Annex Products Pty. Ltd. Taking the Lead in Smartphone Mounting Systems Development with SOLIDWORKS Professional
Customer Company Size
SME
Country
- Australia
Product
- SOLIDWORKS Professional
- PhotoView 360
- Ultimaker 2+ FDM 3D printer
- Form 1+ SLA machine
Tech Stack
- 3D Design Software
- Fused Deposition Modeling (FDM)
- Stereolithography (SLA)
Implementation Scale
- Enterprise-wide Deployment
Impact Metrics
- Revenue Growth
- Productivity Improvements
- Customer Satisfaction
Technology Category
- Functional Applications - Product Lifecycle Management Systems (PLM)
- Functional Applications - Manufacturing Execution Systems (MES)
- Functional Applications - Product Data Management Systems
Applicable Industries
- Consumer Goods
- Electronics
Applicable Functions
- Product Research & Development
- Quality Assurance
Use Cases
- Rapid Prototyping
- Manufacturing System Automation
Services
- Software Design & Engineering Services
- System Integration
About The Customer
With ideas for creating unique smartphone accessories, Chris Peters and Rob Ward founded Annex Products in 2012, off the back of two successful Kickstarter campaigns. The first was for an iPhone® case that doubles as a bottle opener (the Opena® Case), and the second was for a smartphone mounting system (the Quad Lock®) that supports active lifestyles. While the Opena Case made a big splash, with rave reviews, the success of the Quad Lock mounting system—for securing smartphones to bicycles, armbands, a car dashboard, or other locations—has exceeded expectations so dramatically that it has become the company’s main consumer-facing brand. The Quad Lock is the lightest, strongest, and most secure iPhone mounting system on the market. Its patent-pending, dual-stage locking mechanism makes it possible for a single case to provide a mounting solution for cycling, running, driving, and more. The Quad Lock is available worldwide with sales in more than 100 countries. Its market impact, innovative design, and high production quality have prompted Apple to put the product through its rigorous testing regimen and begin selling the Quad Lock alongside its iPhones.
The Challenge
Establish and grow a startup smartphone accessory products company through fast, effective new product design and production to support newly launched smartphone models more quickly than the competition.
The Solution
Implement SOLIDWORKS Professional design software. Using SOLIDWORKS Professional design software, Annex quickly developed Quad Lock designs for every new iPhone model since 2011—as well as Samsung Galaxy smartphones—designing, testing, manufacturing, and delivering new products in a matter of weeks. The company’s design agility has helped it increase annual revenue from zero in 2011 to $10 million in 2016. Annex has received several awards for the Quad Lock design, and with more than half a million units sold, the company has grown from a startup to a market leader. Annex also utilizes the mold development and analysis tools in SOLIDWORKS Professional software—particularly the draft analysis tools—to ensure the manufacturability of its parts, most of which are injection-molded by a moldmaker and manufacturing partner. “SOLIDWORKS draft analysis is critical for us to not only guarantee that our parts will pop out of the molds but also to work out where the parting lines and injection points should go. It’s a key tool for assessing the manufacturability of our products,” Peters says.
Operational Impact
Quantitative Benefit
Case Study missing?
Start adding your own!
Register with your work email and create a new case study profile for your business.
Related Case Studies.
.png)
Case Study
Improving Vending Machine Profitability with the Internet of Things (IoT)
The vending industry is undergoing a sea change, taking advantage of new technologies to go beyond just delivering snacks to creating a new retail location. Intelligent vending machines can be found in many public locations as well as company facilities, selling different types of goods and services, including even computer accessories, gold bars, tickets, and office supplies. With increasing sophistication, they may also provide time- and location-based data pertaining to sales, inventory, and customer preferences. But at the end of the day, vending machine operators know greater profitability is driven by higher sales and lower operating costs.

Case Study
Remote Temperature Monitoring of Perishable Goods Saves Money
RMONI was facing temperature monitoring challenges in a cold chain business. A cold chain must be established and maintained to ensure goods have been properly refrigerated during every step of the process, making temperature monitoring a critical business function. Manual registration practice can be very costly, labor intensive and prone to mistakes.
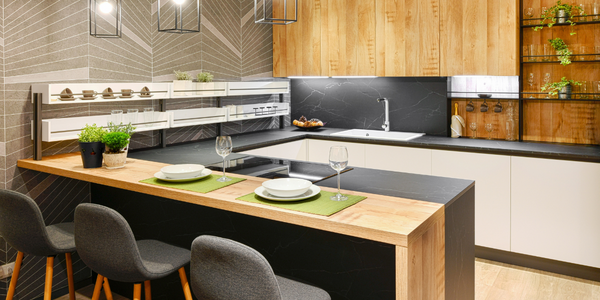
Case Study
Series Production with Lot-size-1 Flexibility
Nobilia manufactures customized fitted kitchens with a lot size of 1. They require maximum transparency of tracking design data and individual processing steps so that they can locate a particular piece of kitchen furniture in the sequence of processes.