Technology Category
- Application Infrastructure & Middleware - Data Exchange & Integration
- Platform as a Service (PaaS) - Application Development Platforms
Applicable Industries
- Automotive
- Education
Applicable Functions
- Human Resources
- Quality Assurance
Use Cases
- Inventory Management
- Visual Quality Detection
Services
- System Integration
- Testing & Certification
About The Customer
Balboa Digital is a California-based company that provides high-quality, affordable contact center solutions, including outsourced inbound and outbound call center, chat, and email services for various industries such as education, finance, and automotive. The company operates a 100-seat call center in Manila, Philippines. Balboa Digital's success is largely attributed to its flexibility in meeting its clients' unique needs for technical integration and telephony support. The company is committed to delivering the highest quality call center solutions and meeting varied client needs at a very competitive cost.
The Challenge
Balboa Digital, a provider of high-quality contact center solutions, was facing a significant challenge with its existing telephony provider. The VoIP office phone system was inflexible and incompatible with third-party systems, preventing integration with Balboa's agent management system. This led to inefficiencies such as idle times between calls and difficulties in transferring calls. The system also lacked necessary recording and reporting capabilities, hindering Balboa's ability to monitor and coach its agents effectively. Furthermore, the reliability of the service was a major concern, with Balboa having to resort to a secondary provider for emergencies. Traditional telecom providers were found to be too expensive for customization and did not provide all the necessary services. On the other hand, open-source solutions lacked sophisticated customer support and a global telephony footprint. Balboa needed a solution that offered flexibility, comprehensive services, customizable solutions, and excellent customer service at a competitive cost.
The Solution
Balboa Digital turned to Twilio, a platform designed for integration and competitive pay-as-you-go pricing. Twilio enabled Balboa to quickly and easily onboard contact center agents anywhere in the world at a low cost. It also offered fundamental call center features such as queuing, recording, conferencing, and reporting. With Twilio, Balboa was able to replicate, improve, and integrate all its existing call center features into custom software, allowing for a smooth migration path. The migration to Twilio was relatively invisible to clients, demonstrating Twilio's ease of use and flexibility to deliver highly customized solutions. By integrating Twilio with Balboa's agent management software, the company created a highly functional contact center desktop, reducing the time between agent activities and increasing staff efficiency. Today, Balboa's distributed workforce relies on Twilio's browser-based, customized soft phone capabilities for both inbound and outbound calling.
Operational Impact
Quantitative Benefit
Case Study missing?
Start adding your own!
Register with your work email and create a new case study profile for your business.
Related Case Studies.
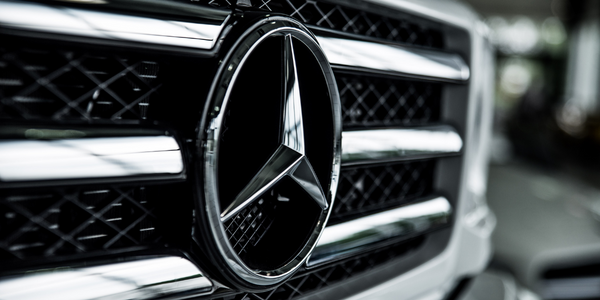
Case Study
Integral Plant Maintenance
Mercedes-Benz and his partner GAZ chose Siemens to be its maintenance partner at a new engine plant in Yaroslavl, Russia. The new plant offers a capacity to manufacture diesel engines for the Russian market, for locally produced Sprinter Classic. In addition to engines for the local market, the Yaroslavl plant will also produce spare parts. Mercedes-Benz Russia and his partner needed a service partner in order to ensure the operation of these lines in a maintenance partnership arrangement. The challenges included coordinating the entire maintenance management operation, in particular inspections, corrective and predictive maintenance activities, and the optimizing spare parts management. Siemens developed a customized maintenance solution that includes all electronic and mechanical maintenance activities (Integral Plant Maintenance).
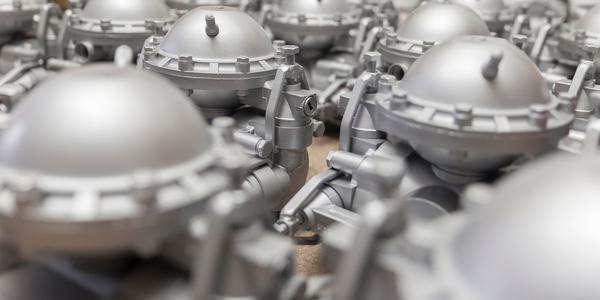
Case Study
Monitoring of Pressure Pumps in Automotive Industry
A large German/American producer of auto parts uses high-pressure pumps to deburr machined parts as a part of its production and quality check process. They decided to monitor these pumps to make sure they work properly and that they can see any indications leading to a potential failure before it affects their process.