Technology Category
- Drones - Multirotor Drones
Applicable Industries
- Aerospace
- Metals
Applicable Functions
- Product Research & Development
Use Cases
- Additive Manufacturing
- Rapid Prototyping
Services
- Drone Operation Services
- System Integration
About The Customer
Aeroswift is a project launched by Aerosud, a South African aviation manufacturing solutions provider, and the South African Council for Scientific and Industrial Research (CSIR). The project was initiated in 2011 with the aim of unlocking the potential of the growing additive manufacturing (AM) industry, improving market competitiveness, and providing South Africa with a unique competitive edge in metal AM. Aeroswift is known for its new generation of metal additive manufacturing (AM) system with a bigger build volume than ever before. The Aeroswift printer is capable of building large-scale 3D printed metal aircraft components in many metals, including titanium alloy, which is widely applied in the industry due to its combination of high performance and low weight.
The Challenge
The South African aviation manufacturing solutions provider Aerosud and the South African Council for Scientific and Industrial Research (CSIR) launched a challenging 3D printing project, Aeroswift, in 2011. The project aimed to unlock the potential of the growing additive manufacturing (AM) industry, improve market competitiveness, and provide South Africa with a unique competitive edge in metal AM. The challenge was to build a large metal Unmanned Aerial Vehicle (UAV) frame on the Aeroswift printer, while improving the buy-to-fly ratio and reducing development time and waste. The Aeroswift system was capable of printing much larger parts than ever before, and ten times faster than any other commercially available laser melting machine. However, to fully utilize its capabilities, Aeroswift needed a methodology for designing large additively manufactured products.
The Solution
Aeroswift collaborated with Altair to develop a methodology for designing large additively manufactured products. They used Altair Inspire, a software that enabled engineers to design a large UAV frame for manufacture on the Aeroswift machine. The design process included UAV flight requirement specifications, electronic component and drivetrain selection, mechanical design employing topology optimization techniques, aesthetic improvements, and manufacturability improvements. The engineers phased their topology optimization approach by running a first step optimization with increased branch sizes, to reduce the computational complexity in finding primary load paths. This process produced the thickness boundaries which encompassed the optimal design. The Aeroswift team then recreated the resulting geometry and ran a second stage topology optimization with thinner branches. This process transformed a very basic design into a topology optimized design suitable for metal AM.
Operational Impact
Quantitative Benefit
Case Study missing?
Start adding your own!
Register with your work email and create a new case study profile for your business.
Related Case Studies.
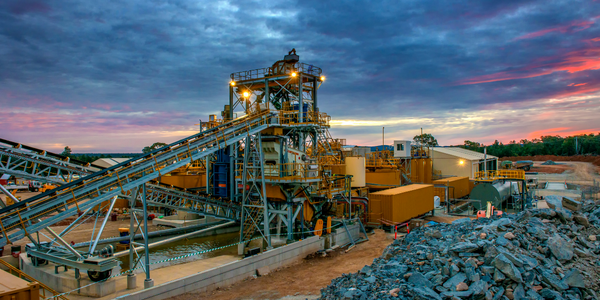
Case Study
Goldcorp: Internet of Things Enables the Mine of the Future
Goldcorp is committed to responsible mining practices and maintaining maximum safety for its workers. At the same time, the firm is constantly exploring ways to improve the efficiency of its operations, extend the life of its assets, and control costs. Goldcorp needed technology that can maximize production efficiency by tracking all mining operations, keep employees safe with remote operations and monitoring of hazardous work areas and control production costs through better asset and site management.
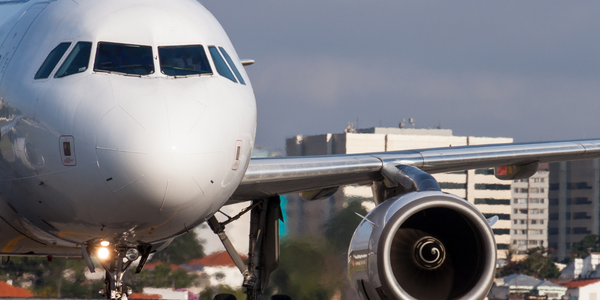
Case Study
Airbus Soars with Wearable Technology
Building an Airbus aircraft involves complex manufacturing processes consisting of thousands of moving parts. Speed and accuracy are critical to business and competitive advantage. Improvements in both would have high impact on Airbus’ bottom line. Airbus wanted to help operators reduce the complexity of assembling cabin seats and decrease the time required to complete this task.
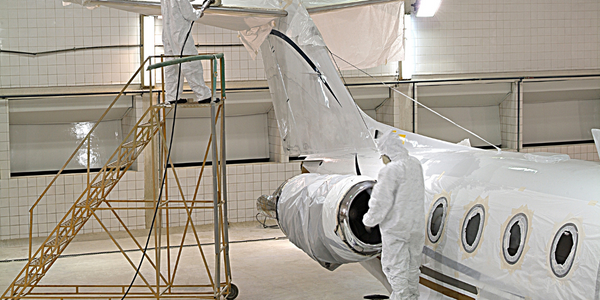
Case Study
Aircraft Predictive Maintenance and Workflow Optimization
First, aircraft manufacturer have trouble monitoring the health of aircraft systems with health prognostics and deliver predictive maintenance insights. Second, aircraft manufacturer wants a solution that can provide an in-context advisory and align job assignments to match technician experience and expertise.
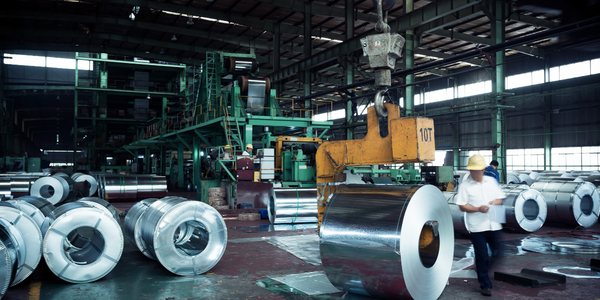
Case Study
KSP Steel Decentralized Control Room
While on-site in Pavlodar, Kazakhstan, the DAQRI team of Business Development and Solutions Architecture personnel worked closely with KSP Steel’s production leadership to understand the steel production process, operational challenges, and worker pain points.
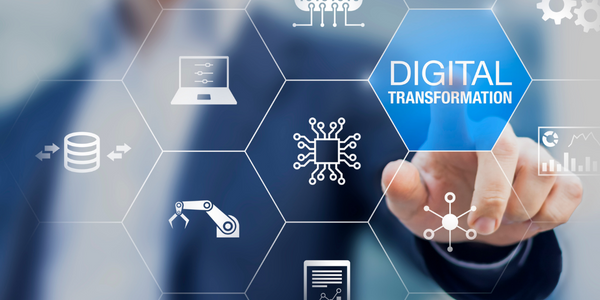
Case Study
Bluescope Steel on Path to Digitally Transform Operations and IT
Increasing competition and fluctuations in the construction market prompted BlueScope Steel to look toward digital transformation of its four businesses, including modern core applications and IT infrastructure. BlueScope needed to modernize its infrastructure and adopt new technologies to improve operations and supply chain efficiency while maintaining and updating an aging application portfolio.
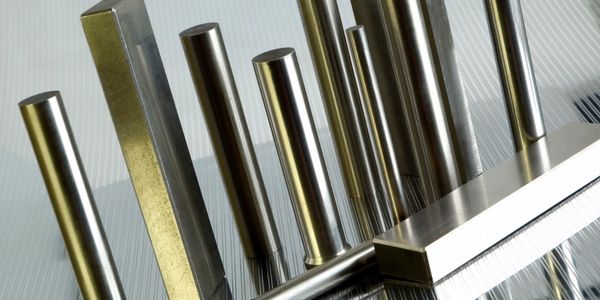
Case Study
RobotStudio Case Study: Benteler Automobiltechnik
Benteler has a small pipe business area for which they produce fuel lines and coolant lines made of aluminum for Porsche and other car manufacturers. One of the problems in production was that when Benteler added new products, production had too much downtime.