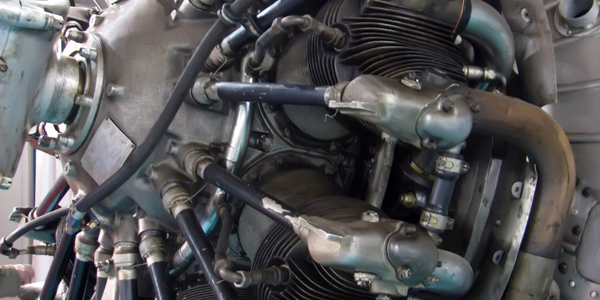
- Analytics & Modeling - Virtual & Augmented Reality Software
- Networks & Connectivity - WiFi
- Wearables - Augmented Reality Glasses, Headsets & Controllers
- Aerospace
- Discrete Manufacturing
- Augmented Reality
GE Aviation loses millions of dollars each year to errors made at key points during the assembly and overhaul of its engines. The costs show up in lost productivity, delays in testing, delays in customer deliveries, and the man-hours required to troubleshoot and correct faults. If errors arenʼt detected until after the engines are sent to customers, the repair costs exponentially increase.
B-nuts are one such key manufacturing point. They play a critical role in aircraft engine fluid lines and hoses, providing a sturdy, reliable seal―but only if tightened and torqued properly. If not torqued properly, there will be a need for a maintenance do-over, cancelled flight, or even an in-flight shut down.
GE Aviation initiated a deployment of AR that combined three technologies: Skylight from Upskill, Glass Enterprise Edition smart glasses, and a Wi-Fi-enabled Atlas-Copco Saltus MWR-85TA torque wrench.
Using Skylight on Glass, mechanics receive step-by-step guided instructions and images directly within their line of sight while performing different maintenance tasks. As the mechanics move through standard procedures and come to a step where they need to apply the torque wrench, Skylight alerts them through the smart glasses and then verifies the correct value in real-time before the mechanic can move on.
Case Study missing?
Start adding your own!
Register with your work email and create a new case study profile for your business.
Related Case Studies.
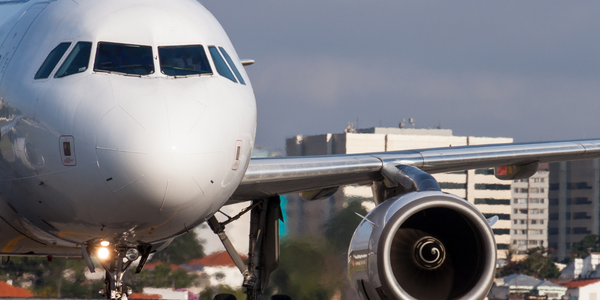
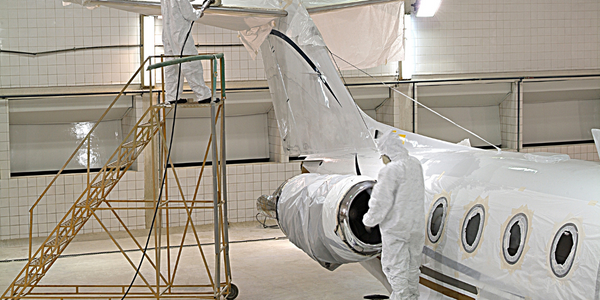
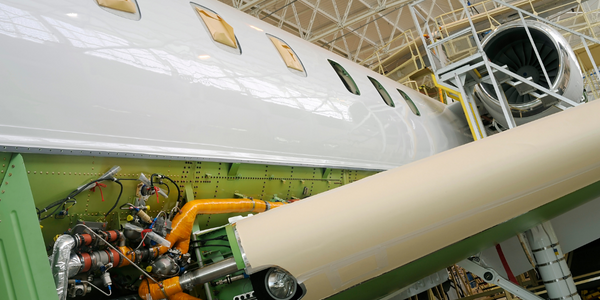
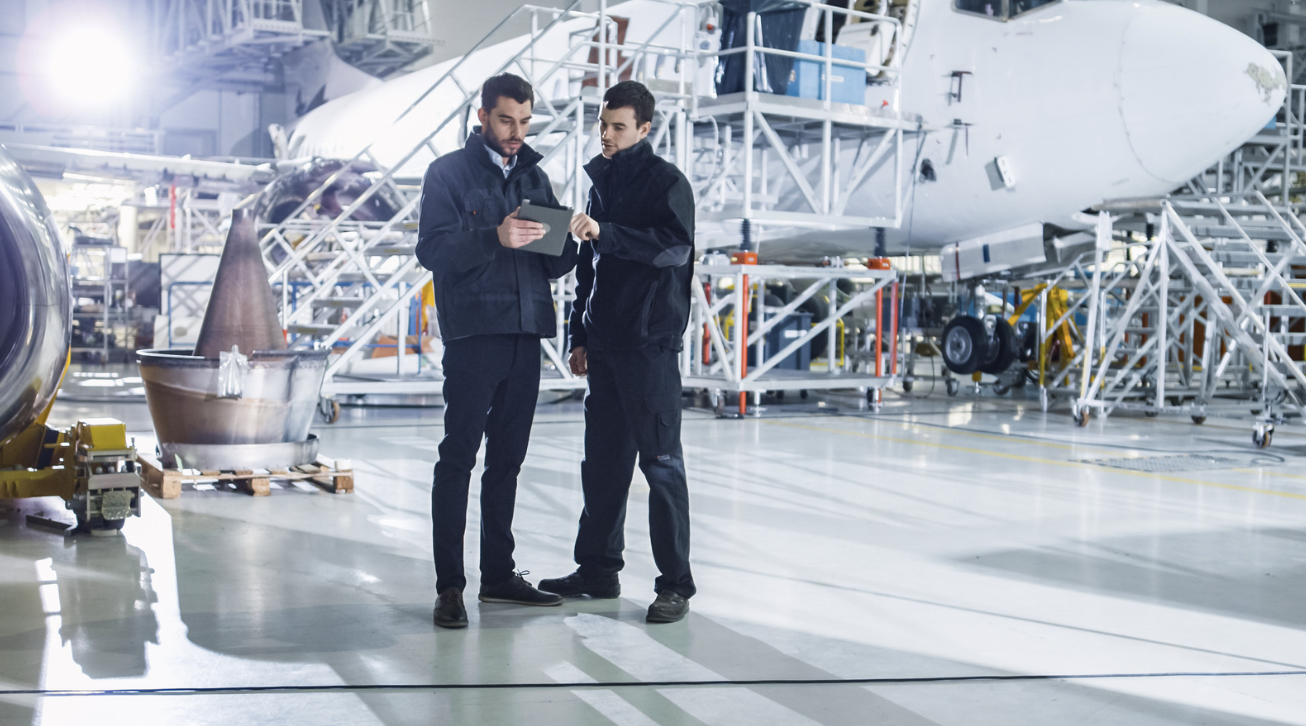
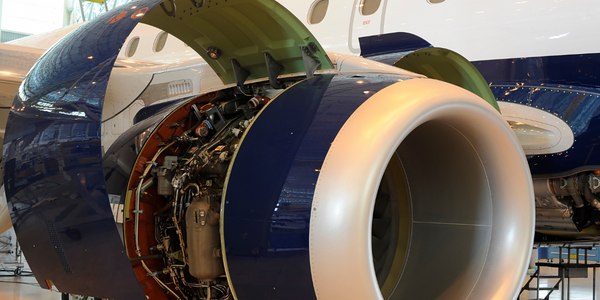