Technology Category
- Analytics & Modeling - Digital Twin / Simulation
- Infrastructure as a Service (IaaS) - Cloud Storage Services
Applicable Industries
- Cement
- Construction & Infrastructure
Applicable Functions
- Procurement
- Product Research & Development
Use Cases
- Construction Management
- Digital Twin
About The Customer
AAEngineering is a leading engineering, procurement, and construction company that specializes in delivering complex projects in challenging environments. In this case, they were tasked with the design and construction of a gold processing plant in the seismic Talas region of Kyrgyzstan. The project was part of Kyrgyzstan's efforts to create a closed cycle of gold production, where both the extraction and processing of ore is carried out within their country. The USD 75 million project required construction of the main factory building along with ancillary services infrastructure, including a crushing and screening complex, a laboratory, storage pond, tailings storage facility, poison and ore storage areas, shift camps for operating personnel, and new roadways and accesses.
The Challenge
AAEngineering was tasked with the design and construction of a gold processing plant in the seismic Talas region of Kyrgyzstan, amid a global pandemic. The USD 75 million project was located at an altitude of 3,500-meters in a dangerously seismic area with seismicity up to 10 magnitudes and increased risk of avalanches due to slopes reaching 75 degrees. The project location presented extreme conditions and was subject to strict environmental standards. In addition to the geographical and geological complications, AAEngineering had to also overcome technical, engineering, and coordination challenges among the globally dispersed project team, as well as accommodate the limited construction period. The area has a very short construction season, lasting only four or five months. It rains the rest of the time. They sought to simultaneously organize and perform multidiscipline design and construction works. To carry out these processes concurrently required integrated digital workflows and accurate modeling and analysis applications for visualization and simulation.
The Solution
AAEngineering utilized Bentley’s digital applications to propose several design options for the various facilities to the client, as well as provide an economic analysis for each alternative. They used digital technology to go beyond conventional engineering methods. They surveyed the numerous areas with quadcopters and built digital terrain models using ContextCapture. Upon winning the project bid, they set up the structure for execution and selected ProjectWise as the coordinated platform to share project information in an open, connected data environment, optimizing communication and scheduling among 500 work sites. They modeled the facility construction sites and access roads using OpenRoads Designer, defining maximum safe traffic speeds and visibility zones, critical in the highlands. They carried out the architectural and structural design using OpenBuildings Designer and ProStructures. The interoperability of ProStructures with third-party software enabled all steel and concrete components to be exported without losing information. They also modeled a drainage channel to drain water and bypass the tailings dump. PLAXIS provided the geotechnical analysis that was necessary for them to optimize design of the drainage network and ensure stability of the tailings and storage pond dams.
Operational Impact
Quantitative Benefit
Case Study missing?
Start adding your own!
Register with your work email and create a new case study profile for your business.
Related Case Studies.

Case Study
System 800xA at Indian Cement Plants
Chettinad Cement recognized that further efficiencies could be achieved in its cement manufacturing process. It looked to investing in comprehensive operational and control technologies to manage and derive productivity and energy efficiency gains from the assets on Line 2, their second plant in India.

Case Study
IoT System for Tunnel Construction
The Zenitaka Corporation ('Zenitaka') has two major business areas: its architectural business focuses on structures such as government buildings, office buildings, and commercial facilities, while its civil engineering business is targeted at structures such as tunnels, bridges and dams. Within these areas, there presented two issues that have always persisted in regard to the construction of mountain tunnels. These issues are 'improving safety" and "reducing energy consumption". Mountain tunnels construction requires a massive amount of electricity. This is because there are many kinds of electrical equipment being used day and night, including construction machinery, construction lighting, and ventilating fan. Despite this, the amount of power consumption is generally not tightly managed. In many cases, the exact amount of power consumption is only ascertained when the bill from the power company becomes available. Sometimes, corporations install demand-monitoring equipment to help curb the maximum power demanded. However, even in these cases, the devices only allow the total volume of power consumption to be ascertained, or they may issue warnings to prevent the contracted volume of power from being exceeded. In order to tackle the issue of reducing power consumption, it was first necessary to obtain an accurate breakdown of how much power was being used in each particular area. In other words, we needed to be able to visualize the amount of power being consumed. Safety, was also not being managed very rigorously. Even now, tunnel construction sites often use a 'name label' system for managing entry into the work site. Specifically, red labels with white reverse sides that bear the workers' names on both sides are displayed at the tunnel work site entrance. The workers themselves then flip the name label to the appropriate side when entering or exiting from the work site to indicate whether or not they are working inside the tunnel at any given time. If a worker forgets to flip his or her name label when entering or exiting from the tunnel, management cannot be performed effectively. In order to tackle the challenges mentioned above, Zenitaka decided to build a system that could improve the safety of tunnel construction as well as reduce the amount of power consumed. In other words, this new system would facilitate a clear picture of which workers were working in each location at the mountain tunnel construction site, as well as which processes were being carried out at those respective locations at any given time. The system would maintain the safety of all workers while also carefully controlling the electrical equipment to reduce unnecessary power consumption. Having decided on the concept, our next concern was whether there existed any kind of robust hardware that would not break down at the construction work site, that could move freely in response to changes in the working environment, and that could accurately detect workers and vehicles using radio frequency identification (RFID). Given that this system would involve many components that were new to Zenitaka, we decided to enlist the cooperation of E.I.Sol Co., Ltd. ('E.I.Sol') as our joint development partner, as they had provided us with a highly practical proposal.
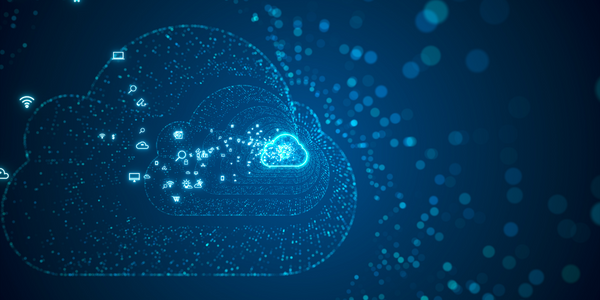
Case Study
Splunk Partnership Ties Together Big Data & IoT Services
Splunk was faced with the need to meet emerging customer demands for interfacing IoT projects to its suite of services. The company required an IoT partner that would be able to easily and quickly integrate with its Splunk Enterprise platform, rather than allocating development resources and time to building out an IoT interface and application platform.
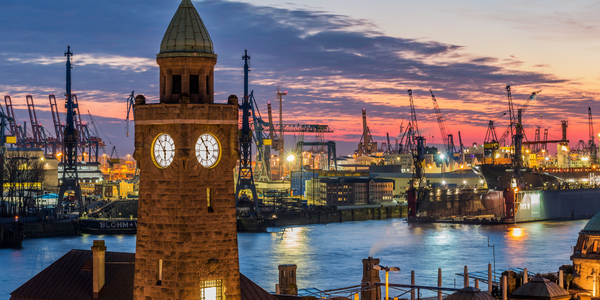
Case Study
Bridge monitoring in Hamburg Port
Kattwyk Bridge is used for both rail and road transport, and it has played an important role in the Port of Hamburg since 1973. However, the increasing pressure from traffic requires a monitoring solution. The goal of the project is to assess in real-time the bridge's status and dynamic responses to traffic and lift processes.
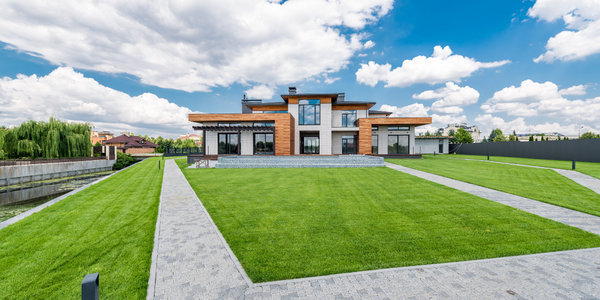
Case Study
Bellas Landscaping
Leading landscaping firm serving central Illinois streamlines operations with Samsara’s real-time fleet tracking solution: • 30+ vehicle fleet includes International Terrastar dump trucks and flatbeds, medium- and light-duty pickups from Ford and Chevrolet. Winter fleet includes of snow plows and salters.