega brand holds 15.7% of the Australian retail cheese market. But it has other iconic brands, too, such as the world- famous Vegemite spread, Picky Picky peanuts and Zoosh French onion dip. And it is not just Australians that like Bega; about a third of its revenues (as of 2019) came from exports of dairy products to around 40 countries around the world.
The Challenge
Bega Cheese, a major player in the Australian dairy industry, faced challenges in its supply chain. The process was almost entirely manual, with farmers having to test milk quality and check vat levels themselves, then phone in the data to Bega Cheese. If there was extra production, Bega Cheese would have to rush to get tankers there quickly—if they were available. Milk tankers could sometimes deliver too-warm milk—or shaken-up milk (which changes the quality). The supply chain had to be much faster, and much more efficient. The company wanted to improve the efficiency of its supply chain, increasing efficiency and improving visibility to address these unique challenges.
The Solution
Bega Cheese turned to the Internet of Things for a solution. They partnered with Swinburne University of Technology, which—with its IoT lab and Industry 4.0 initiative—was an ideal choice for Bega. Swinburne did a lot of the heavy lifting to get the project off the ground, which included successfully applying for a research grant from the federal government’s Cooperative Research Centres Projects (CRC-P). The project to optimise the productivity and competitiveness of Australia’s dairy industry, is in collaboration with Bega Cheese and three Australian milk suppliers initially—then scaling to 100+ suppliers. NBioT was selected as the network technology type to be used with new sensors. Then, what the project needed was an IoT platform that could start small, start quickly and then scale smoothly to include Bega Cheese’s 100+ suppliers. That is where Software AG was brought in—to scale up the 2.5-year project with its Cumulocity IoT platform.
Operational Impact
Quantitative Benefit
Case Study missing?
Start adding your own!
Register with your work email and create a new case study profile for your business.
Related Case Studies.

Case Study
The Kellogg Company
Kellogg keeps a close eye on its trade spend, analyzing large volumes of data and running complex simulations to predict which promotional activities will be the most effective. Kellogg needed to decrease the trade spend but its traditional relational database on premises could not keep up with the pace of demand.

Case Study
HEINEKEN Uses the Cloud to Reach 10.5 Million Consumers
For 2012 campaign, the Bond promotion, it planned to launch the campaign at the same time everywhere on the planet. That created unprecedented challenges for HEINEKEN—nowhere more so than in its technology operation. The primary digital content for the campaign was a 100-megabyte movie that had to play flawlessly for millions of viewers worldwide. After all, Bond never fails. No one was going to tolerate a technology failure that might bruise his brand.Previously, HEINEKEN had supported digital media at its outsourced datacenter. But that datacenter lacked the computing resources HEINEKEN needed, and building them—especially to support peak traffic that would total millions of simultaneous hits—would have been both time-consuming and expensive. Nor would it have provided the geographic reach that HEINEKEN needed to minimize latency worldwide.

Case Study
Energy Management System at Sugar Industry
The company wanted to use the information from the system to claim under the renewable energy certificate scheme. The benefit to the company under the renewable energy certificates is Rs 75 million a year. To enable the above, an end-to-end solution for load monitoring, consumption monitoring, online data monitoring, automatic meter data acquisition which can be exported to SAP and other applications is required.

Case Study
Coca Cola Swaziland Conco Case Study
Coco Cola Swaziland, South Africa would like to find a solution that would enable the following results: - Reduce energy consumption by 20% in one year. - Formulate a series of strategic initiatives that would enlist the commitment of corporate management and create employee awareness while helping meet departmental targets and investing in tools that assist with energy management. - Formulate a series of tactical initiatives that would optimize energy usage on the shop floor. These would include charging forklifts and running cold rooms only during off-peak periods, running the dust extractors only during working hours and basing lights and air-conditioning on someone’s presence. - Increase visibility into the factory and other processes. - Enable limited, non-intrusive control functions for certain processes.

Case Study
Temperature Monitoring for Restaurant Food Storage
When it came to implementing a solution, Mr. Nesbitt had an idea of what functionality that he wanted. Although not mandated by Health Canada, Mr. Nesbitt wanted to ensure quality control issues met the highest possible standards as part of his commitment to top-of-class food services. This wish list included an easy-to use temperature-monitoring system that could provide a visible display of the temperatures of all of his refrigerators and freezers, including historical information so that he could review the performance of his equipment. It also had to provide alert notification (but email alerts and SMS text message alerts) to alert key staff in the event that a cooling system was exceeding pre-set warning limits.
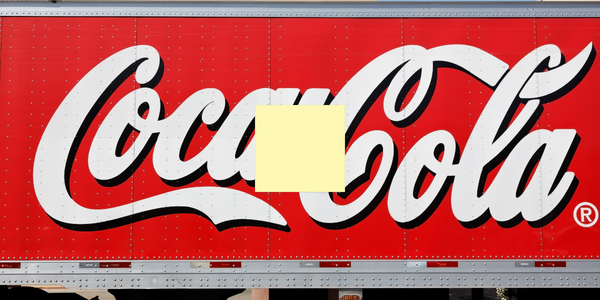
Case Study
Coca-Cola Refreshments, U.S.
Coca-Cola Refreshments owns and manages Coca-Cola branded refrigerators in retail establishments. Legacy systems were used to locate equipment information by logging onto multiple servers which took up to 8 hours to update information on 30-40 units. The company had no overall visibility into equipment status or maintenance history.