Technology Category
- Analytics & Modeling - Data-as-a-Service
- Analytics & Modeling - Predictive Analytics
Applicable Industries
- Automotive
- Finance & Insurance
Applicable Functions
- Quality Assurance
- Sales & Marketing
Use Cases
- Fraud Detection
- Inventory Management
Services
- Data Science Services
About The Customer
RCI Bank and Services is the financial services brand of the Renault Group. This French multinational operates in the automotive industry and is a result of the Renault-Nissan Alliance, which includes several other brands including Renault, Dacia, Nissan, and Infiniti. With over 50 years in the automotive-specific financial products and services sector, RCI supports dealers in sales processes where company brands need financing. RCI has developed a strategy of diversifying its offering, adapting to the actual requirements of its customers, guaranteeing the highest quality standards and after-sales satisfaction. They offer their services to individuals and companies that want to take advantage of the credit facilities and financing available.
The Challenge
RCI Bank and Services, the financial services brand of the Renault Group, was facing challenges in data management and digitization. The company was using Microsoft Excel for pricing, risk calculation, sales forecasts, results forecasting, and debt recovery. This limited their capacity for innovation and the implementation of new projects. They also had multiple solutions in place, including an SAS-trained credit scoring tool, an Oracle data warehouse, an ad hoc ERP, Business Objects for operational BI reporting, and SalesForce as a CRM tool, plus SAP for accounting. The company also had some in-house applications for ETL and web analytics. However, the data from all these tools was dispersed, preventing the RCI team from working consistently.
The Solution
RCI Bank and Services decided to implement Alteryx, a data management tool, after seeing its capabilities in a use case from the Management Control Department. Alteryx simplified workflow management and the creation of new workflow tasks, reducing the generation of long lines of code by simply clicking and dragging a box. The main users of Alteryx technology are the Data Team and the Risk Department, as well as people who work on the most complex projects. The implementation of Alteryx democratized ETL tools and Data Science in general, which was previously inaccessible for many people. The technology unified data and made it easily accessible to all departments in the organization. As a result, the company became 10 times more agile and adopted a flexible working methodology that increased productivity. RCI went from using 5 data applications to managing more than 30 in parallel.
Operational Impact
Quantitative Benefit
Case Study missing?
Start adding your own!
Register with your work email and create a new case study profile for your business.
Related Case Studies.
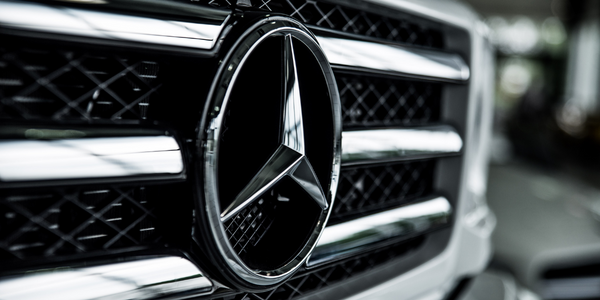
Case Study
Integral Plant Maintenance
Mercedes-Benz and his partner GAZ chose Siemens to be its maintenance partner at a new engine plant in Yaroslavl, Russia. The new plant offers a capacity to manufacture diesel engines for the Russian market, for locally produced Sprinter Classic. In addition to engines for the local market, the Yaroslavl plant will also produce spare parts. Mercedes-Benz Russia and his partner needed a service partner in order to ensure the operation of these lines in a maintenance partnership arrangement. The challenges included coordinating the entire maintenance management operation, in particular inspections, corrective and predictive maintenance activities, and the optimizing spare parts management. Siemens developed a customized maintenance solution that includes all electronic and mechanical maintenance activities (Integral Plant Maintenance).
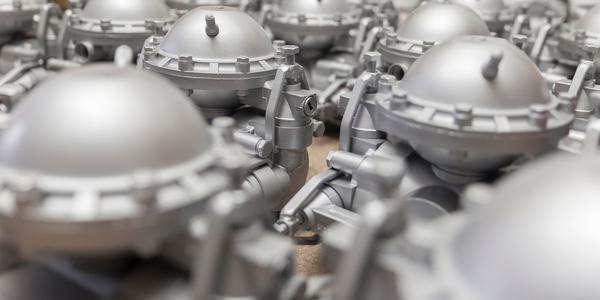
Case Study
Monitoring of Pressure Pumps in Automotive Industry
A large German/American producer of auto parts uses high-pressure pumps to deburr machined parts as a part of its production and quality check process. They decided to monitor these pumps to make sure they work properly and that they can see any indications leading to a potential failure before it affects their process.