Allied Hygiene Successfully Gains Stock Control
Customer Company Size
Mid-size Company
Region
- Europe
Country
- United Kingdom
Product
- NetSuite
- RF-SMART
Tech Stack
- Mobile Barcoding Solution
- ERP System
Implementation Scale
- Enterprise-wide Deployment
Impact Metrics
- Productivity Improvements
- Cost Savings
- Customer Satisfaction
Technology Category
- Functional Applications - Warehouse Management Systems (WMS)
- Functional Applications - Manufacturing Execution Systems (MES)
Applicable Industries
- Consumer Goods
- Chemicals
Applicable Functions
- Warehouse & Inventory Management
Use Cases
- Inventory Management
- Predictive Maintenance
- Warehouse Automation
Services
- System Integration
- Training
About The Customer
Allied Hygiene is a British manufacturer and international distributor of industrial wipe products. The company has a significant presence in the market, providing essential hygiene products to various industries. With a focus on quality and efficiency, Allied Hygiene has been striving to improve its operational processes to better serve its customers. The company recently upgraded its ERP system to NetSuite, aiming to enhance its inventory management and overall operational efficiency. Allied Hygiene's commitment to innovation and customer satisfaction drives its continuous efforts to optimize its processes and adopt new technologies.
The Challenge
Allied Hygiene faced significant challenges in maintaining accurate inventory counts due to their manual, paper-based methods. Despite consolidating their warehouse operations from 10 locations to one, they struggled with stock inaccuracies, leading to difficulties in fulfilling sales orders and lengthy, error-prone stock counts. The manual process of entering stock data was time-consuming and often resulted in errors, making it difficult to maintain an accurate inventory. This inefficiency affected their ability to provide timely information to customers regarding order statuses and led to operational delays.
The Solution
Allied Hygiene implemented RF-SMART, a mobile barcoding solution, to address their inventory management challenges. The solution was recommended by their NetSuite implementation partner and quickly proved effective in improving inventory control. RF-SMART's functions, such as sales order picking, goods receiving, item inquiry, and bin transfers, helped tighten inventory control and reduce errors. The real-time data provided by RF-SMART allowed for rapid improvements in accuracy and efficiency. The implementation of cycle counting further enhanced their inventory accuracy, increasing it from 75% to 99.6%. This allowed Allied Hygiene to conduct stock counts less frequently and with fewer resources. Additionally, RF-SMART was deployed in the chemical area of their manufacturing department, where mobile work order functions reduced human errors and provided instant visibility of stock levels and work order statuses. The user-friendly interface facilitated quick adaptation by the manufacturing team, leading to a smooth transition and efficient use of the new technology.
Operational Impact
Quantitative Benefit
Case Study missing?
Start adding your own!
Register with your work email and create a new case study profile for your business.
Related Case Studies.
.png)
Case Study
Improving Vending Machine Profitability with the Internet of Things (IoT)
The vending industry is undergoing a sea change, taking advantage of new technologies to go beyond just delivering snacks to creating a new retail location. Intelligent vending machines can be found in many public locations as well as company facilities, selling different types of goods and services, including even computer accessories, gold bars, tickets, and office supplies. With increasing sophistication, they may also provide time- and location-based data pertaining to sales, inventory, and customer preferences. But at the end of the day, vending machine operators know greater profitability is driven by higher sales and lower operating costs.
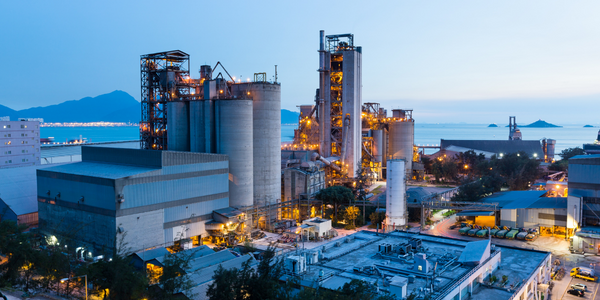
Case Study
Honeywell - Tata Chemicals Improves Data Accessibility with OneWireless
Tata was facing data accessibility challenges in the cement plant control room tapping signals from remote process control areas and other distant locations, including the gas scrubber. Tata needed a wireless solution to extend its control network securely to remote locations that would also provide seamless communication with existing control applications.

Case Study
Advanced Elastomer Systems Upgrades Production
In order to maintain its share of the international market for thermoplastic elastomers AES recently expanded its Florida plant by adding a new production line. While the existing lines were operating satisfactorily using a PROVOX distributed control system with traditional analog I/O, AES wanted advanced technology on the new line for greater economy, efficiency, and reliability. AES officials were anxious to get this line into production to meet incoming orders, but two hurricanes slowed construction.
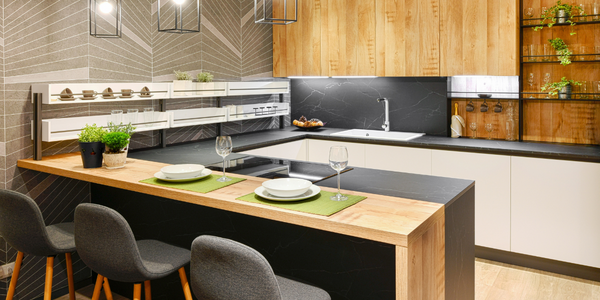
Case Study
Series Production with Lot-size-1 Flexibility
Nobilia manufactures customized fitted kitchens with a lot size of 1. They require maximum transparency of tracking design data and individual processing steps so that they can locate a particular piece of kitchen furniture in the sequence of processes.