Company Size
1,000+
Region
- America
Country
- United States
Product
- Intelex Sustainability Performance Indicators
- Intelex Communication Management
- Intelex Audit Management for EHS
- Intelex Meetings Management
- Intelex Action Plans
- Intelex Job Safety Analysis
- Intelex EHS Incident Management
Tech Stack
- Digital Transformation
- Data Analytics
Implementation Scale
- Enterprise-wide Deployment
Impact Metrics
- Productivity Improvements
- Waste Reduction
Technology Category
- Analytics & Modeling - Real Time Analytics
- Application Infrastructure & Middleware - Data Exchange & Integration
Applicable Industries
- Metals
Applicable Functions
- Discrete Manufacturing
- Quality Assurance
Use Cases
- Manufacturing System Automation
- Predictive Maintenance
Services
- Data Science Services
- System Integration
About The Customer
Kloeckner Metals Corporation is a subsidiary of Klöckner & Co. of Duisburg, Germany. Based in Roswell, Georgia, it is a distributor of steel and non-ferrous metals. The company supports customers and suppliers with innovative metal solutions and strives to go beyond mere delivery of products. Kloeckner Metals Corporation is a full-line manufacturing, production and service center business specializing in metals industries, including hot-roll products, structural materials, sheets, pipes and plates. The company employs approximately 2,200 people and includes a 20-member environment, health and safety (EHS) team of 11 corporate and nine branch-dedicated professionals. As a pioneer of digital transformation in the steel industry, the company is striving to fully digitalize and largely automate the supply and service chain.
The Challenge
Kloeckner Metals Corporation, a full-line manufacturing, production and service center business specializing in metals industries, was seeking a solution to streamline its processes and make it easier for branch operations to meet the company’s environmental health and safety (EHS) objectives. In 2017, the company was using multiple EHS systems to track incidents, perform corrective actions, hold safety meetings, perform job hazard analyses, and run other EHS programs. Each system was disparate and there was no interoperability. Kloeckner wanted to consolidate these workflows, close the loop on both corrective actions and audit recommendations, and enhance its overall EHS processes.
The Solution
Kloeckner began discussions with Intelex in 2017. Solution development and implementation started a year later and was performed in two stages. Phase 1 introduced Intelex Sustainability Performance Indicators, Communication Management, Audit Management for EHS, Meetings Management, Action Plans and Job Safety Analysis. Phase 2 introduced Intelex EHS Incident Management and was rolled out during May 2019. With Intelex, Kloeckner introduced a single integrated system that achieved full user acceptance and helped the company meet its overall goals, including the elimination of redundant claims reporting to its insurance carrier. After successfully implementing the Intelex EHS Incident Management application and sharing it with Kloeckner’s operations, a new opportunity presented itself. The company’s controlling and operations functions used a paper-based capital expenditure request and approval process that was extremely time-consuming.
Operational Impact
Quantitative Benefit
Case Study missing?
Start adding your own!
Register with your work email and create a new case study profile for your business.
Related Case Studies.
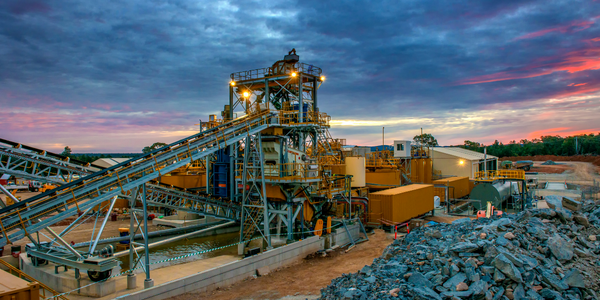
Case Study
Goldcorp: Internet of Things Enables the Mine of the Future
Goldcorp is committed to responsible mining practices and maintaining maximum safety for its workers. At the same time, the firm is constantly exploring ways to improve the efficiency of its operations, extend the life of its assets, and control costs. Goldcorp needed technology that can maximize production efficiency by tracking all mining operations, keep employees safe with remote operations and monitoring of hazardous work areas and control production costs through better asset and site management.
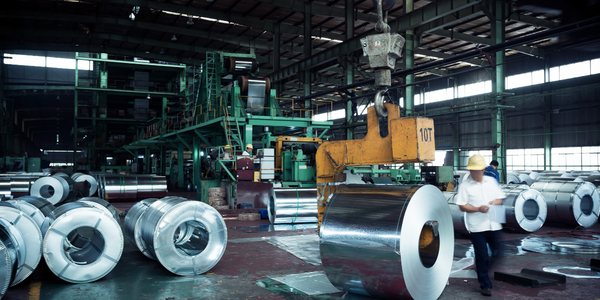
Case Study
KSP Steel Decentralized Control Room
While on-site in Pavlodar, Kazakhstan, the DAQRI team of Business Development and Solutions Architecture personnel worked closely with KSP Steel’s production leadership to understand the steel production process, operational challenges, and worker pain points.
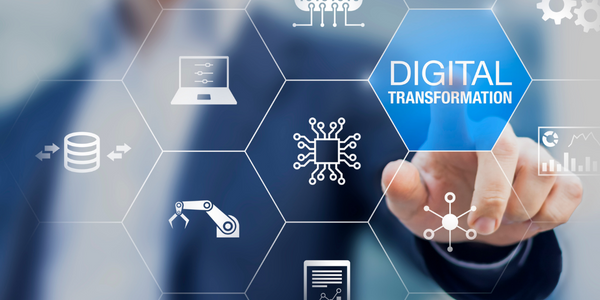
Case Study
Bluescope Steel on Path to Digitally Transform Operations and IT
Increasing competition and fluctuations in the construction market prompted BlueScope Steel to look toward digital transformation of its four businesses, including modern core applications and IT infrastructure. BlueScope needed to modernize its infrastructure and adopt new technologies to improve operations and supply chain efficiency while maintaining and updating an aging application portfolio.
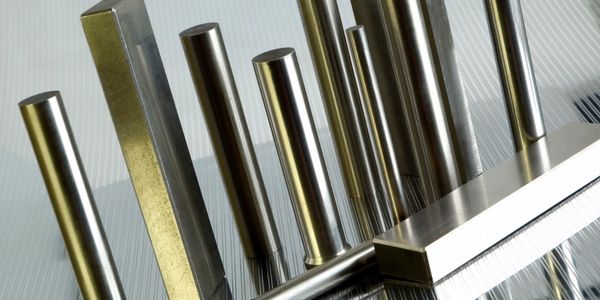
Case Study
RobotStudio Case Study: Benteler Automobiltechnik
Benteler has a small pipe business area for which they produce fuel lines and coolant lines made of aluminum for Porsche and other car manufacturers. One of the problems in production was that when Benteler added new products, production had too much downtime.
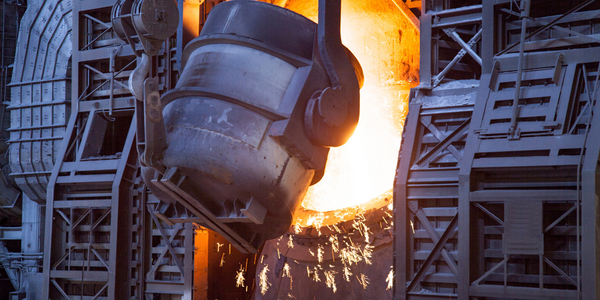
Case Study
Continuous Casting Machines in a Steel Factory
With a very broad range of applications, steel is an important material and has been developed into the most extensive alloy in the engineering world. Since delivering high quality is absolutely crucial for steel plants, ensuring maximum productivity and the best quality production are the keys to competitiveness in the steel industry. Additionally, working conditions in steel factories are not suitable for workers to stay in for long periods of time, so manufactures usually adopt various machines to complete the steel production processes. However, the precision of these machines is often overestimated and the lack of flexibility also makes supervisors unable to adjust operating procedures. A renowned steel factory in Asia planned to improve its Distributed Control System (DCS) of furnaces as well as addressing the problem of insufficient accuracy. However, most well-known international equipment suppliers can not provide a satisfactory solution and local maintenance because the project needed new technologies to more accurately control equipment operations. By implementing Advantech’s automated monitoring and control solution, steel factories can not only improve the manufacturing processes but can also allow users to add additional functions to the existing system so as to make sure the operation runs at high efficiency.
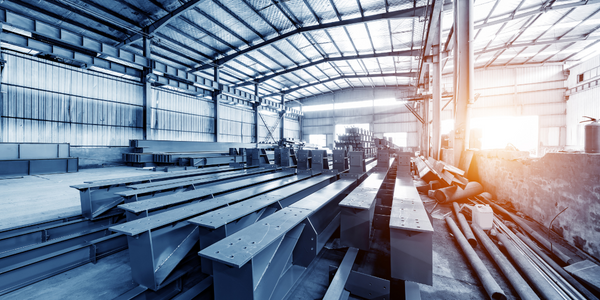
Case Study
Automated Predicitive Analytics For Steel/Metals Industry
Asset to be monitored: Wire Compactor that produces Steel RebarCustomer Faced The Following Challenges:Dependent upon machine uptime.Pressure cylinders within the compactor fail to control compression and speed causing problems in binding the coil.Equipment failure occurs in the final stage of production causing the entire line to stop, can you say bottleneck?Critical asset unequipped with sensors to produce data.