Customer Company Size
Large Corporate
Country
- Worldwide
Product
- IBM Operational Decision Management
Tech Stack
- COBOL-based applications
- ERP system
Implementation Scale
- Enterprise-wide Deployment
Impact Metrics
- Productivity Improvements
- Digital Expertise
Technology Category
- Application Infrastructure & Middleware - API Integration & Management
Applicable Industries
- Automotive
Applicable Functions
- Discrete Manufacturing
- Business Operation
Use Cases
- Manufacturing System Automation
Services
- System Integration
- Training
About The Customer
The company in the case study is a manufacturer of commercial trucks, buses, recreational vehicles (RVs), defense vehicles and engines. In addition to manufacturing, the company also provides aftermarket support and financing services. The company has a global presence with operations worldwide. As part of its IT strategy, the company wanted to make fundamental changes. It aimed to replace silos with enterprise-wide applications and create a greater alignment between business requirements and the IT department. The company's core ERP system relied on numerous COBOL-based applications for processing, which were challenging and time-consuming to change.
The Challenge
The organization wanted to make fundamental changes to its IT strategy. It sought to replace silos with enterprisewide applications and create greater alignment between business requirements and the IT department. As part of this transformation, the company needed to change the way it handled business rules. Its core ERP system relied on numerous COBOL-based applications for processing. Making changes to these applications could be tricky; they were poorly documented and the company had a shrinking pool of resources available to manage them. The organization began looking for a more flexible, responsive business rules solution that would enable it to get new and updated business rules to production quickly.
The Solution
The business considered solutions from multiple vendors before deciding to engage IBM to perform a Quick Win Pilot using IBM® Operational Decision Management software. IBM did codevelopment with the company and then helped them size their environment because it’s a centralized decision-making environment where all the manufacturing applications — not only financial applications but warranty applications, engineering applications or sales applications — can coexist in one central location so that they can leverage the environment itself. And IBM laid out the training plan for them. With Operational Decision Management software, users can divide business rules into services, which then integrate with the organization’s service-oriented architecture (SOA), facilitating reuse. Users can search for rules, modify them and reuse them. Further, if necessary, users can revert to previous versions of the rule and access a complete history of the changes other users have made to it.
Operational Impact
Quantitative Benefit
Case Study missing?
Start adding your own!
Register with your work email and create a new case study profile for your business.
Related Case Studies.
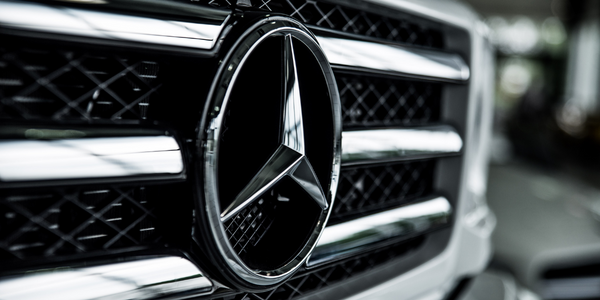
Case Study
Integral Plant Maintenance
Mercedes-Benz and his partner GAZ chose Siemens to be its maintenance partner at a new engine plant in Yaroslavl, Russia. The new plant offers a capacity to manufacture diesel engines for the Russian market, for locally produced Sprinter Classic. In addition to engines for the local market, the Yaroslavl plant will also produce spare parts. Mercedes-Benz Russia and his partner needed a service partner in order to ensure the operation of these lines in a maintenance partnership arrangement. The challenges included coordinating the entire maintenance management operation, in particular inspections, corrective and predictive maintenance activities, and the optimizing spare parts management. Siemens developed a customized maintenance solution that includes all electronic and mechanical maintenance activities (Integral Plant Maintenance).
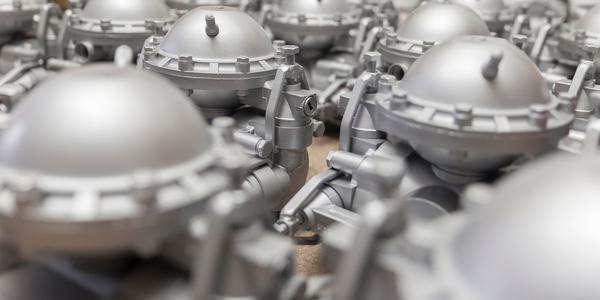
Case Study
Monitoring of Pressure Pumps in Automotive Industry
A large German/American producer of auto parts uses high-pressure pumps to deburr machined parts as a part of its production and quality check process. They decided to monitor these pumps to make sure they work properly and that they can see any indications leading to a potential failure before it affects their process.