Bakkavör Improves Food Service Operation with Manhattan Warehouse Management Solution
Company Size
1,000+
Region
- Africa
- America
- Asia
- Europe
Country
- Belgium
- China
- Czech Republic
- France
- Iceland
- South Africa
- Spain
- United Kingdom
- United States
Product
- Manhattan Warehouse Management
- LXE MX2 Hand-held Scanners
- LXE VX1 Truck-mounted Scanners
Tech Stack
- Microsoft-based Architecture
- Radio Frequency (RF) Technology
- Windows 2000
Implementation Scale
- Enterprise-wide Deployment
Impact Metrics
- Cost Savings
- Customer Satisfaction
- Productivity Improvements
Technology Category
- Functional Applications - Warehouse Management Systems (WMS)
Applicable Industries
- Food & Beverage
- Retail
Applicable Functions
- Logistics & Transportation
- Warehouse & Inventory Management
Use Cases
- Inventory Management
- Supply Chain Visibility
- Warehouse Automation
Services
- Software Design & Engineering Services
- System Integration
About The Customer
Bakkavör Group is a leading international food manufacturing company specializing in fresh prepared foods and produce. The Group operates 66 factories and employs over 20,000 people across ten countries, including the UK, Iceland, France, Belgium, Spain, South Africa, China, the Czech Republic, and the United States. The company generates 88% of its revenue from customers in the UK, 10% from Continental Europe, and 2% from the rest of the world. Bakkavör Group produces over 6,000 products in 18 product categories, primarily developed and sold under its customers' brands. The company has seen significant growth, outpacing the market, and has become essential to improve its supply chain systems to maintain and advance its market-leading position.
The Challenge
Bakkavör was experiencing rapid market growth and faced challenges due to a lack of coordination and integration among its systems and facilities. The company's order processing and transaction systems were minimally integrated with its existing warehouse management software, necessitating a paper-based system for orders, picking, dispatching, and reporting. Additionally, multiple Bakkavör food companies operated from various factories on the same site, feeding into seven different warehouses. This situation required the company to consolidate its operational facilities and apply a single system for managing and fulfilling orders. To maintain its market-leading position in the fresh food market, where short production cycles and order accuracy are critical, Bakkavör needed to implement a new and unified Warehouse Management system.
The Solution
Bakkavör chose Manhattan Associates to provide a Warehouse Management system to integrate all its systems and streamline distribution center processes. The company centralized its fulfillment operation in a new distribution center in Spalding, Lincolnshire, and replaced its manual paper-based environment with a paperless Radio Frequency (RF)-driven operation managed by Manhattan's Warehouse Management solution. The project, including the design and construction of a state-of-the-art chilled facility, was completed within six months. The Manhattan solution now manages the distribution of Bakkavör's salads, soups, sauces, dips, dressings, and ready meals to major stores throughout the UK and Northern Europe. The implementation of the new system allowed Bakkavör to achieve total visibility across the supply chain, increase customer service levels, reduce distribution center space needs, and enhance productivity.
Operational Impact
Quantitative Benefit
Case Study missing?
Start adding your own!
Register with your work email and create a new case study profile for your business.
Related Case Studies.

Case Study
The Kellogg Company
Kellogg keeps a close eye on its trade spend, analyzing large volumes of data and running complex simulations to predict which promotional activities will be the most effective. Kellogg needed to decrease the trade spend but its traditional relational database on premises could not keep up with the pace of demand.

Case Study
HEINEKEN Uses the Cloud to Reach 10.5 Million Consumers
For 2012 campaign, the Bond promotion, it planned to launch the campaign at the same time everywhere on the planet. That created unprecedented challenges for HEINEKEN—nowhere more so than in its technology operation. The primary digital content for the campaign was a 100-megabyte movie that had to play flawlessly for millions of viewers worldwide. After all, Bond never fails. No one was going to tolerate a technology failure that might bruise his brand.Previously, HEINEKEN had supported digital media at its outsourced datacenter. But that datacenter lacked the computing resources HEINEKEN needed, and building them—especially to support peak traffic that would total millions of simultaneous hits—would have been both time-consuming and expensive. Nor would it have provided the geographic reach that HEINEKEN needed to minimize latency worldwide.
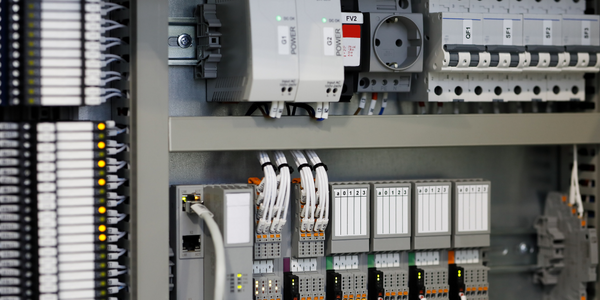
Case Study
Improving Production Line Efficiency with Ethernet Micro RTU Controller
Moxa was asked to provide a connectivity solution for one of the world's leading cosmetics companies. This multinational corporation, with retail presence in 130 countries, 23 global braches, and over 66,000 employees, sought to improve the efficiency of their production process by migrating from manual monitoring to an automatic productivity monitoring system. The production line was being monitored by ABB Real-TPI, a factory information system that offers data collection and analysis to improve plant efficiency. Due to software limitations, the customer needed an OPC server and a corresponding I/O solution to collect data from additional sensor devices for the Real-TPI system. The goal is to enable the factory information system to more thoroughly collect data from every corner of the production line. This will improve its ability to measure Overall Equipment Effectiveness (OEE) and translate into increased production efficiencies. System Requirements • Instant status updates while still consuming minimal bandwidth to relieve strain on limited factory networks • Interoperable with ABB Real-TPI • Small form factor appropriate for deployment where space is scarce • Remote software management and configuration to simplify operations

Case Study
Energy Management System at Sugar Industry
The company wanted to use the information from the system to claim under the renewable energy certificate scheme. The benefit to the company under the renewable energy certificates is Rs 75 million a year. To enable the above, an end-to-end solution for load monitoring, consumption monitoring, online data monitoring, automatic meter data acquisition which can be exported to SAP and other applications is required.
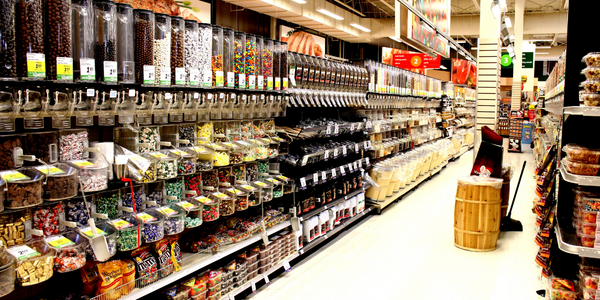
Case Study
How Sirqul’s IoT Platform is Crafting Carrefour’s New In-Store Experiences
Carrefour Taiwan’s goal is to be completely digital by end of 2018. Out-dated manual methods for analysis and assumptions limited Carrefour’s ability to change the customer experience and were void of real-time decision-making capabilities. Rather than relying solely on sales data, assumptions, and disparate systems, Carrefour Taiwan’s CEO led an initiative to find a connected IoT solution that could give the team the ability to make real-time changes and more informed decisions. Prior to implementing, Carrefour struggled to address their conversion rates and did not have the proper insights into the customer decision-making process nor how to make an immediate impact without losing customer confidence.