Auto Components Growth Drives to MES with a Future
Customer Company Size
Large Corporate
Region
- Europe
Country
- Portugal
Product
- Critical Manufacturing’s MES
- SAP
Tech Stack
- MES
- ERP
Implementation Scale
- Enterprise-wide Deployment
Impact Metrics
- Productivity Improvements
- Cost Savings
Technology Category
- Functional Applications - Manufacturing Execution Systems (MES)
- Functional Applications - Enterprise Resource Planning Systems (ERP)
Applicable Industries
- Automotive
Applicable Functions
- Discrete Manufacturing
Use Cases
- Manufacturing System Automation
- Predictive Maintenance
Services
- System Integration
- Software Design & Engineering Services
About The Customer
Yazaki Saltano is a Portugal-based company that is part of the Yazaki Group, which has 476 locations worldwide. The company specializes in the production of a variety of wire, cable, and wiring harnesses used by many automotive Original Equipment Manufacturers (OEMs). The MES was implemented in the plastic injection-molded parts division of Yazaki Saltano. The company was planning to add many more molding machines to its operation, which was being managed with paper records and Excel spreadsheets. The company had previously attempted to implement an MES, but the project had failed due to unreliable communication between the molding machines and the MES.
The Challenge
Yazaki Saltano, a molded plastic parts supplier in Portugal, was facing challenges in managing its high-volume molding operation with paper records and Excel. The company was planning to add many more molding machines and realized that it needed a more robust control system. A previous attempt to implement a Manufacturing Execution System (MES) had failed due to unreliable communication between the molding machines and the MES. This, coupled with plans to add even more machines, created a strong incentive for Yazaki Saltano to choose the right partner and succeed with the MES implementation.
The Solution
Yazaki Saltano selected Critical Manufacturing’s MES to connect to dozens of existing and new molding machines. The implementation project started and progressed smoothly, with daily half-hour status meetings and an agile approach that allowed the team to see screens as they were configured. A few months into the project, it was put on hold due to a slow wide area network (WAN), but once this issue was resolved, the team was able to finish the project. The implementation included Critical Manufacturing’s core modules for MES, statistical process control (SPC), ERP integration, and machine connection. Yazaki provided new computers and touch-screen tablets for operators to use the MES Graphical User Interface (GUI) cockpit.
Operational Impact
Quantitative Benefit
Case Study missing?
Start adding your own!
Register with your work email and create a new case study profile for your business.
Related Case Studies.
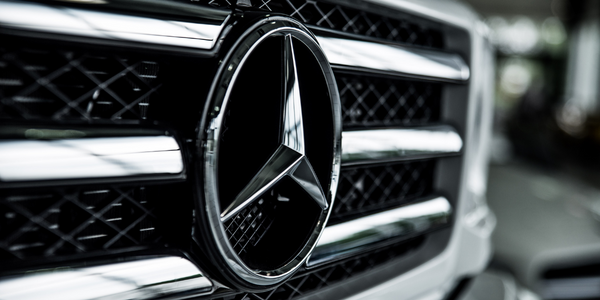
Case Study
Integral Plant Maintenance
Mercedes-Benz and his partner GAZ chose Siemens to be its maintenance partner at a new engine plant in Yaroslavl, Russia. The new plant offers a capacity to manufacture diesel engines for the Russian market, for locally produced Sprinter Classic. In addition to engines for the local market, the Yaroslavl plant will also produce spare parts. Mercedes-Benz Russia and his partner needed a service partner in order to ensure the operation of these lines in a maintenance partnership arrangement. The challenges included coordinating the entire maintenance management operation, in particular inspections, corrective and predictive maintenance activities, and the optimizing spare parts management. Siemens developed a customized maintenance solution that includes all electronic and mechanical maintenance activities (Integral Plant Maintenance).
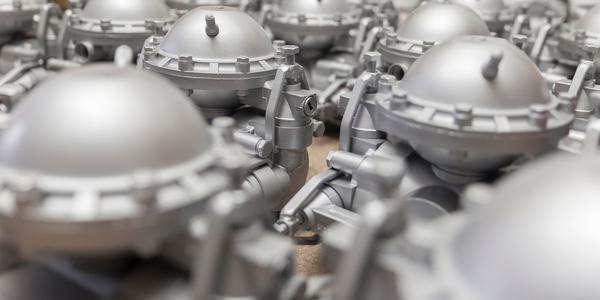
Case Study
Monitoring of Pressure Pumps in Automotive Industry
A large German/American producer of auto parts uses high-pressure pumps to deburr machined parts as a part of its production and quality check process. They decided to monitor these pumps to make sure they work properly and that they can see any indications leading to a potential failure before it affects their process.