Technology Category
- Analytics & Modeling - Real Time Analytics
- Functional Applications - Transportation Management Systems (TMS)
Applicable Industries
- Automotive
- Transportation
Applicable Functions
- Logistics & Transportation
Use Cases
- Real-Time Location System (RTLS)
- Supply Chain Visibility
Services
- System Integration
About The Customer
4flow is a leading global provider of supply chain consulting, software and fourth party logistics (4PL) services. The company carries out more than 200 projects with clients all over the world each year. As a neutral 4PL, 4flow management handles the continuous planning, optimization, and management of a large number of transportation networks and global end-to-end supply chains on behalf of small to medium-sized companies as well as internationally operating companies representing a range of industry verticals. These include automotive, machinery manufacturing, consumer packaged goods and retail, life science and high tech. With over 700 employees, 4flow is a global partner for its customers at 17 locations in Europe, Asia, and in North and South America. The company’s global headquarters is in Berlin, Germany.
The Challenge
4flow, a leading global provider of supply chain consulting, software and fourth party logistics (4PL) services, was facing a significant challenge. The company was dealing with rapidly increasing deviations from previously planned transport processes. Early detection of these deviations was crucial to avoid additional costs and maintain efficiency. However, without real-time data, achieving absolute supply chain visibility was a daunting task. As a neutral 4PL that is not fleet-based, 4flow did not have access to real-time transportation data. The lack of visibility resulted in inefficiencies and increased costs from deviations and exceptions, such as late penalties and dispute management costs. In the worst cases, it led to extended supply chain disruptions. Late identified delays meant the time needed to take preventative measures was lost, potentially leading to late fees and penalties. Manual communication between carriers, customers and transport planners was also required if shipping status data was not automatically exchanged between supply chain partners.
The Solution
To address these challenges, 4flow partnered with Shippeo to implement real-time tracking information into the 4flow integrated transportation management system (iTMS). Shippeo’s real-time transportation visibility allowed 4flow to increase supply chain transparency and leverage data to boost efficiencies for shippers, carriers, and end customers. The integration of real-time tracking information into 4flow’s IT system created the data layer necessary to identify deviations much earlier, thus reducing additional costs and unlocking the productivity and service benefits of real-time tracking. Now, 4flow’s transport execution teams can instantly trace a single part right down to the truck carrying it. The information and transparency gained can be shared with customers at any time. This real-time data and optimized estimated time of arrival (ETA) calculation, combined with 4flow’s deep understanding of supply chain optimization, are helping to build more resilient and efficient supply chains for 4flow and Shippeo’s joint customers.
Operational Impact
Quantitative Benefit
Case Study missing?
Start adding your own!
Register with your work email and create a new case study profile for your business.
Related Case Studies.
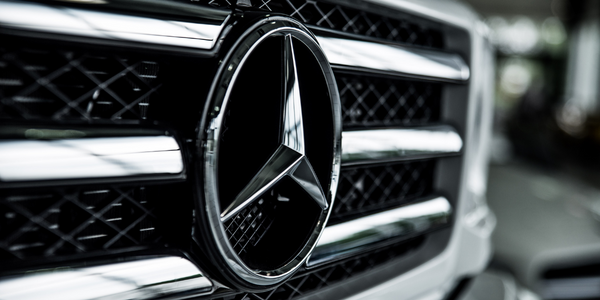
Case Study
Integral Plant Maintenance
Mercedes-Benz and his partner GAZ chose Siemens to be its maintenance partner at a new engine plant in Yaroslavl, Russia. The new plant offers a capacity to manufacture diesel engines for the Russian market, for locally produced Sprinter Classic. In addition to engines for the local market, the Yaroslavl plant will also produce spare parts. Mercedes-Benz Russia and his partner needed a service partner in order to ensure the operation of these lines in a maintenance partnership arrangement. The challenges included coordinating the entire maintenance management operation, in particular inspections, corrective and predictive maintenance activities, and the optimizing spare parts management. Siemens developed a customized maintenance solution that includes all electronic and mechanical maintenance activities (Integral Plant Maintenance).
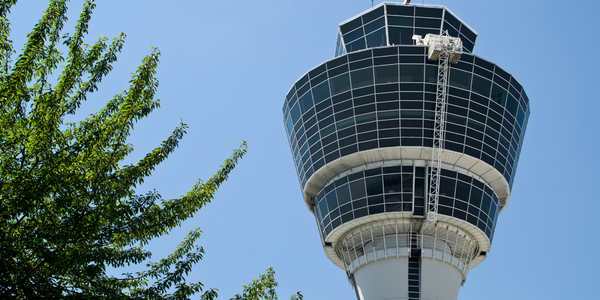
Case Study
Airport SCADA Systems Improve Service Levels
Modern airports are one of the busiest environments on Earth and rely on process automation equipment to ensure service operators achieve their KPIs. Increasingly airport SCADA systems are being used to control all aspects of the operation and associated facilities. This is because unplanned system downtime can cost dearly, both in terms of reduced revenues and the associated loss of customer satisfaction due to inevitable travel inconvenience and disruption.
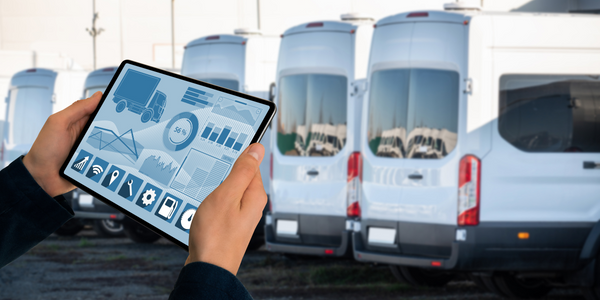
Case Study
IoT-based Fleet Intelligence Innovation
Speed to market is precious for DRVR, a rapidly growing start-up company. With a business model dependent on reliable mobile data, managers were spending their lives trying to negotiate data roaming deals with mobile network operators in different countries. And, even then, service quality was a constant concern.
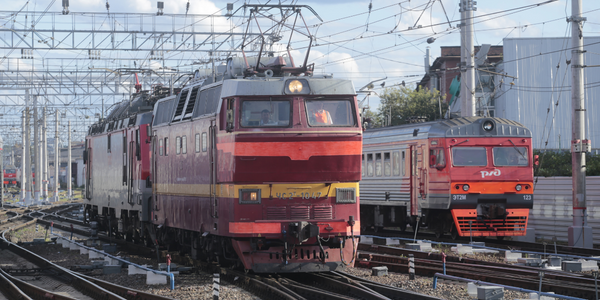
Case Study
Digitize Railway with Deutsche Bahn
To reduce maintenance costs and delay-causing failures for Deutsche Bahn. They need manual measurements by a position measurement system based on custom-made MEMS sensor clusters, which allow autonomous and continuous monitoring with wireless data transmission and long battery. They were looking for data pre-processing solution in the sensor and machine learning algorithms in the cloud so as to detect critical wear.