Company Size
1,000+
Country
- Worldwide
Product
- Gensuite Quality Management System software
Tech Stack
- Cloud-based software
Implementation Scale
- Enterprise-wide Deployment
Impact Metrics
- Cost Savings
- Productivity Improvements
Applicable Industries
- Automotive
Applicable Functions
- Quality Assurance
Services
- System Integration
- Training
About The Customer
The customer is a top mobility systems manufacturing and service company with a global footprint. They are a multinational company with facilities and customers all over the world. The company is committed to ensuring top quality products and services, which requires them to invest time, money, and energy to effectively capture and resolve quality issues. They were in need of a quality management software system to streamline the logging of nonconformities and other quality-related issues, improve issue resolution, and increase visibility between field technicians and quality managers.
The Challenge
The multinational company, a top mobility systems manufacturing and service company with a global footprint, needed a quality management software system to streamline the logging of nonconformities and other quality-related issues. They wanted to improve issue resolution by establishing an efficient process and increase visibility between field technicians and quality managers. They also required in-depth system training. The company needed an intuitive interface for enterprise-wide deployment, mobile capabilities for deployment within multiple facilities, and integrated data analytics & reporting for continuous improvement.
The Solution
The company deployed Gensuite’s Quality Management suite of cloud-based software applications. This enabled users to meet quality program expectations and deliver to customer standards throughout the entire production and distribution lifecycle. The software allowed them to plan, publish and measure facilities to established organizational quality program expectations with appropriate follow-up and responsibility tracking. Staff could engage in key quality program activities such as compliance tasks, auditing, issue identification, Corrective and Preventative Action, etc. and be notified through automated alerts and reminders. Defects could be recorded via Mobile and online reporting, and Root Cause Analysis activities surrounding defect resolution could be tracked and managed. The software also provided the ability to report and analyze data and key performance indicators by site or across the company through flexible and customizable reporting and data analytics capabilities.
Operational Impact
Quantitative Benefit
Case Study missing?
Start adding your own!
Register with your work email and create a new case study profile for your business.
Related Case Studies.
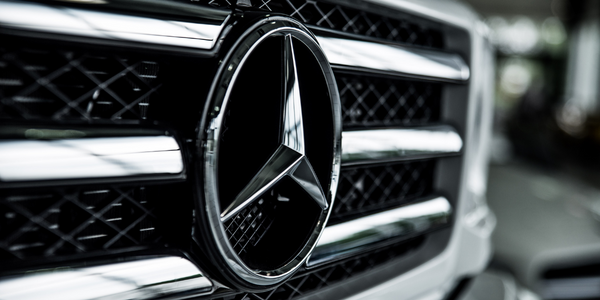
Case Study
Integral Plant Maintenance
Mercedes-Benz and his partner GAZ chose Siemens to be its maintenance partner at a new engine plant in Yaroslavl, Russia. The new plant offers a capacity to manufacture diesel engines for the Russian market, for locally produced Sprinter Classic. In addition to engines for the local market, the Yaroslavl plant will also produce spare parts. Mercedes-Benz Russia and his partner needed a service partner in order to ensure the operation of these lines in a maintenance partnership arrangement. The challenges included coordinating the entire maintenance management operation, in particular inspections, corrective and predictive maintenance activities, and the optimizing spare parts management. Siemens developed a customized maintenance solution that includes all electronic and mechanical maintenance activities (Integral Plant Maintenance).
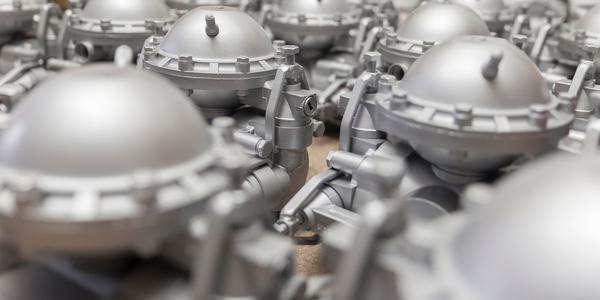
Case Study
Monitoring of Pressure Pumps in Automotive Industry
A large German/American producer of auto parts uses high-pressure pumps to deburr machined parts as a part of its production and quality check process. They decided to monitor these pumps to make sure they work properly and that they can see any indications leading to a potential failure before it affects their process.