Company Size
1,000+
Region
- America
- Asia
- Europe
Country
- Germany
Product
- Stature system
Tech Stack
- Risk Assessment
- Process Hazard Analysis (PHA)
- Action item tracking
Implementation Scale
- Enterprise-wide Deployment
Impact Metrics
- Brand Awareness
- Customer Satisfaction
- Productivity Improvements
Technology Category
- Analytics & Modeling - Process Analytics
- Application Infrastructure & Middleware - Data Exchange & Integration
Applicable Industries
- Chemicals
Applicable Functions
- Discrete Manufacturing
- Quality Assurance
Use Cases
- Predictive Maintenance
- Process Control & Optimization
Services
- System Integration
- Training
About The Customer
BASF is the world’s largest chemical producer with 2014 sales approaching €75 billion. The company operates on the principle of combining economic success with environmental protection and social responsibility. This German-based company is highly focused on the need for its operations around the world to follow strict, well-defined processes that ensure plant and worker safety as well as protecting nearby communities and ecosystems. As part of its commitment to continuous improvement, BASF embarked on a project to streamline the documentation and management of risks associated with Safety, Health & Environment (SHE).
The Challenge
BASF, the world’s largest chemical producer, was facing challenges in managing plant risks and safety processes. The company was using Word, Excel, or specialized desktop software to document process hazards, leading to inconsistencies in documentation across the global organization. Staff members were using different languages for classification and different methods for HAZOP assessments and data collection. This lack of consistency limited the visibility of BASF managers across facilities and hindered comparisons of issues and safeguards. Comparisons had to be done 'intellectually', by experienced staff reviewing documents that were up to 300 pages long, which was inefficient, time-consuming, and labor-intensive.
The Solution
BASF implemented the Stature system for risk assessment, process hazard analysis (PHA), and action item tracking. The company trained 1,600 staff members across Europe, Asia, and the Americas to use the system within the first nine months of implementation. Staff in all locations now enter data into a single template that uses standardized language and measurements. The system has enabled BASF to build a central risk knowledge base and gain better visibility across the organization. Managers can now see the status of items and prioritize workloads for the next few years. The system also facilitates the revalidation process, setting all necessary dates and giving BASF staff an overview of plans and dates.
Operational Impact
Quantitative Benefit
Case Study missing?
Start adding your own!
Register with your work email and create a new case study profile for your business.
Related Case Studies.
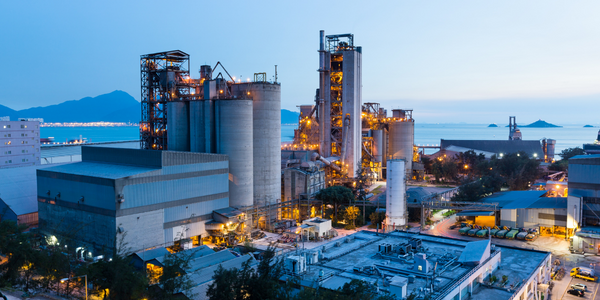
Case Study
Honeywell - Tata Chemicals Improves Data Accessibility with OneWireless
Tata was facing data accessibility challenges in the cement plant control room tapping signals from remote process control areas and other distant locations, including the gas scrubber. Tata needed a wireless solution to extend its control network securely to remote locations that would also provide seamless communication with existing control applications.

Case Study
Advanced Elastomer Systems Upgrades Production
In order to maintain its share of the international market for thermoplastic elastomers AES recently expanded its Florida plant by adding a new production line. While the existing lines were operating satisfactorily using a PROVOX distributed control system with traditional analog I/O, AES wanted advanced technology on the new line for greater economy, efficiency, and reliability. AES officials were anxious to get this line into production to meet incoming orders, but two hurricanes slowed construction.
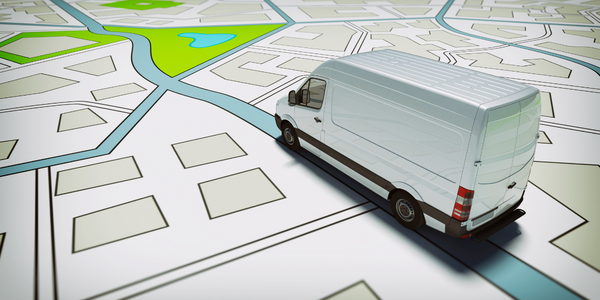
Case Study
Wireless GPS Tracking & Security Monitoring
Enhancing the security of hazardous freight and ensuring compliance with Homeland Security’s Transportation Security Administration mandate that all trains carrying chemicals capable of creating a toxic inhalation condition are equipped with on-board safety monitoring systems.
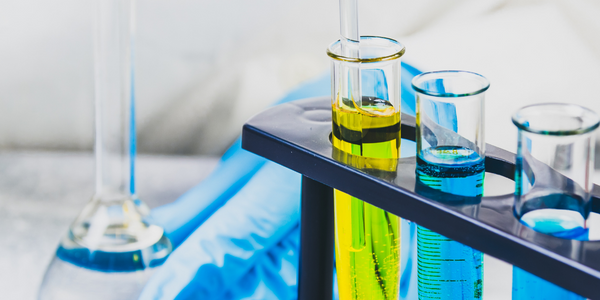
Case Study
Field Device Asset Management For Chemical Company in China
Chinese chemical subsidiary of multinational corporation serves customers throughout the world. Sales offices and research and technology centers are strategically located to provide rapid response to customer requests. Just two workers were assigned to maintain thousands of intelligent instruments in three production units, so they could do little more than react to device issues as they appeared. This costly maintenance method inevitably led to unexpected downtime when a critical instrument failed. Plant management recognized the need to change from reactive to predictive maintenance for all assets, including instruments and control valves, but help was needed in implementing such a technology-based initiative.
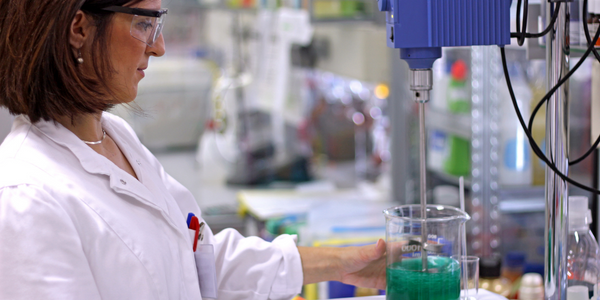
Case Study
Industrial Workforce Mobility for Improved Safety & Operations
Huntsman Corporation, a global manufacturer and marketer of differentiated chemicals, undertook an aggressive program to eliminate injuries, product defects, and environmental releases at their Port Neches facility. Termed “Project Zero”, this program required a completely mobile solution to empower operations and maintenance personnel to capture defects, track work progress and make process and safety related decisions in real-time.